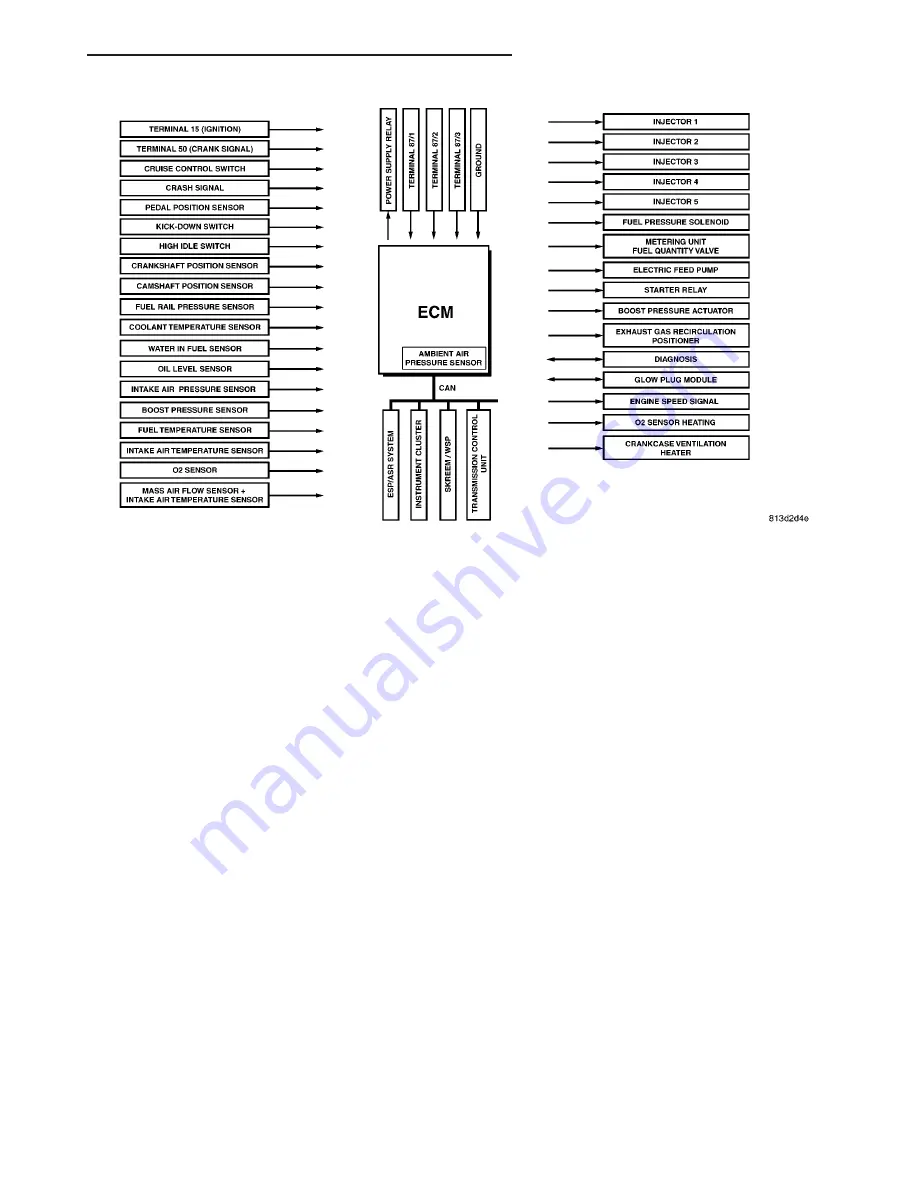
New software has been loaded to the ECM for EGR
control. This is due to the wider operating range and
larger volume of recirculated gas. There is a consid-
erable number of new, adapted, and optimized func-
tions, particularly with regard to injection, EGR,
boost control, sensing of the input parameters and
the signaling of the actuators (Fig. 3).
•
The rail pressure control achieved by signaling
the quantity control valve in the high pressure pump
and the pressure regulator results in reduced power
consumption of high pressure pump and in lowering
fuel pressures
•
Individual cylinder torque control for smooth
engine running: using the crankshaft position sensor
signals, the ECM detect non-uniform engine running
results from uneven torque contributions of the indi-
vidual cylinders and adjust the injection quantities of
the individual injectors so that all cylinders make the
same torque contribution
•
A relay is used for activating the electric in-tank
fuel pump
•
Heated crankcase ventilation to ensure pressure
compensation even at low temperatures
•
Improved boost pressure control using an elec-
tric variable nozzle turbine actuator with position
feed back
•
Controlled fuel heating using the high pressure
pump closed-loop control
•
Translation of the drive input received from the
accelerator pedal module which is equipped with
dual hall sensors
•
Measurement of the intake air mass using new
mass air flow (MAF) sensor with increase precision
and extended measuring range
•
O2 sensor for measuring the amount of oxygen
in the exhaust in order to calculate the air to fuel
ratio. With the intake air mass being known, the
injected fuel quantity can be calculated from the air
to fuel ratio
•
Activation of the O2 sensor heater to burn off
deposits
•
Full load EGR with a more precise, model based
EGR closed-loop control. The ECM calculates the
EGR rate from the various sensor signals. Using the
calculate EGR rate in percent instead of the fresh air
mass flow as a control parameter enables a more pre-
cise control of the EGR rate as well as better correc-
tion of the target value.
The oxygen sensor signal can be used in combina-
tion with the mass air flow signal, the injection
quantity signal and pressure and temperature sig-
nals to perform the following functions for optimized
closed loop control and monitoring of emissions
related components:
•
Injection valve quantity drift compensation in
partial load range: the oxygen content in the exhaust
is calculated from the air mass and from injection
quantity signal and is compared to the air-fuel ratio
as measured by the sensor. If the calculated air-fuel
ratio differs from the measured air-fuel ratio, the is
no correction of the injection quantity but the EGR
Fig. 3 ECM CONTROL
VA
ELECTRONIC CONTROL MODULES
8E - 5