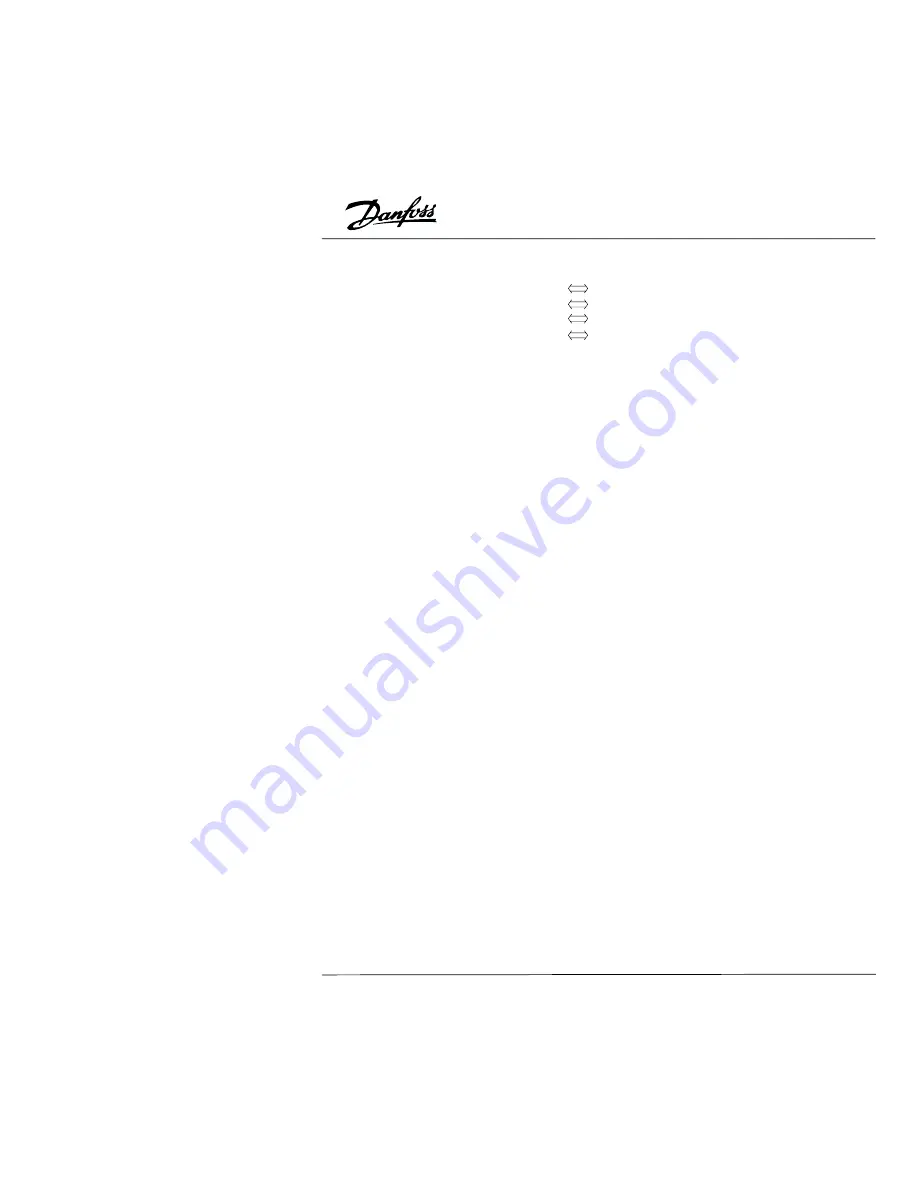
VLT
®
MICRO
3.3 ADR (1, 0)
00: Broadcast to all AC drives
ARD1 = 30Hex, ADR0 = 30Hex
01: To AC drive at Address 01
ARD1 = 30Hex, ADR0 = 31Hex
0F: to AC drive at Address 0F
ARD1 = 30Hex, ADR0 = 46Hex
10: To AC drive at Address 10
ARD1 = 31Hex, ARD0 = 30Hex
Maximum is 254, at Address FE
3.4 CMD (1, 0)
CMD0:
"0"
30Hex: Stop
"1"
31Hex: FWD + RUN
"2"
32Hex: REV + RUN
"3"
33Hex: JOG + FWD + RUN
"4"
34Hex: JOG + REV + RUN
"5"
35Hex: E.F. ON (External Fault)
"6"
36Hex: Reset
"7"
37Hex: Write Parameter
"8"
38Hex: Read Parameter
"9"
39Hex: Read Inverter Status
"A"
41Hex: Reserved
"B"
42Hex: Reserved
"C"
43Hex: Reserved
"D"
44Hex: Reserved
"E"
45Hex: Reserved
"F"
46Hex: Reserved
CMD1:
Bit 0 = 0
No Mirror Telegram
Bit 0 = 1
Mirror Telegram
Bit 2 = 1
When Bit 2 = 1, Means CEXX; clear with RESET command
86
Summary of Contents for 176F7300
Page 2: ...VLT MICRO ...