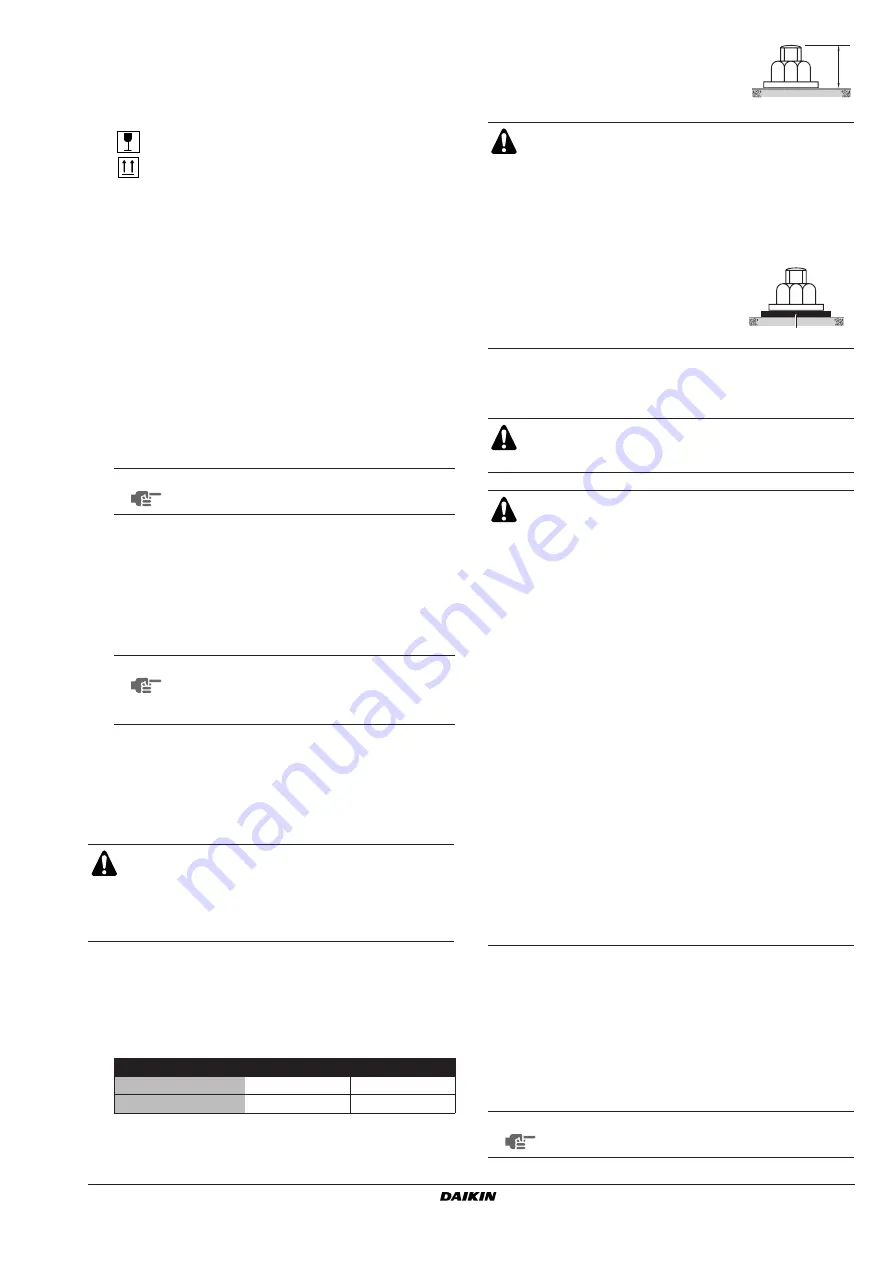
RXYQ8~18P7W1BR1
VRVIII System air conditioner
4PW44039-1E – 07.2010
Installation manual
4
4.
I
NSPECTING
AND
HANDLING
THE
UNIT
At delivery, the package should be checked and any damage should
be reported immediately to the carrier claims agent.
When handling the unit, take into account the following:
1
Fragile, handle the unit with care.
Keep the unit upright in order to avoid compressor
damage.
2
Choose on beforehand the path along which the unit is to be
brought in.
3
Bring the unit as close as possible to its final installation position
in its original package to prevent damage during transport.
4
Lift the unit preferably with a crane and 2 belts of at least 8 m
long.
Always use protectors to prevent belt damage and pay attention
to the position of the unit's centre of gravity.
5
If a forklift is to be used, preferably transport the unit with pallet
first, then pass the forklift arms through the large rectangular
openings on the bottom of the unit.
5.1
From the moment you use a forklift to move the unit to its final
position, lift the unit under the pallet.
5.2
Once at final position, unpack the unit and pass the forklift arms
through the large rectangular openings on the bottom of the unit.
5.
U
NPACKING
AND
PLACING
THE
UNIT
■
Remove the four screws fixing the unit to the pallet.
■
Make sure the unit is installed level on a sufficiently strong base
to prevent vibration and noise.
■
Make sure the base under the unit is larger than the 765 mm of
the unit depth.
■
The height of the foundation must at least be 150 mm from the
floor.
■
The unit must be installed on a solid longitudinal foundation
(steelbeam frame or concrete) as indicated in
■
Support the unit with a foundation of 67 mm wide or more. (The
support leg of the unit is 67 mm wide, see
■
Fasten the unit in place using four
foundation bolts M12. It is best to screw in
the foundation bolts until their length
remains 20
mm above the foundation
surface.
6.
R
EFRIGERANT
PIPING
6.1.
Installation tools
Make sure to use installation tools (gauge manifold charge hose, etc.)
that are exclusively used for R410A installations to withstand the
pressure and to prevent foreign materials (e.g. mineral oils such as
SUNISO and moisture) from mixing into the system.
(The screw specifications differ for R410A and R407C.)
Use a 2-stage vacuum pump with a non-return valve which can
evacuate to –100.7 kPa (5 Torr, –755 mm Hg).
1
Packaging material
2
Opening (large)
3
Belt sling
4
Opening (small) (40x45)
5
Protector
NOTE
Use a belt sling of
≤
20 mm wide that adequately
bears the weight of the unit.
NOTE
Use filler cloth on the forklift arms to prevent
damaging the unit. If the paint on the bottom
frame peels off, the anti corrosion effect may
decrease.
Do not use stands to only support the corners.
Model
A
B
RXYQ8~12
930
792
RXYQ14~18
1240
1102
X
Not allowed
O
Allowed (units: mm)
■
Prepare a water drainage channel around the
foundation to drain waste water from around the unit.
■
If the unit is to be installed on a roof, check the
strength of the roof and its drainage facilities first.
■
If the unit is to be installed on a frame, install the
waterproofing board within a distance of 150 mm
under the unit in order to prevent infiltration of water
coming from under the unit.
■
When installed in a corrosive
environment, use a nut with
plastic washer (1) to protect the
nut tightening part from rust.
Do not insert fingers, rods or other objects into the air
inlet or outlet. When the fan is rotating at high speed, it
will cause injury.
Use R410A to add refrigerant.
All field piping must be installed by a licensed refrigeration
technician and must comply with relevant local and
national regulations.
Caution to be taken when brazing refrigerant piping
Do not use flux when brazing copper-to-copper refrigerant
piping. (Particularly for the HFC refrigerant piping)
Therefore, use the phosphor copper brazing filler metal
(BCuP) which does not require flux.
Flux has extremely harmful influence on refrigerant piping
systems. For instance, if the chlorine based flux is used, it
will cause pipe corrosion or, in particular, if the flux
contains fluorine, it will damage the refrigerant oil.
Be sure to perform a nitrogen blow when brazing. Brazing
without performing nitrogen replacement or releasing
nitrogen into the piping will create large quantities of
oxidized film on the inside of the pipes, adversely affecting
valves and compressors in the refrigerating system and
preventing normal operation.
After completing the installation work, check that the
refrigerant gas does not leak.
Toxic gas may be produced if the refrigerant gas leaks into
the room and comes in contact with a source of fire.
Ventilate the area immediately in the event of a leak.
In the event of a leak, do not touch the leaked refrigerant
directly. Frostbite may be caused.
NOTE
Make sure the pump oil does not flow oppositely into
the system while the pump is not working.
20 mm
1