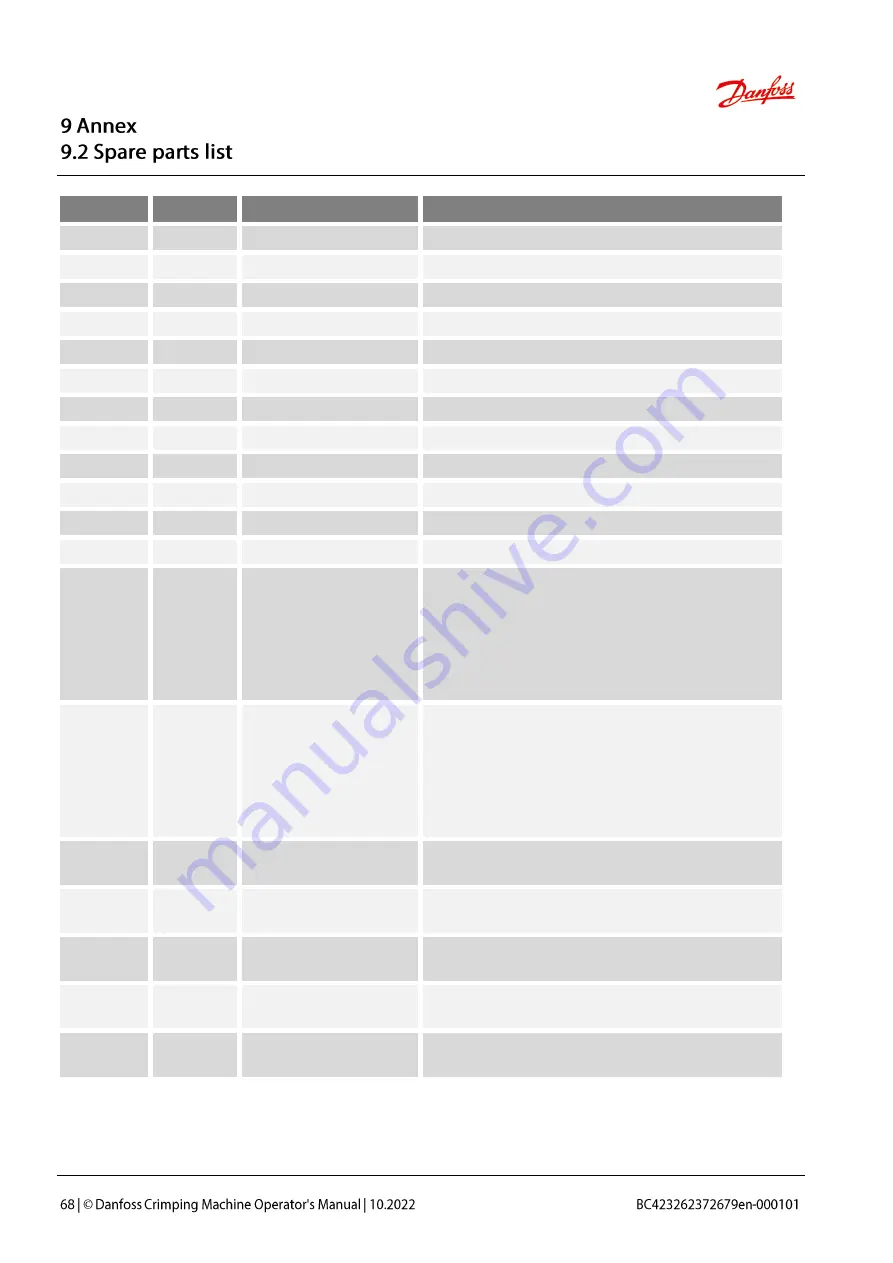
Item
Quantity
Part code
Designation
4
2
239.520
Double pipe nipple
5
2
239.529
Angle
6
1
239.535
Angle
7
1
268.337
Hydraulic double pump
8
1
268.325.3
Hydraulic block, complete
9
1
777.349
NG 10 valve
10
1
GN 552-R3/4"-A1
air ventilation caps
11
2
777.361
Gear pump flange
12
2
777.362
Gear pump flange
13
1
777.300
Bell housing
14
1
24/30N2a-28
Coupling
15
1
777.301.3
Gasket
16
1
235.326
777.3336
777.341
Pressure limiting valve for
hydraulic block 268.325.3_A / 268.325.3_D
Pressure limiting valve for
hydraulic block 268.325.3_B
Pressure limiting valve for
hydraulic block 268.325.3_C
17
1
777.325
777.338
777.340
Directional valve for
hydraulic block 268.325.3_A / 268.325.3_D
Directional valve for
hydraulic block 268.325.3_B
Directional valve for
hydraulic block 268.325.3_C
No pic-
ture
1
268.349.2
Tank seal
No pic-
ture
1
232.011
Electric motor 4 kW (S6/S8)
No pic-
ture
1
266.011
Electric motor 5.5 kW (S10)
No pic-
ture
1
238.139
Electric motor 5.5 kW 200 V 60 Hz 3 phases
No pic-
ture
1
266.019
Electric motor 5.5 kW 575 V 60 Hz 3 phases
Summary of Contents for ET4500-001
Page 1: ......
Page 3: ......
Page 69: ...Item Quantity Part code Designation 1 2 245 515 Piston pressure switch pressure setting 40 bar...
Page 74: ...Retaining bolt Crimping die profile 262 263 239 266 232 237 554 245 246 247 245 114 4 x x x...
Page 75: ...9 6 Hydraulic diagram...
Page 76: ...9 7 Electric diagram...
Page 77: ......
Page 78: ......
Page 81: ......
Page 82: ......
Page 83: ......
Page 84: ......