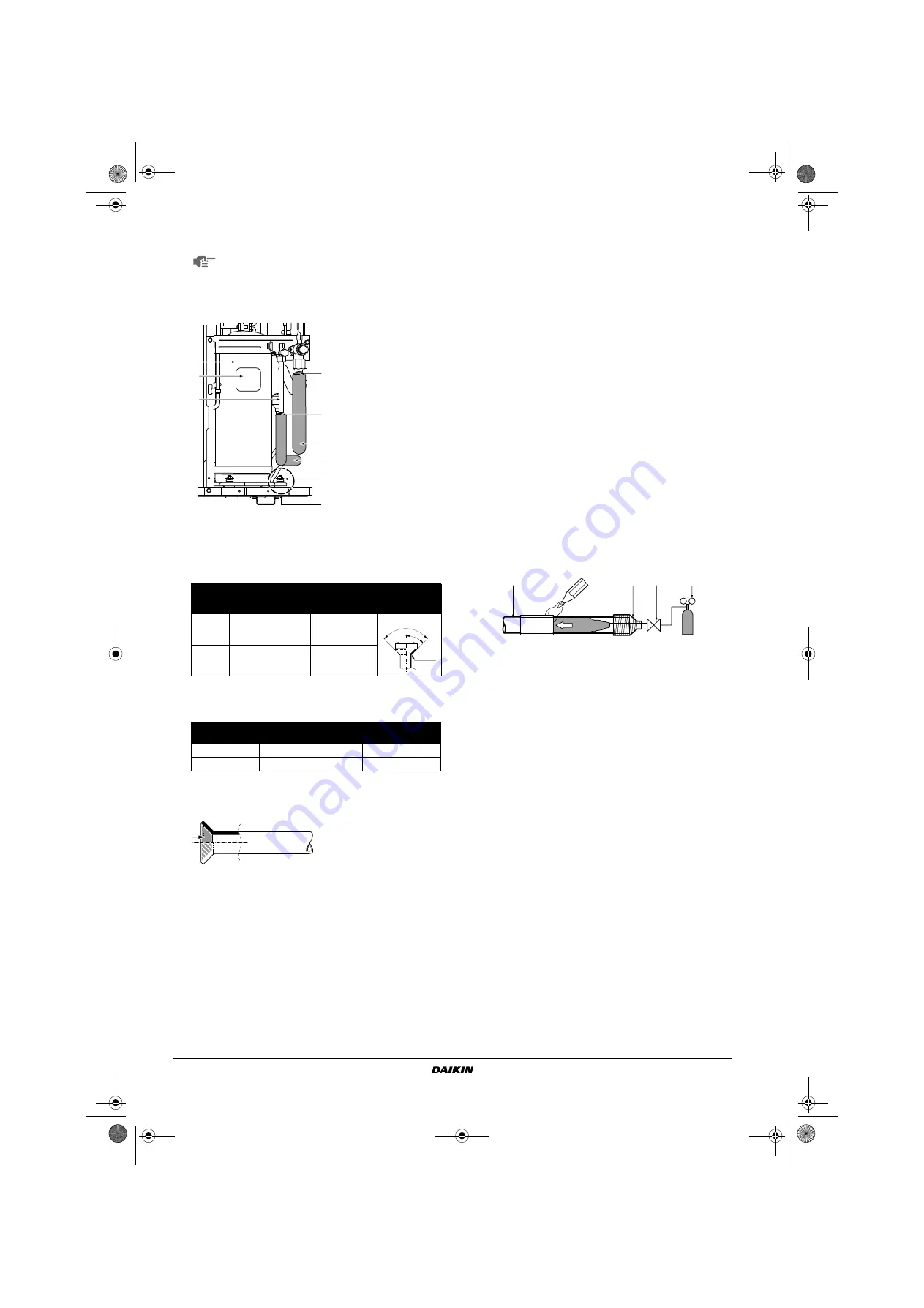
Installation manual
8
Be sure to insulate the liquid and gas-side field piping and the
refrigerant branch kit.
(The highest temperature that the gas-side piping can reach is
around 120°C, so be sure to use insulating material which is
very resistant.)
Cautions for flare connection
Please refer to the table for the dimensions for processing flares
and for the tightening torques. (Too much tightening will end up
in splitting of the flare.)
If a torque wrench is not available, be aware that the tightening
torque may increase suddenly. Do not tighten nuts any further
than to the angle as listed.
When connecting the flare nut, coat the flare inner surface with
ether oil or ester oil and initially tighten 3 or 4 turns by hand
before tightening firmly.
After completing the installation, carry out a gas leak inspection
of the piping connections with nitrogen and such.
Cautions for necessity of a trap
Since there is fear of the oil held inside the riser piping flowing back into
the compressor when stopped and causing liquid compression
phenomenon, or cases of deterioration of oil return, it will be necessary
to provide a trap at an appropriate place in the riser gas piping.
Trap installation spacing.
(See figure 6)
A
Outdoor unit
B
Indoor unit
C
Gas piping
D
Liquid piping
E
Oiltrap
H
Install trap at each difference in height of 10 m.
A trap is not necessary when the outdoor unit is installed in a
higher position than the indoor unit.
Cautions for brazing
Be sure to carry out a nitrogen blow when brazing.
Brazing without carrying out nitrogen replacement or releasing
nitrogen into the piping will create large quantities of oxidised
film on the inside of the pipes, adversely affecting valves and
compressors in the refrigerating system and preventing normal
operation. When brazing pipes however, do not use oxidation
preventers. Residue of such preventers may result in choking of
pipes or malfunction of components.
When brazing while inserting nitrogen into the piping, nitrogen
must be set to 0.02 MPa with a pressure-reducing valve (=just
enough so that it can be felt on the skin).
Evacuating
Do not purge the air with refrigerants. Use a vacuum pump to
vacuum the installation. No additional refrigerant is provided for
air purging.
Pipes inside the units were checked for leaks by the
manufacturer. The refrigerant pipes fit on site are to be checked
for leaks by the installer.
Confirm that the valves are firmly closed before leak test or
vacuuming.
Set up for vacuuming and leak test:
see
figure 8
Any exposed piping may cause condensation or burns
if touched.
Piping
size
Flare nut
tightening torque
A - dimensions for
processing flares
(mm)
Flare shape
Ø9.5
33~39 N•m
12.8~13.2
Ø15.9
63~75 N•m
19.3~19.7
Piping size
Further tightening angle
Recommended arm
length of tool
Ø9.5
60°~90°
200 mm
Ø15.9
30°~60°
300 mm
2
1
3
5
5
A
4
4
6
1
Compressor
2
Terminal cover
3
Indoor and outdoor
field piping
4
Corking, etc.
5
Insulation material
6
Bolts
A
Be careful with pipe,
bolt and outer panel
connections
R=0.4~0.8
45
° ±
2
90
°±
2
A
1
Refrigerant piping
2
Part to be brazed
3
Taping
4
Hands valve
5
Pressure-reducing valve
6
Nitrogen
A
Pair system
B
Simultaneous operation system
1
Pressure gauge
2
Nitrogen
3
Refrigerant
4
Weighing machine
5
Vacuum pump
6
Stop valve
7
Main pipe
8
Branched pipes
9
Pipe branching kit (optional)
1
2
3
4
5
6
6
4PEN342104-1B.book Page 8 Tuesday, May 26, 2015 9:07 AM