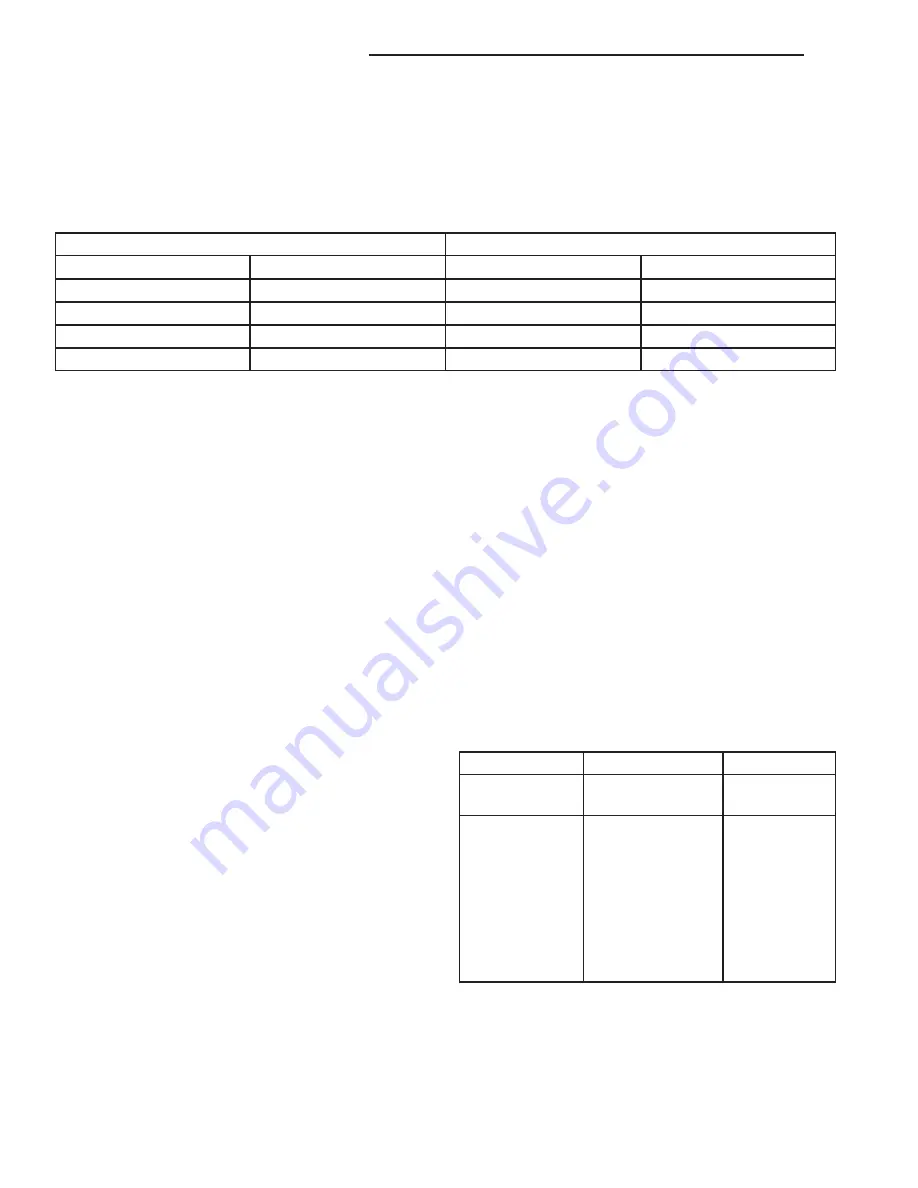
•
Mode control in the floor heat position
•
Blower motor control in the highest speed posi-
tion
Using a test thermometer, check the temperature
of the air being discharged at the floor outlets. Com-
pare the test thermometer reading to the Tempera-
ture Reference chart.
TEMPERATURE REFERENCE CHART
Ambient Temperature
Minimum Floor Outlet Temperature
Celsius
Fahreheit
Celsius
Fahreheit
15.5°
60°
62.2°
144°
21.1°
70°
63.8°
147°
26.6°
80°
65.5°
150°
32.2°
90°
67.2°
153°
If the floor outlet air temperature is insufficient,
check for a faulty heater valve (perform ATC Func-
tion Test) and verify that the cooling system is oper-
ating to specifications (Refer to 7 - COOLING/
ENGINE/COOLANT - DIAGNOSIS AND TESTING).
Both of the heater hoses should be HOT to the touch
(the coolant return heater hose should be slightly
cooler than the supply hose. If the coolant return
hose is much cooler than the supply hose, locate and
repair the engine coolant flow obstruction in the
heater system.
POSSIBLE LOCATIONS OR CAUSE OF
OBSTRUCTED COOLANT FLOW
•
Pinched or kinked heater hoses.
•
Improper heater hose routing.
•
Plugged heater hoses or supply and return ports
at the cooling system connections.
•
Inoperative or stuck heater water valve.
•
Plugged heater core.
If proper coolant flow is verified, and heater floor
outlet air temperature is insufficient, a mechanical
problem may exist.
POSSIBLE LOCATIONS OR CAUSE OF INSUFFI-
CIENT HEAT
•
An obstructed cowl air intake.
•
Obstructed heater system outlets.
•
Heater water valve not functioning properly.
TEMPERATURE CONTROL
If outlet air temperature cannot be adjusted with
the A/C-heater temperature control, one of the follow-
ing could require service:
•
Faulty A/C-heater control switch.
•
Faulty temperature sensor.
•
Faulty A/C-heater control cable or actuator.
•
Faulty A/C-heater control module.
ATC FUNCTION TEST
The automatic temperature control (ATC) system
can perform an self-test, which can be activated by
the DRBIII
t
scan tool to confirm that the A/C system
is performing satisfactorily. This test provides a
quick confirmation of heating and A/C system perfor-
mance to the service technician. Refer to Body Diag-
nostic Procedures for the appropriate diagnostic
information.
SPECIFICATIONS
HEATING - A / C SYSTEM
FRONT A/C SYSTEM
Item
Description
Notes
A/C Compres-
sor
Denso 7SBU16C
ND-8 PAG oil
Freeze-up Con-
trol
Evaporator tem-
perature sensor
HVAC hous-
ing mounted -
input to A/C-
heater control
- operating
range of -10°
C (14° F) to
40° C (104°
F)
24 - 6
HEATING & AIR CONDITIONING
VA