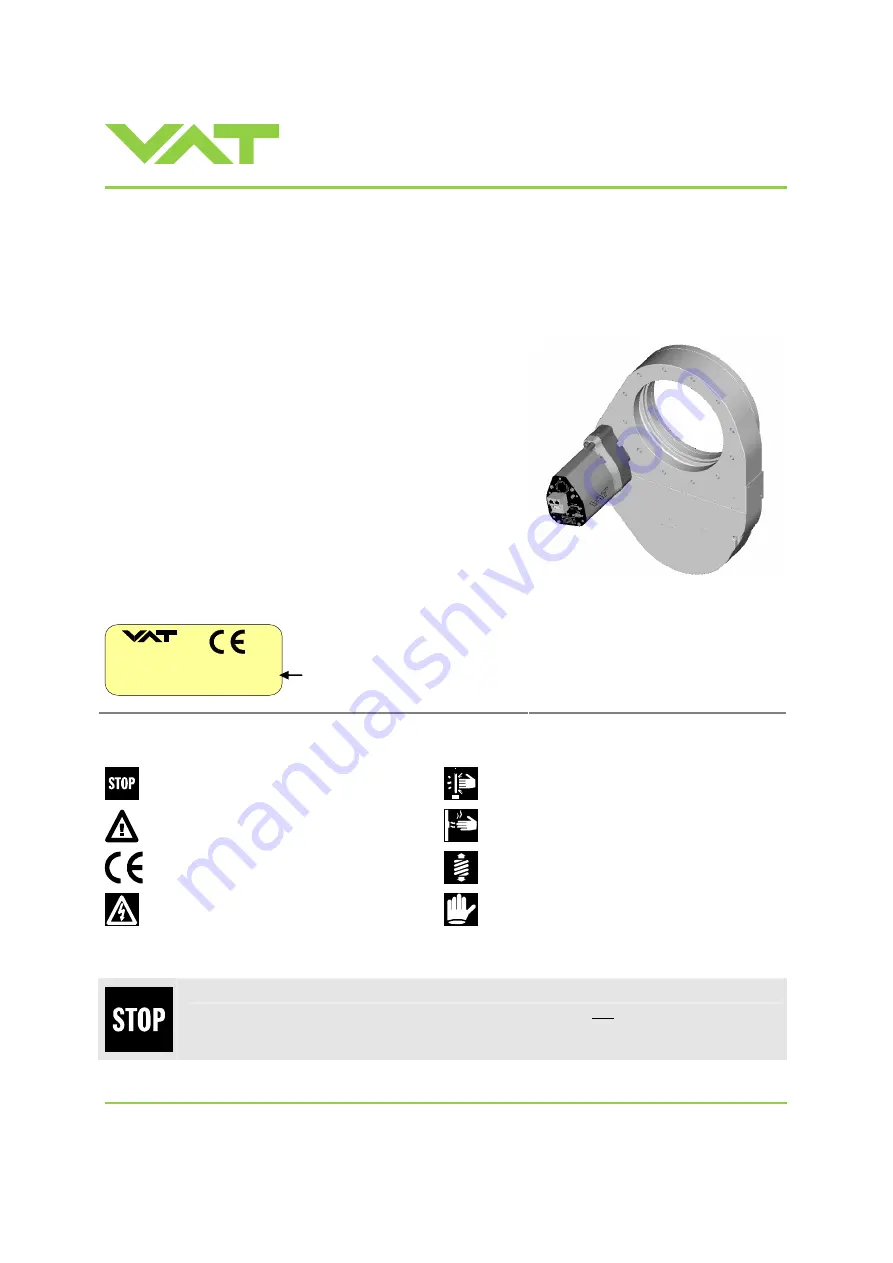
Installation, Operating & Maintenance Instructions
Series 650 DN 100-250 (I.D. 4“ - 10”), RS485
VAT Vakuumventile AG, CH-9469 Haag, Switzerland
Tel ++41 81 771 61 61 Fax ++41 81 771 48 30 Email
www.vatvalve.com
271149EA
2007-06-12
1/77
Pendulum control & isolation valve
with RS485 interface
with valve cluster functionality
This manual is valid for the valve ordering number(s):
650 . . - . . TJ - . . . .
(Master / 1 sensor input)
650 . . - . . TK - . . . .
(Master / 2 sensor inputs)
650 . . - . . VJ - . . . .
(Master / 1 sensor input /
±
15V SPS)
650 . . - . . VK - . . . .
(Master / 2 sensor inputs /
±
15V SPS)
650 . . - . . UJ - . . . .
(Master / 1 sensor input / PFO)
650 . . - . . UK - . . . .
(Master / 2 sensor inputs / PFO)
650 . . - . . WJ - . . . .
(Master / 1 sensor input /
±
15V SPS / PFO)
650 . . - . . WK - . . . .
(Master / 2 sensor inputs /
±
15V SPS / PFO)
650 . . - . . GS - . . . . (Slave)
650 . . - . . HS - . . . .
(Slave / PFO)
SPS = Sensor Power Supply
PFO = Power Failure Option
Master configured with firmware
650C.1E.06
Slave configured with firmware
650C.1E.06
The fabrication number is indicated on each product as per the label
below (or similar):
made in Switzerland
Fabrication No.:
patented
. .
650 . . – . . . . – . . . . / . . . .
A – . . . . . .
Fabrication number
sample picture
Explanation of symbols:
Read declaration carefully before you start any other
action!
Keep body parts and objects away from the valve
opening!
Attention!
Hot surfaces; do not touch!
Product is in conformity with EC guidelines!
Loaded springs and/or air cushions are potential
hazards!
Disconnect electrical power and compressed air
lines. Do not touch parts under voltage!
Wear gloves!
Read these «Installation, Operating & Maintenance Instructions» and the enclosed «General
Safety Instructions» carefully before you start any other action!