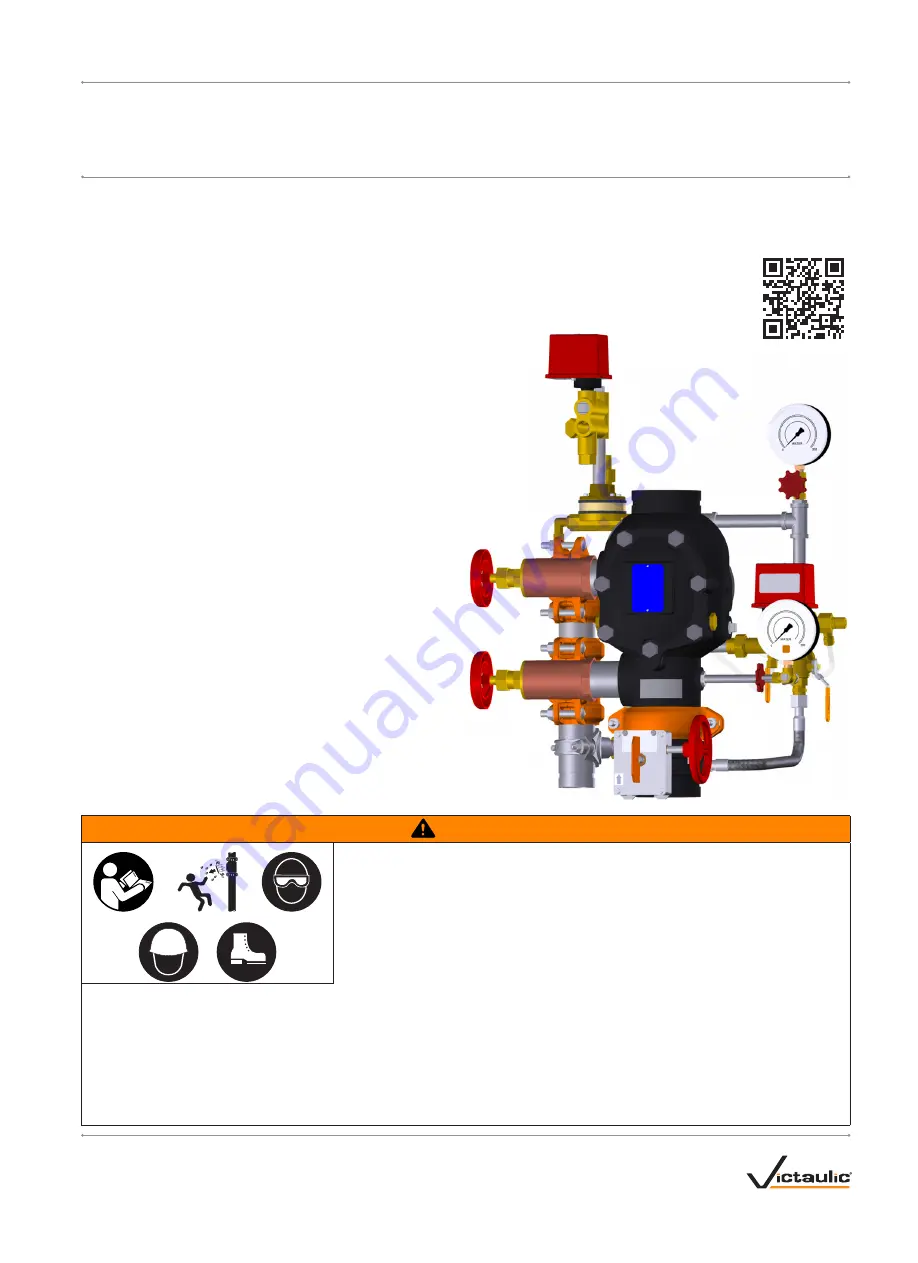
KEEP THESE INSTRUCTIONS WITH THE
INSTALLED VALVE FOR FUTURE REFERENCE
WARNING
• Read and understand all instructions before attempting to install any Victaulic products.
• Always verify that the piping system has been completely depressurized and drained
immediately prior to installation, removal, adjustment, or maintenance of any Victaulic
products.
• Wear safety glasses, hardhat, and foot protection.
Failure to follow these instructions could result in death or serious personal injury and property
damage.
• Series 769N FireLock NXT
™
Deluge Valves shall be used only in fire protection systems that are designed and installed in accordance with
current, applicable National Fire Protection Association (NFPA 13, 13D, 13R, etc.) standards, or equivalent standards, and in accordance
with applicable building and fire codes. These standards and codes contain important information regarding protection of systems from
freezing temperatures, corrosion, mechanical damage, etc.
• These installation instructions are intended for an experienced, trained installer. The installer shall understand the use of this product and
why it was specified for the particular application.
• The installer shall understand common industry safety standards and potential consequences of improper product installation.
Failure to follow installation requirements and local and national codes and standards could compromise system integrity or cause system
failure, resulting in death or serious personal injury and property damage.
Scan QR Code for Access to Videos
and Additional Publications
I-769N.Deluge
INSTALLATION, MAINTENANCE, AND TESTING MANUAL
Series 769N FireLock NXT
™
Deluge Valve
Pneumatic (Dry Pilot) Release, Hydraulic (Wet Pilot) Release, and Electric Release Systems
I-769N.Deluge
REV_F