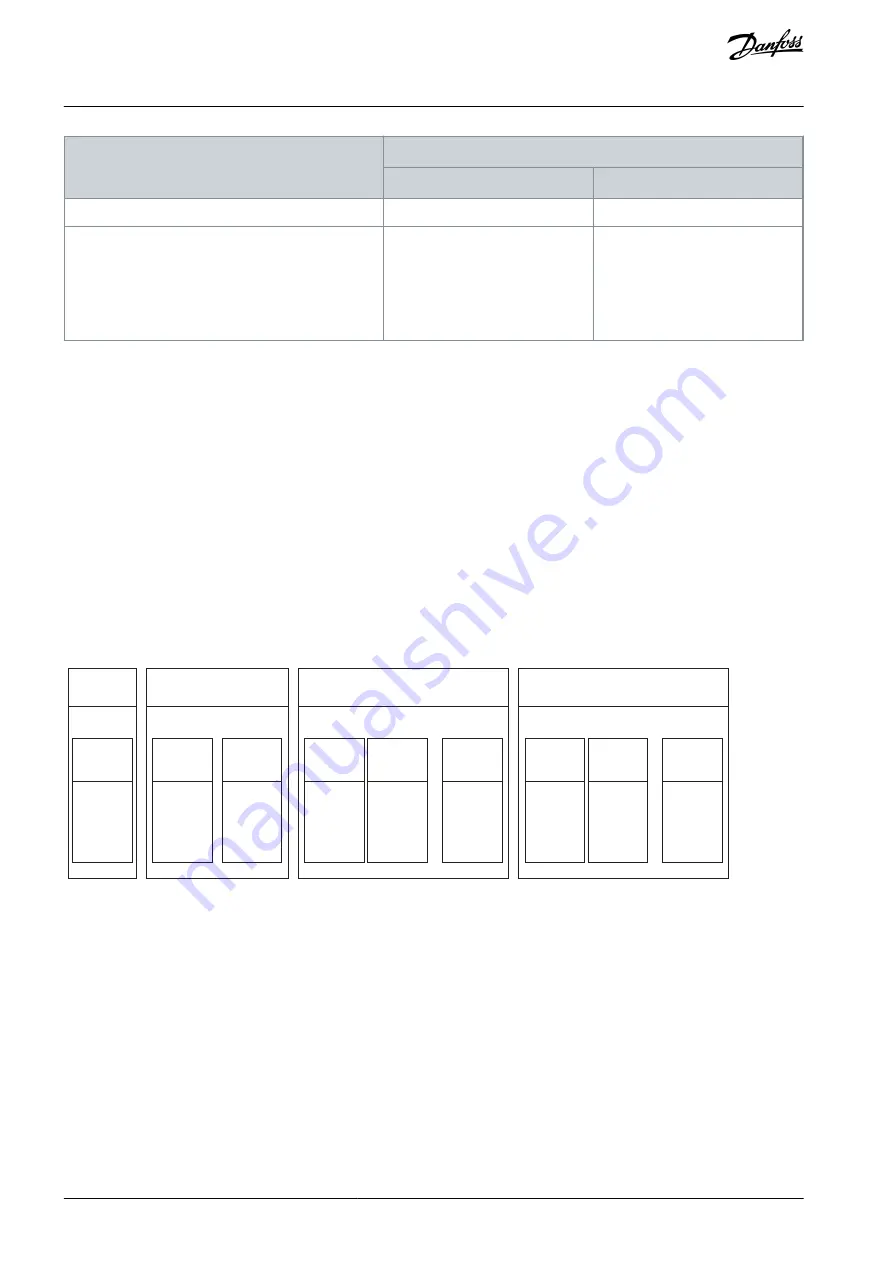
•
•
•
•
•
•
•
Application
Submodules
Cyclic input data
Cyclic output data
20 signals (80 bytes)
Motion
4 signals (16 bytes)
8 signals (32 bytes)
12 signals (48 bytes)
16 signals (64 bytes)
20 signals (80 bytes)
4 signals (16 bytes)
8 signals (32 bytes)
12 signals (48 bytes)
16 signals (64 bytes)
20 signals (80 bytes)
Each of the selections in a signal module can comprise the following data types:
Boolean
Unsigned 8/16/32
Signed 8/16/32
Float 32
The buffer size adapts to the data type of the selected signals. If a Boolean type is mapped, only bit 0 is used in the chosen signal
address, and the remaining 7 bits are not used.
The actual interpretation of the value that is read or written depends on the data type and representation. For example, motor
current is a real-type 32-bit value that is represented as float, and publishing the motor current as an actual value does not need any
scaling and factoring.
2.5.1 Functional Extension Options
Each functional extension option is defined by its own PROFINET device model with a module and submodule(s).
Slot 1 contains the application and the subsequent slots contain the installed options. Each option supports a module access point
(MAP), and other submodules contain the process data.
e3
0b
k7
55
.1
0
Subslot
0x0001
DAP
Slot 0
Device
Subslot
0x0001
MAP
Subslot
0x0002
iC Speed
profile
Slot 1
Application
Industry
General Purpose I/O OC7C0
Slot 3
Option
Subslot
0x0001
MAP
Subslot
0x0009
General
Purpose
I/O
DIN
T13
Subslot
0x0002
General
Purpose
I/O
AIN
T2
...
Basic I/O (+BDBA)
Slot 2
Option
Subslot
0x0001
MAP
Subslot
0x0012
Basic I/O
AIN
T34
Subslot
0x0002
Basic I/O
Relay
T2
...
Illustration 2: Example of a PROFINET Device Model with Functional Extension Options Installed in an iC7-Automation Frequency Converter
2.6 Network Topologies
Communication interface X1/X2 is used for fieldbus connection.
The iC7 series communication interface has 2 Ethernet ports (X1 and X2) and an embedded switch with 2 Ethernet RJ45 connectors.
It has 1 MAC and IP address, and is considered a single device in the network. The communication interface supports 3 network
topologies:
Line topology
Star topology
Ring topology
2.6.1 Line Topology
In many applications, line topology enables simpler cabling and the use of fewer Ethernet switches. Observe network performance
and the number of devices in a line topology. Too many devices in a line may exceed network update time limits.
AQ408626183394en-000101 / 136R0280
16 | Danfoss A/S © 2023.06
Product Overview
iC7 Series PROFINET
Operating Guide