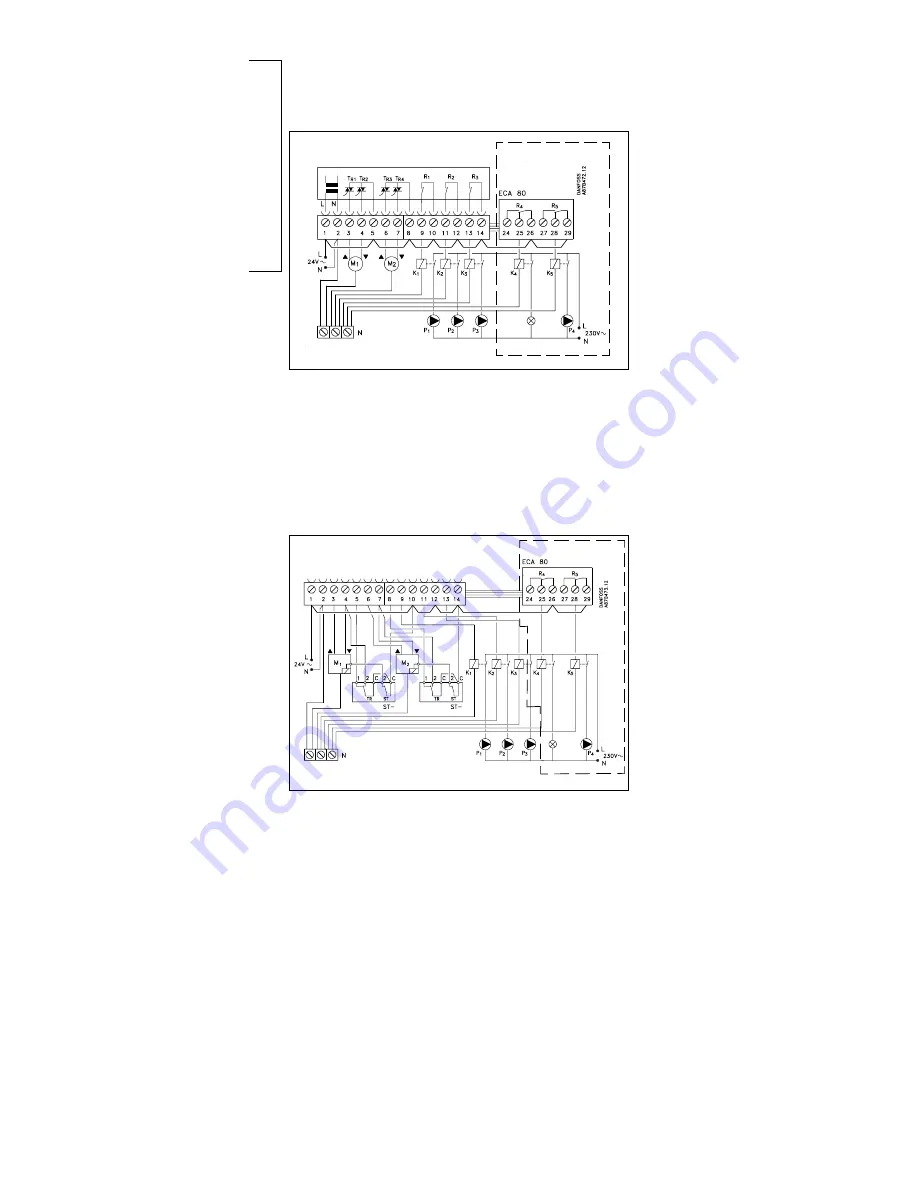
Installa
tion
13a
Electrical connections -
24 V a.c. - in general
24 V a.c. connections - without safety thermostat
Optional
Establish these jumpers:
1-5-8-10-12-14
and jumper 2 to common N-terminal.
If an ECA 80 module is to be applied, the jumpers 14-26-29
must be established additionally.
24 V a.c. connections - with safety thermostat
Optional
This circuit diagram is only valid if Danfoss actuators are used
Establish these jumpers:
1-10-12-14
Safety thermostat:
4, 5 and 10 with ST- (safety thermostat)
and jumper 2 to common N-terminal.
If an ECA 80 module is to be applied, the jumpers 14-26-29
must be established additionally.
Summary of Contents for ECL Comfort 100M
Page 4: ......
Page 13: ...Installation 11b ...
Page 21: ...Installation ...
Page 45: ...Control overviews ...
Page 71: ...The grey side of the ECL Card Extended service ...