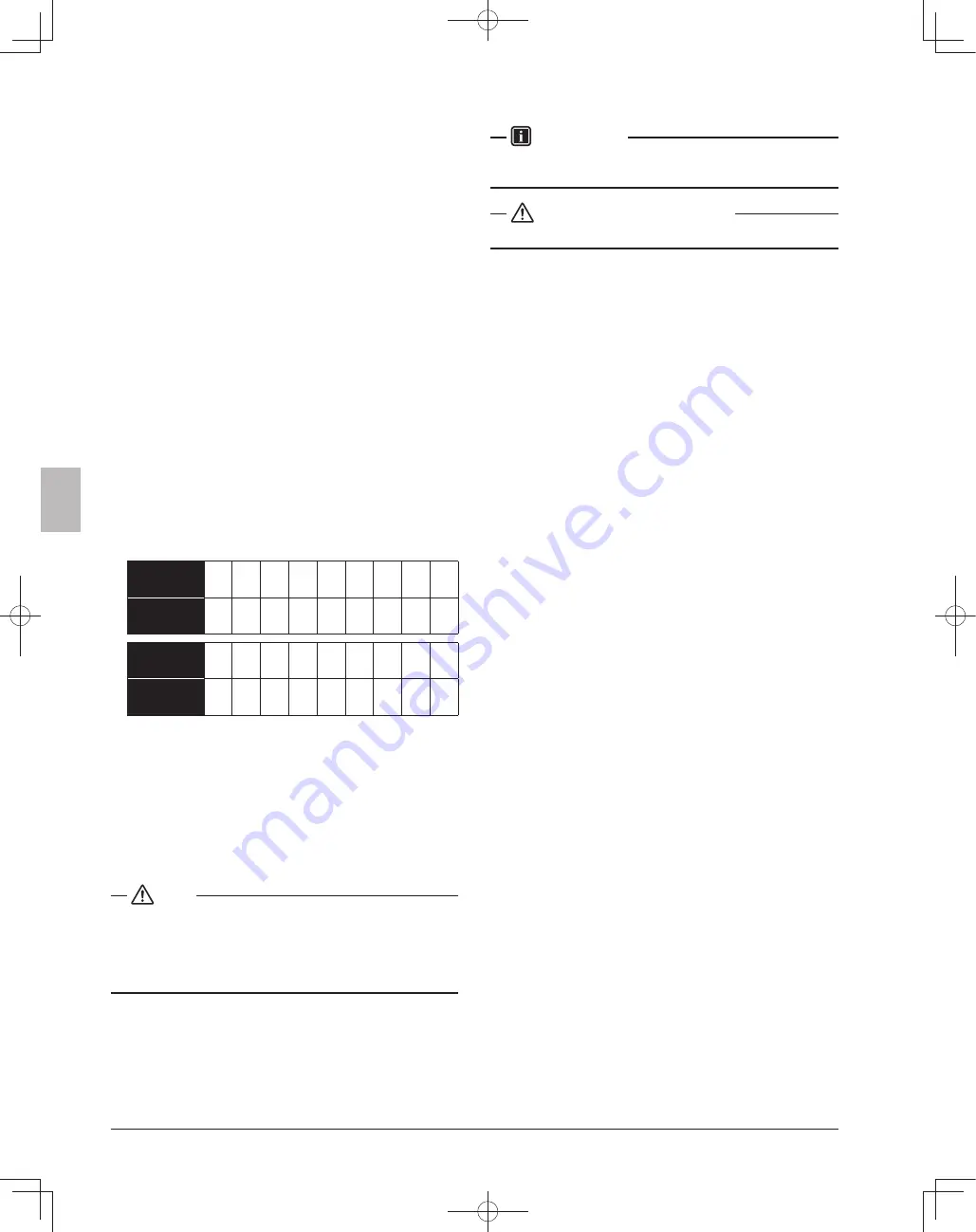
35
English
14.3.3. Final charge adjustment
It is not necessary to do this final adjustment normally, but perform the
following operation only when if the most adequate refrigerant for the
best performance is required.
The outdoor temperature must be between 60°F (16°C) and 97°F
(36 °C).
Run the system for 30 minutes in cooling by the forced operation using
the field setting mode [2-6] (value 0: OFF, 1:ON) (Refer to 15.2. Moni
-
toring function and field settings.) to allow pressures to stabilize, then
check subcooling as detailed in the following sections.
Subcooling = Condensing_temp.(TC) – (Heat exchanger liquid pipe)
Check subcooling for each outdoor unit by DAIKIN specified checker
and calculate the average subcooling of the outdoor unit using
weighted average method. (shown below)
To display the specific temperature in the unit, refer to the instructions
in the manual that comes with the kit.
Average subcooling = ((C1) x (S1) + (C2) x (S2) + (C3) x (S3) ) / (CT)
C1 = O-1 Capacity index (Outdoor Unit 1)
S1 = O-1 Subcooling (Outdoor Unit 1)
C2 = O-2 Capacity index (Outdoor Unit 2)
S2 = O-2 Subcooling (Outdoor Unit 2)
C3 = O-3 Capacity index (Outdoor Unit 3)
S3 = O-3 Subcooling (Outdoor Unit 3)
CT = Total Capacity index of Outdoor unit
Systems should have a subcooling of following table.
Capacity
index
72
96 120 144 168 192 216 240 264
Average
subcooling
6.0 4.5 6.2 6.7 7.9 5.3 6.1 6.5 6.5
Capacity
index
288 312 336 360 384 408 432 456 480
Average
subcooling
6.7 7.3 7.9 6.6 5.3 5.7 6.1 6.3 6.5
a. If average subcooling is low, add charge to raise subcooling to
(Average subcooling)±0.5°C. (The maximum additional charge
is 4.4 lbs. (2kg))
b. If average subcooling is high, remove charge to lower the sub-
cooling to (Average subcooling)±0.5°C.
14.3.4. Checks after adding refrigerant
• Are all stop valves open?
• Is the amount of refrigerant, that has been added, recorded on the
refrigerant charge label?
NOTE
• Make sure to open all stop valves after (pre-) charging the refrigerant.
Operating with the stop valves closed will damage the compressor.
• After adding the refrigerant, do not forget to close the cover of the
service port. The tightening torque for the cover is 7.9 to 10.8 ft
•
lbf
(10.7 to 14.7 N
•
m).
15.
Start-up and configuration
INFORMATION
It is important that all information in this chapter is read sequentially by
the installer and that the system is configured as applicable.
DANGER: ELECTRICAL SHOCK
See Safety considerations on page i.
15.1. Checks before initial start-up
After the installation of the unit, first check the following items. Once all
below checks are fulfilled, the unit must be closed, only then can the
unit be powered up.
1
Installation
Check that the unit is properly installed, to avoid abnormal noises
and vibrations when starting up the unit.
2
Field wiring
Be sure that the field wiring has been carried out according to the
instructions described in 9. Field wiring on page 21, according to
the wiring diagrams and according to the applicable legislation.
3
Power supply voltage
Check the power supply voltage on the local supply panel. The
voltage must correspond to the voltage on the identification label
of the unit.
4
Ground wiring
Be sure that the ground wires have been connected properly and
that the ground terminals are tightened.
5
Insulation test of the main power circuit
Using a megatester for 500 V, check that the insulation resistance
of 1 MΩ or more is attained by applying a voltage of 500 V DC
between power terminals and ground. Never use the megatester
for the transmission wiring.
6
Fuses, circuit breakers, or protection devices
Check that the fuses, circuit breakers, or the locally installed pro-
tection devices are of the size and type specified in 9. Field wiring
on page 21. Be sure that neither a fuse nor a protection device
has been bypassed.
7
Internal wiring
Visually check the control box and the inside of the unit on loose
connections or damaged electrical components.
8
Pipe size and pipe insulation
Be sure that correct pipe sizes are installed and that the insulation
work is properly executed.
9
Stop valves
Be sure that all stop valves are open.
10
Damaged equipment
Check inside of the unit on damaged components or squeezed pipes.
11
Refrigerant leak
Check inside of the unit on refrigerant leakage. If there is a refriger-
ant leak, try to repair the leak. If the repair is unsuccessful, call your
local dealer. Do not touch any refrigerant which has leaked out
from refrigerant piping connections. This may result in frostbite.
12
Oil leak
Check the compressor for oil leakage. If there is an oil leak, try
to repair the leak. If the repairing is unsuccessful, call your local
dealer.
13
Air inlet/outlet
Check that the air inlet and outlet of the unit is not obstructed by
paper sheets, cardboard, or any other material.
01_EN_Main_VRV6_HP_IM.indd 35
01_EN_Main_VRV6_HP_IM.indd 35
2022/12/08 17:56:17
2022/12/08 17:56:17