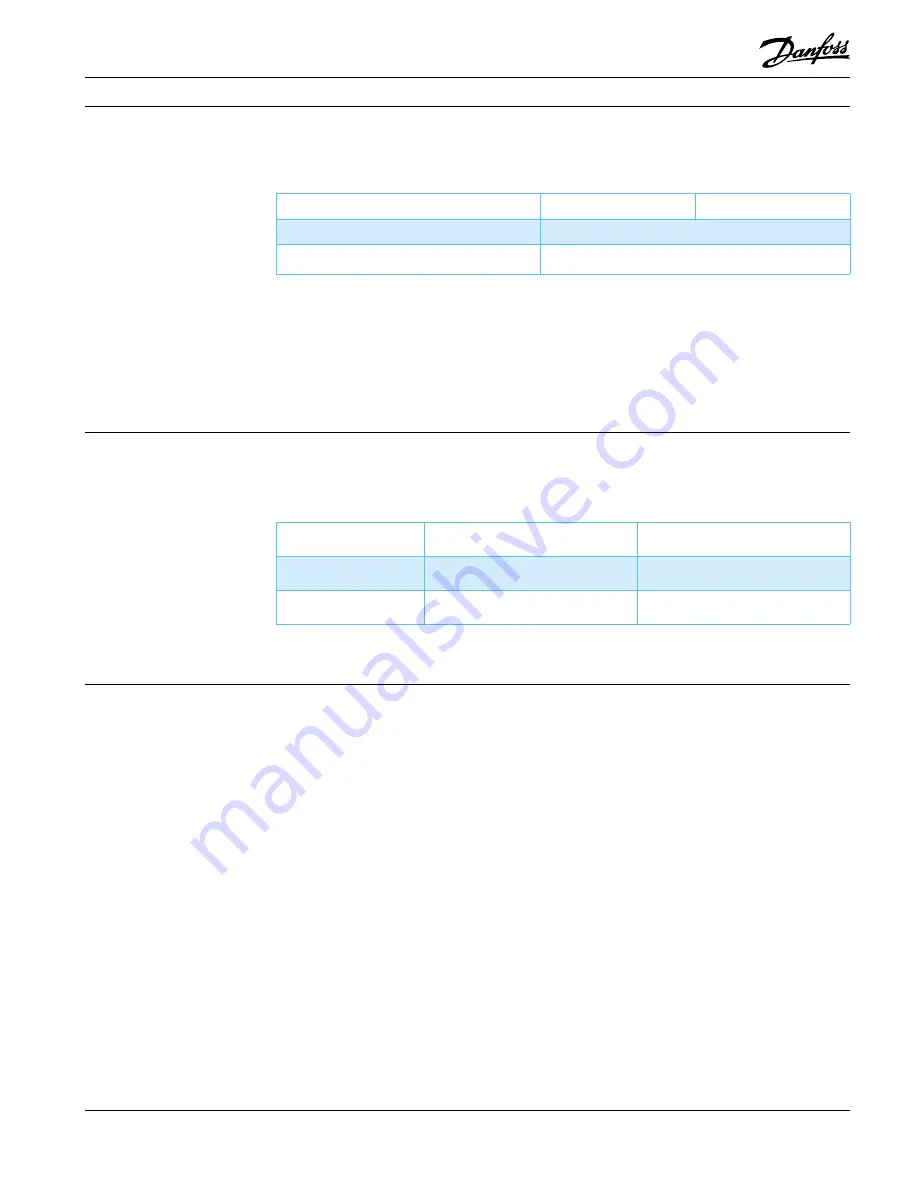
Installation
System pressure test
Pressurize the system on HP side first then LP
side to prevent rotation of the scroll. Never let
the pressure on LP side exceed the pressure on
HP side with more than 72 psi.
On SY/SZ240-300 models which have an
internal non return-valve in discharge fitting
or if an external non return valve is present on
the discharge line, we advise to pressurize the
system not quicker than 70 psi/s to allow enough
pressure equalisation between LP and HP side
over the scroll elements.
Always use an inert gas such as nitrogen for
pressure testing. Never use other gasses such as
oxygen, dry air or acetylene as these may form
an inflammable mixture. Do not exceed the
following pressures:
Moisture obstructs the proper functioning of the
compressor and the refrigeration system.
Air and moisture reduce service life and increase
condensing pressure, and cause excessively high
discharge temperatures, which can destroy the
lubricating properties of the oil. Air and moisture
also increase the risk of acid formation, giving
rise to copper platting. All these phenomena
can cause mechanical and electrical compressor
failure.
For these reasons it’s important to perform a
vacuum dehydration on the system to remove
all residual moisture from the pipe-work after
assembly;
SM / SY / SZ compressors are delivered with
< 100 ppm moisture level. The required moisture
level in the circuit after vacuum dehydration
must be < 100 ppm for systems with an SM / SY
/ SZ.
• Never use the compressor to evacuate the
system.
• Connect a vacuum pump to both the LP & HP
sides.
• Evacuate the system to a pressure of 0.02 inHg
(300 μm Hg) absolute.
Do not use a megohm meter nor apply power to
the compressor while it’s under vacuum as this
may cause internal damage.
Vacuum evacuation and
moisture removal
Leak detection must be carried out using a
mixture of nitrogen and refrigerant or nitrogen
and helium, as indicated in the table below.
Never use other gasses such as oxygen, dry air
or acetylene as these may form an inflammable
mixture.
Pressurize the system on HP side first then Low
side.
Leak detection
Maximum compressor test pressure (low side)
SM/SZ 084 - 185: 363 psig
SZ/SY240 - 380: 290 psig
Maximum compressor test pressure (high side)
464 psig
Maximum pressure difference between high and
low side of the compressor:
348 psig
Compressor model
Leak detection with refrigerant
Leak detection with a mass spectrometer
SM-SY compressors
Nitrogen & R22
Nitrogen & Helium
SZ compressors
Nitrogen & R134a or R407C
Nitrogen & Helium
Note 1:
Leak detection with refrigerant may be forbidden in some countries. Check local regulations.
Note 2:
The use of leak detecting additives is not recommended as they may affect the lubricant properties.
45
FRCC.PC.003.A5.22
Application guidelines