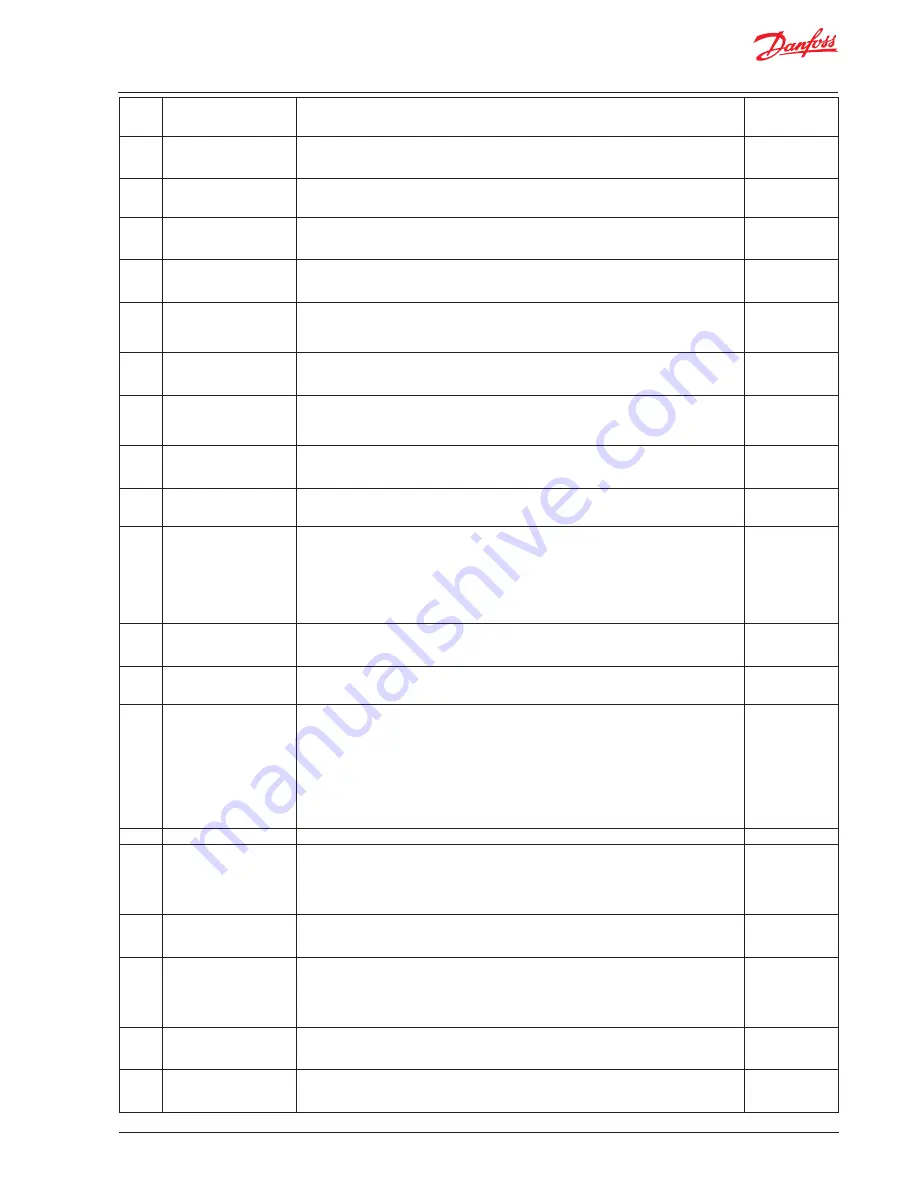
User Guide
|
Capacity Controller, AK-PC 651
RS8HA102 | 11
© Danfoss | ADAP-KOOL® | 2015.10
VSD Max speed
***: For speed
Highest permitted speed for compressor
Min: 40 Hz
Max: 120 Hz
Fac: 60 Hz
PWM period time
*, **: For “Scroll” and “Stream”
Set the period time for the unloading valve (on time + off time)
Min: 10 s
Max: 20 s
Fac: 20 s
CRII Period time
**: For CRII
Set the period time for the unloader valve (on time + off time)
Min: 10 s
Max: 20 s
Fab: 60 s
Comp. 1 min cap.
*: For scroll and CRII
Minimum capacity in the time period (without a minimum capacity the compressor
will not be cooled)
Min: 10%
Max: 50%
Fac: 10%
Comp. 1 start cap
*: For scroll and CRII
Start capacity: the compressor will only start when the capacity requirement reaches
the value
Min: 10%
Max: 60%
Fac: 30%
Comp. 1 Sd temp.
*, **: For “Scroll”, “Stream” and CRII
Define whether the controller should monitor the discharge gas temperature Sd from the
compressor (NTC 86K or Pt 1000 Ohm).
AI-demand
No / Yes
Fac: No
Comp. 1 Sd max.
*, **: For scroll, Stream and CRII and yes to “Comp.1 Sd temp”
Set the maximum Sd temperature
Min: 0°C
Max: 195°C
Fac: 125°C
No.of unloaders
****: For compressor with unloaders
Set how many unloaders there are on the compressor on multi-step compressors
DO-demand
Min: 1
Max: 3
Fac: 1
Comp. safety input
Compressor safety circuit
Define whether a DI input should be reserved for registration of each compressor safety
circuit
DI-demand
Yes /No
Fac: Yes
LP switch via DI
Low pressure safety circuit
Define whether a DI input should be reserved for registration of the signal from an LP switch
DI-demand
Yes /No
Fac: No
Load shedding via DI
Load limitation
Define whether a DI input should be reserved for registration of the signal from
a power meter
• None:
• DI: Load limitation must follow a DI input
• Night Mode: Load limitation must follow the status of the day/night signal.
(The day/night signal can be received via a DI input, via time schedule or network.)
DI-demand
Yes /No
Fac: No
Sd disch. gas temp.
Shared discharge temperature
Define whether signals from a common Sd sensor on the suction line (Pt 1000) should be
received
AI-demand
Yes /No
Fac: No
Ss suction superheat
Monitoring of superheat
Define whether a signal from a common Ss sensor on the suction line should be received
AI-demand
Yes /No
Fac: No
Injection ON fct.
Stop injection into evaporators
If the compressors are prevented from starting, stop injection into the evaporators.
Here define whether the function should be active and how the signal should be
communicated.
No: The function is not used
Network: The controller sends a signal to the system unit, which then forwards it to
the evaporator controls
Relay: The function reserves a relay that pulls in if all compressors are stopped.
All evaporator controls must be wired to this signal from the relay.
DO-demand
No /Network /Relay
Fac: No
Compressor timers
Compressor timers
Lead comp. Min ON
Min. On-time for first compressor
Set a forced On-time here during which the compressor will remain in operation before it
can be switched off again. The setting is to prevent incorrect operation.
To prevent a compressor breakdown, the setting must be made in accordance with the
requirements of the compressor supplier.
Min: 0 min
Max: 60 min
Fac: 0 min
Lead comp. Min OFF
Min. Off-time for first compressor
Set the forced Off-time during which the compressor must be off before it can be switched
on again. The setting is to prevent incorrect operation.
Min: 0 min.
Max: 30 min
Fac: 0 min
Lead comp. Restart
Min. period of time for re-starting the first compressor.
Set the forced Off-time during which the compressor must be off before it can be switched
on again. The setting is to prevent incorrect operation.
To prevent a compressor breakdown, the setting must be made in accordance with the
requirements of the compressor supplier.
Min: 1 min.
Max: 60 min
Fac: 4 min
Lead comp. Safety
delay
Delay time before compressor no. 1 cut out for reasons of safety
The time begins when a signal is received on the DI input (configure the DI input via
“Configuration” and “Comp. safety inlet”).
Min: 1 min.
Max: 10 min
Fac: 1 min
Comp. Min ON
Min. On-time for remaining compressors
Set a forced On-time here during which the compressor will remain in operation before it
can be switched off again. The setting is to prevent incorrect operation.
Min: 0 min.
Max: 60 min
Fac: 0 min