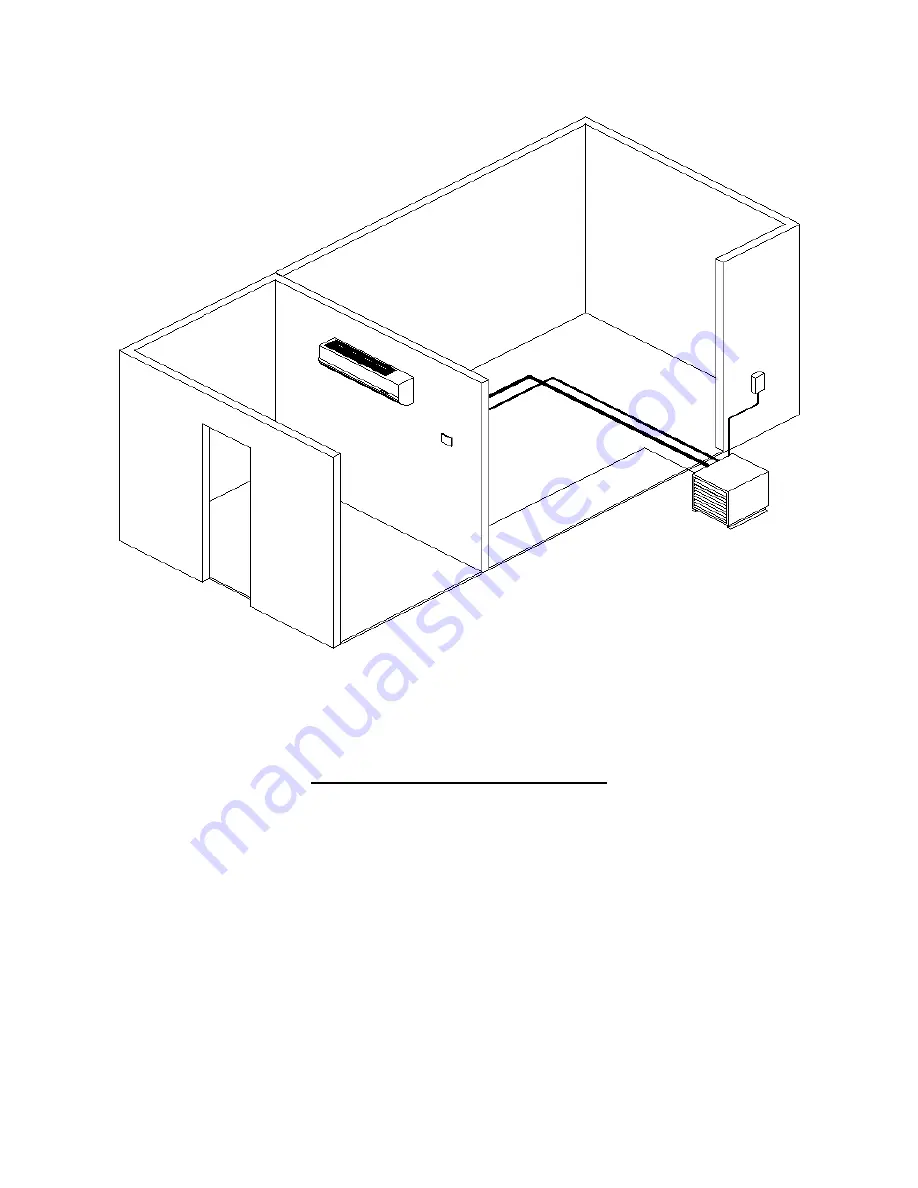
WZDS9100 #2
1
Wine Zone Ductless Split System
Requires an HVAC technician to install and charge unit
Can be charged with R-22, NU-22B, MO99, or R-427A refrigerants
Electric connections for evaporator are hard wired to the condenser
Industrial grade for longer life
Indoor and outdoor condensing units available
Field supplied drain line, refrigerant, and electric connections required