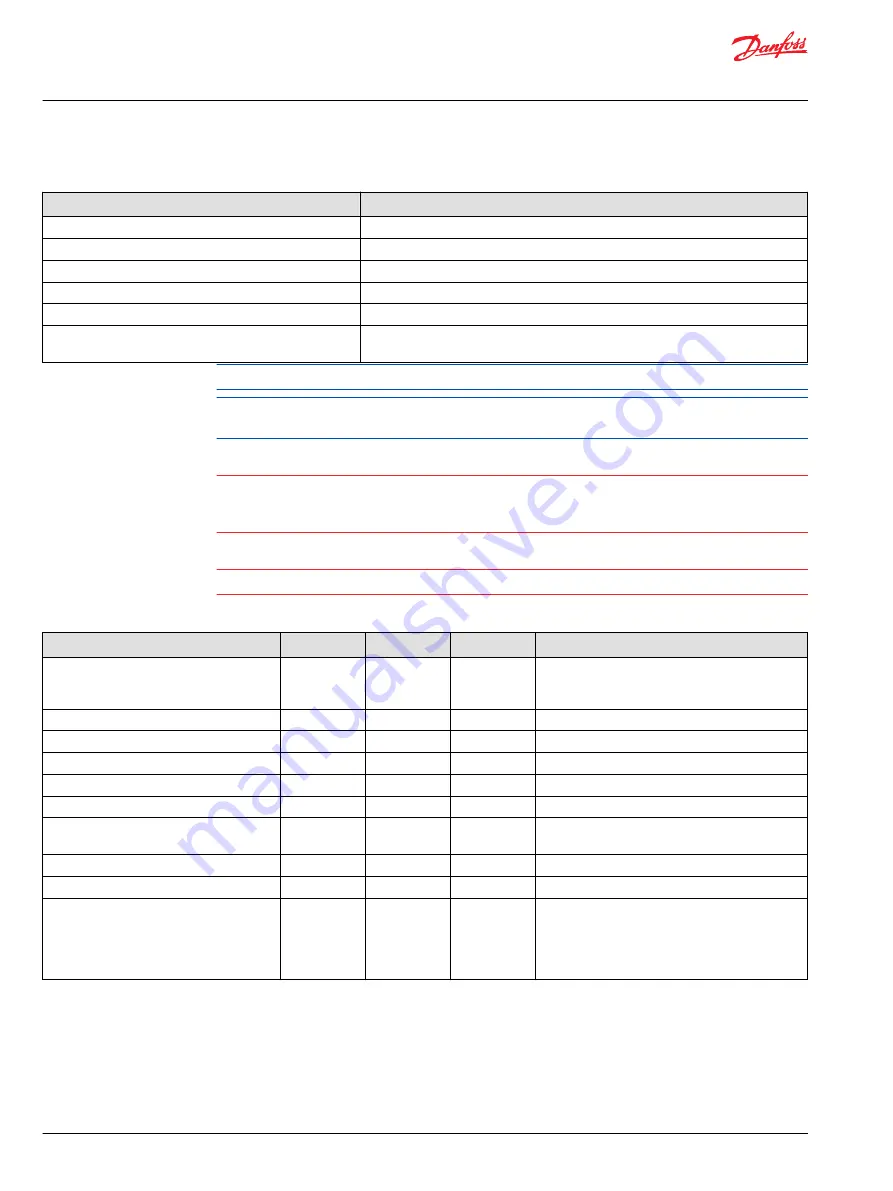
General
Description
Comment
Configuration
Sourcing or sinking.
Type (Linear vs. PWM)
PWM
Operating modes
Programmable: closed loop current or open loop voltage (duty cycle).
Dual coil PCPs
Compensated for induced currents in a non-driven coil (closed loop mode).
Short circuit to ground
Output fully protected against damage and fault detected.
Mode selection (current or voltage) and full scale current
ranges
Programmable.
Do not connect a digital output to (back drive) without a series diode.
PLUS+1
®
PWM output circuits are not designed to be used as inputs. Output current feedback readings
should be used for fault checking only.
W
Warning
Unintended movement of the machine or mechanism may cause injury to the technician or bystanders.
The module will be powered up if battery voltage is applied to the module's output pin. To protect
against unintended movement, secure the machine.
C
Caution
Warranty will be voided if module is damaged by significant current driven back through an output pin.
Specifications
Description
Units
Minimum
Maximum
Comment
Full scale proportional
current output
mA
10
3000
The current may accidently be exceeded in open
loop mode. If the current exceeds the trip point, the
output will be latched off.
Output voltage, 100% duty cycle
Vdc
0
Vbatt-1
Output resolution of 3 A
mA
0.25
Repeatability of full range
% of full scale
0.5
Absolute accuracy of full range
% of full scale
0.3
Output settling time
ms
100
Depends on load characteristics.
PWM frequency
Hz
33
4000 and
20,000
Dither frequency
Hz
40
250
Increased in steps, see module API.
Dither amplitude
A
0
0.5
Increased in steps, see module API.
Over-current trip point
A
5
7.3
There is over-current protection built into each
output driver. If the instantaneous current exceeds
the trip point, the driver is latched off. GUIDE
application software can reset the latch and attempt
to drive current again.
For each PWM output there are two switches in series for sourcing current/voltage (the high-side of the
half bridge has two switches). One switch is controlled and monitored by the secondary controller, and
the other is controlled and monitored by the primary processor. The secondary controller can monitor
the condition of the redundant switch under its control with a digital voltage feedback signal. Each
sourcing PWM output can be disconnected from its supply voltage at any time by the secondary
controller with this redundant switch. When the redundant switch is disabled it must remain disabled by
the kernel for 250 ms before the secondary controller's application is allowed to re-enable the redundant
switch. When the switch controlled by the secondary controller is enabled then the PWM outputs are
Technical Information
PLUS+1 SC0XX-1XX Controller Family
Outputs
14 |
©
Danfoss | June 2016
L1415500 | BC00000235en-US0201