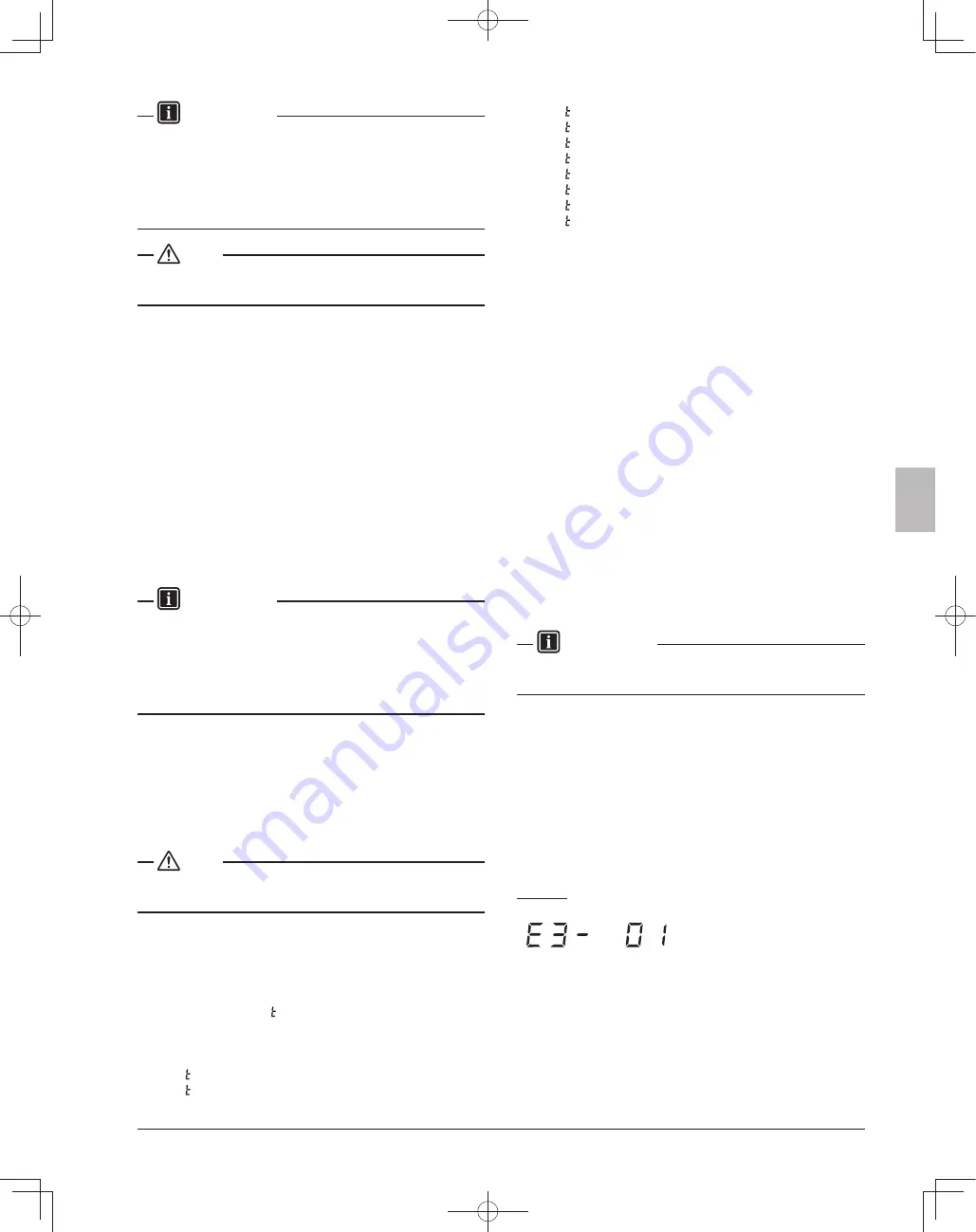
44
English
INFORMATION
Note that during the first running period of the unit (break in period for
compressor), required power input may be higher. This phenomenon
originates from the compressor that requires a 50 hour run elapse
before reaching smooth operation and stable power consumption.
Reason is that the scroll is made out of iron and that it takes some time
to smooth the surfaces that make contact.
NOTE
To protect the compressor, be sure to turn on the power supply 6
hours before starting operation.
15.4.2. Test operation
The procedure below describes the test operation of the complete
system. This operation checks and judges following items:
• Check of wrong wiring (communication check with indoor units).
• Check of the stop valves opening.
• Judgment of piping length.
On top of this system test operation, indoor units operation should
also be checked separately.
•
Make sure to carry out the system test operation after the first
installation. Otherwise, the error code U3 will be displayed on the
user interface and normal operation or indoor unit test run cannot
be carried out.
• Abnormalities on indoor units cannot be checked for each unit
separately. After the test operation is finished, check the in
-
door units one by one by performing a normal operation using
the user interface. Refer to the indoor units installation manual
for more details concerning the individual test run.
INFORMATION
• It may take 10 minutes to achieve a uniform refrigerant state before
the compressor starts.
• During the test operation, the refrigerant running sound or the mag-
netic sound of a solenoid valve may become loud and the display
indication may change.
These are not malfunctions.
Procedure
1
Close all front panels in order to not let it be the cause of misjudg-
ment.
2
Make sure all field settings you want are set; see 15.2. Monitoring
function and field settings on page 36.
3
Turn ON the power to the outdoor units and the connected indoor
units.
NOTE
Be sure to turn on the power 6 hours before operation in order to have
power running to the crankcase heater and to protect the compressor.
4
Make sure the default (idle) situation is existing; see 13.2. Operat-
ing the push buttons and DIP switches on the printed circuit board
on page 28. Push BS2 for 5 seconds or more. The unit will start
test operation.
• The test operation is automatically carried out, the outdoor unit
display will indicate
01
and the indication
Test operation
and
Under centralized control
will display on the user interface of
indoor units.
Steps during the automatic system test run procedure:
-
01
: control before start up (pressure equalization)
-
02
: cooling start up control
-
03
: cooling stable condition
-
04
: communication check
-
05
: stop valve check
-
06
: pipe length check
-
07
: refrigerant amount check
-
08
: −
-
09
: pump down operation
-
10
: unit stop
• During the test operation, the progress rate*
1
will be displayed
alternately with the display.
• During the test operation, it is not possible to stop the unit
operation from a user interface. To abort the operation, press
BS3. The unit will stop after ±30 seconds.
*1 The progress rate is displayed in
00P
-
99P
, but it may advance
rapidly.
5
Check the test operation results on the outdoor unit segment
display.
- Normal completion: no indication on the segment display
(idle).
- Abnormal completion: indication of error code on the seg-
ment display.
Refer to 15.4.3. Correcting after abnormal completion of the
test operation to take actions for correcting the abnormality.
When the test operation is fully completed, normal operation
will be possible after 5 minutes.
15.4.3. Correcting after abnormal completion of the test
operation
The test operation is only completed if there is no error code displayed
on the user interface or outdoor unit segment display. In case an error
code is displayed, perform correcting actions as explained in the error
code table. Carry out the test operation again and confirm that the
abnormality is properly corrected.
INFORMATION
Refer to the installation manual of the indoor unit for other detailed
error codes related to indoor units.
15.5. Error code list
In case of a displayed error code, perform correcting actions as ex-
plained in the error code table.
After correcting the abnormality, press BS3 to reset the error code and
retry operation.
The error code which is displayed on the outdoor unit will indicate a
main error code and a sub code. The sub code indicates more detailed
information about the error code. The error code will be displayed
intermittent.
Example:
Main code
Sub code
With an interval of 1 second, the display will switch between main
code and sub code.
01_EN_Main_VRV6_HP_IM.indd 44
01_EN_Main_VRV6_HP_IM.indd 44
2022/11/17 16:07:42
2022/11/17 16:07:42