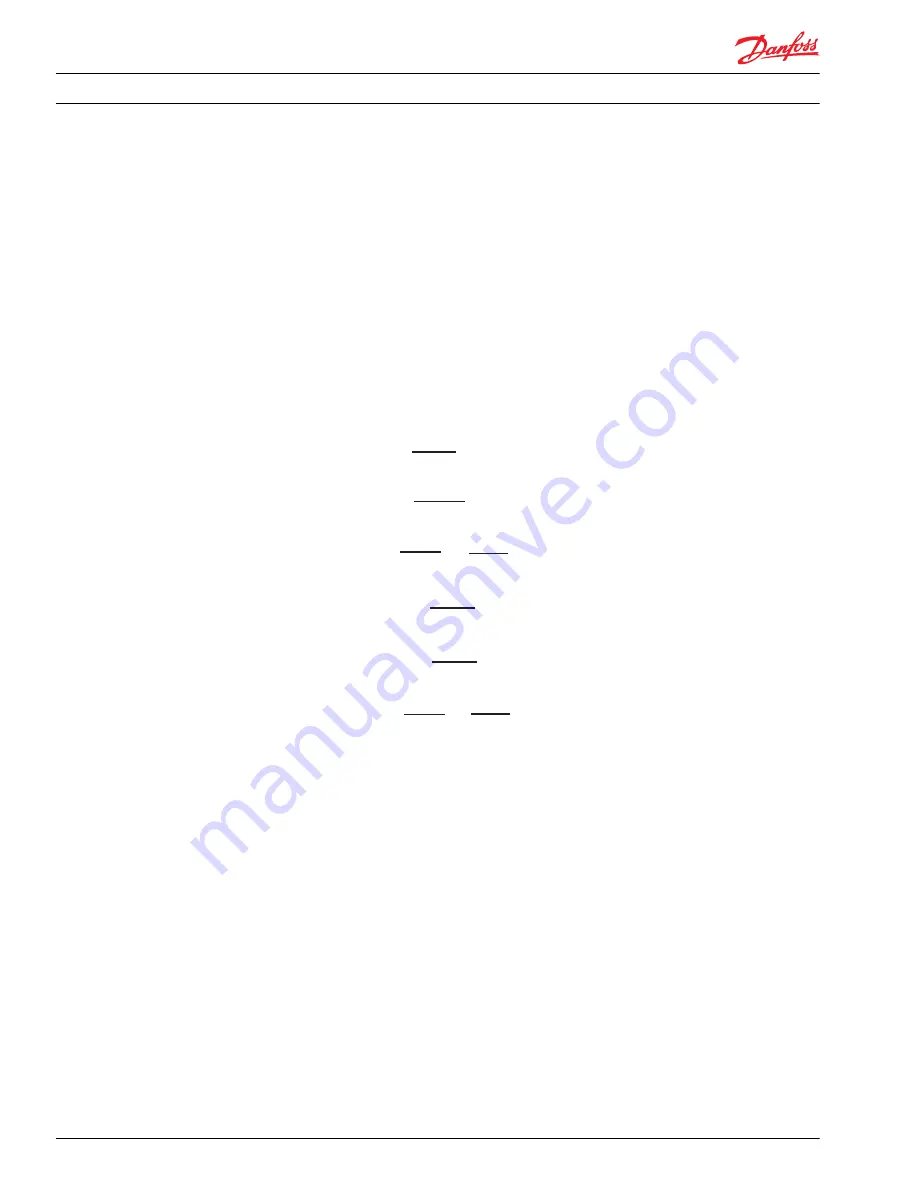
•
Use flexible hoses.
•
Limit system line length.
•
If possible, optimize system line position to minimize noise.
•
If you must use steel plumbing, clamp the lines.
•
If you add additional support, use rubber mounts.
•
Test for resonants in the operating range; if possible avoid them.
Sizing Equations
The following equations are helpful when sizing hydraulic pumps. Generally, the sizing process is
initiated by an evaluation of the machine system to determine the required motor speed and torque to
perform the necessary work function. Refer to
Selection of drive line components
, BLN-9885, for a more
complete description of hydrostatic drive line sizing. First, the motor is sized to transmit the maximum
required torque. The pump is then selected as a flow source to achieve the maximum motor speed.
Output f ow Q =
(l/min..)
Input torque M =
(N•m)
Input power P =
=
(kW)
SI units
V
g
= Displacement per revolution
(cm
3
/rev)
∆p = p
O
- p
i
(system pressure)
(bar)
n = Speed (min
-1
(rpm))
η
v
= Volumetric eff ciency
η
m
= Mechanical eff ciency
η
t
= Overall eff ciency (η
v
• η
m
)
V
g
• n • η
v
1000
V
g
• ∆p
20 • π • η
m
Q • ∆p
600 • η
t
M • n • π
30 000
US units
V
g
= Displacement per revolution
(in
3
/rev)
∆p = p
O
- p
i
(system pressure)
(psi)
n = Speed (min
-1
(rpm))
η
v
= Volumetric eff ciency
η
m
= Mechanical eff ciency
η
t
= Overall eff ciency (η
v
• η
m
)
Output f ow Q =
(US gal/min..)
Input torque M =
(lbf•in)
Input power P =
=
(hp)
V
g
• n • η
v
231
V
g
• ∆p
2 • π • η
m
Q • ∆p
1714 • η
t
M • n • π
198 000
Mounting Flange Loads
Adding tandem mounted auxiliary pumps and/or subjecting pumps to high shock loads may result in
excessive loading of the mounting flange.
Applications which experience extreme resonant vibrations or shock may require additional pump
support. The overhung load moment for multiple pump mounting may be estimated using the formula
below.
Technical Information
Series 90 Axial Piston Pumps
System Design Parameters
18
520L0603 • Rev 0804 • March 2016