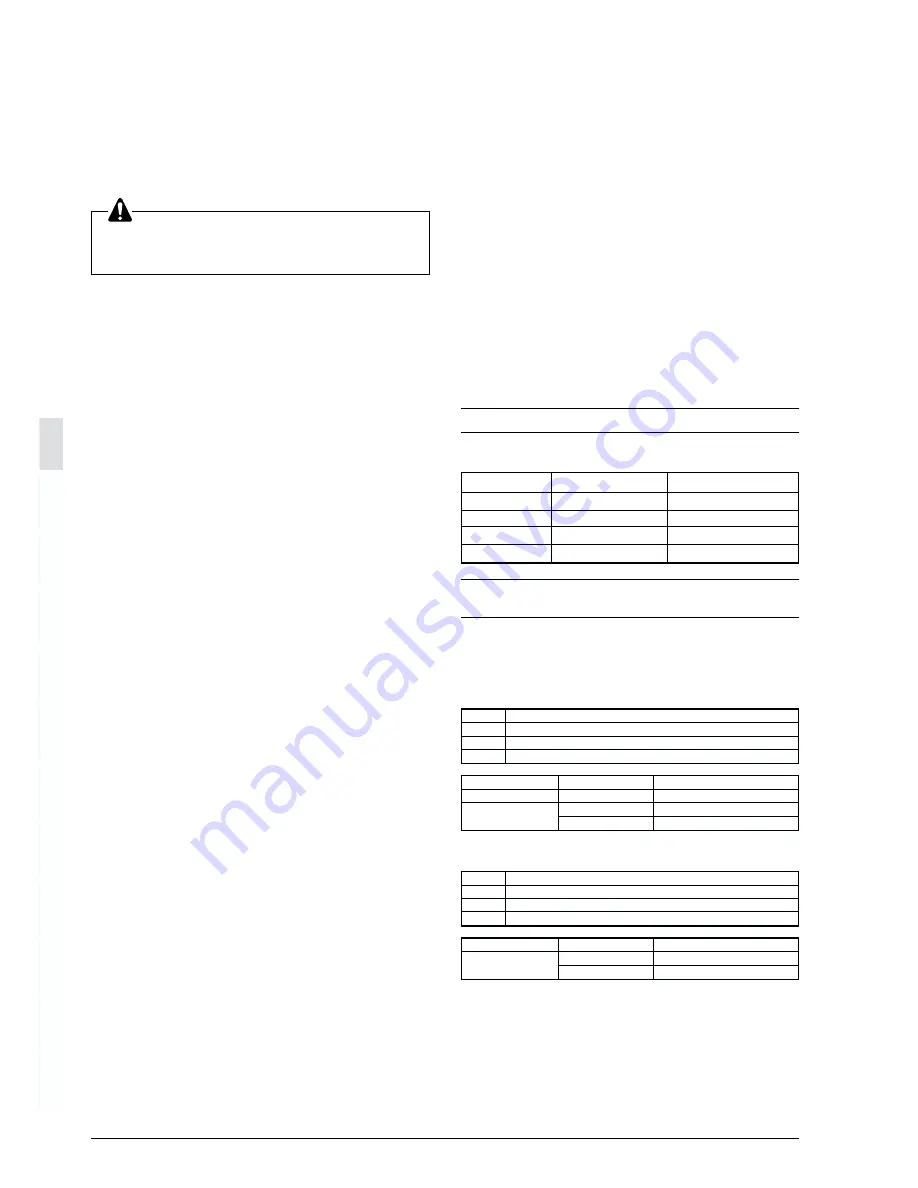
5
E
VACUATING
The units were checked for leaks by the manufacturer.
The refrigerant lines fitted in site are to be checked for leaks by
the fitter.
Confirm that the valves are firmly closed before pressure test or
vacuuming.
Do not purge the air with refrigerants. Use a vacuum
pump to vacuum the installation. No additional refrigerant
is provided for air purging.
Air tight test and vacuum drying (take special care for
R407C units): refer to figure 11
A Pair system
B Simultaneous operation system
1 Pressure gauge
2 Nitrogen
3 Refrigerant
4 Weighing machine
5 Vacuum pump
6 Stop valve
7 Main pipe
8 Branched pipes
9 Pipe branching kit (optional)
•
Air tight test: make sure to use nitrogen gas. Pressurize the
liquid and gas pipes to 3.3MPa (do not pressurize more than
3.3MPa). If the pressure drops, check where the nitrogen
comes from.
•
Vacuum drying: use a vacuum pump which can evacuate to
-100.7kPa (5Torr, -755mmHg).
1. Evacuate the system from the liquid and gas pipes by
using a vacuum pump for more than 2 hours and bring the
system to -100.7kPa. After keeping the system under that
condition for more than one hour, check if the vacuum
gauge rises or not. If it rises, the system may either contain
moisture inside or have leaks.
2. Following should be executed if there is a possibility of
moisture remaining in the pipe (if piping work is carried out
during the raining season or over a long period of time,
rainwater may enter the pipe during work).
After evacuating the system for 2 hours, pressurize the
system to 0.05MPa (vacuum break) with nitrogen gas and
evacuate the system again using the vacuum pump for
1 hour to -100.7kPa (vacuum drying). If the system cannot
be evacuated to -100.7kPa within 2 hours, repeat the
operation of vacuum break and vacuum drying.
Then after leaving the system in vacuum for 1 hour,
confirm that the vacuum gauge does not rise.
Leak test
1. Evacuate the pipes and check vacuum. (No pressure increase
for 1 minute.)
2. Break the vacuum with a minimum of 2 bar of nitrogen.
3. Conduct leak test by applying soap water, etc. to the connect-
ing part of the pipes.
4. Discharge Nitrogen.
5. Evacuate and check vacuum again.
6. Open the stop valve and inject the refrigerant into the refrig-
erant pipe and into the indoor unit.
7. Leak test must satisfy EN 378-2.
C
HARGING
REFRIGERANT
This unit requires additional charging of refrigerant according to
the length of pipe connected at the site. Concerning R407C
refrigerant: charge the refrigerant to the liquid pipe in its liquid
state. Since R407C is a mixed refrigerant, its composition
changes if charged in a state of gas and normal system operation
would no longer be assured.
Concerning L1~L7 (see tables below), refer to figures 2~5.
1. Additional charging of refrigerant
•
The R22 cooling units (R200/R250) do not require any
additional charging of refrigerant.
•
The R22 heatpump units (RY200/RY250) and the R407C
units (R(Y)P200 / R(Y)P250) require additional charging of
refrigerant, according to the length of pipe connected at the
site.
Find the correct amount of additional refrigerant to charge ‘G’
(kg) using one of the following formulas.
If G<0: no addition is required.
Pair system: refer to figure 2
L1 (m)
one way length of liquid pipe
Simultaneous operation system
(Twin, Triple, Double Twin: refer to figures 2~5)
- L1 (m)
one way length of main liquid pipe
- L2~L7 (m) one way length of branched liquid pipes
R407C:
R407C
R22
R(P)200
G = (L1-30) x 0.06
G= 0
R(P)250
G = (L1-30) x 0.09
G= 0
RY(P)200
G = (L1-30) x 0.10
G= (L1-7.5) x 0.03
RY(P)250
G = (L1-30) x 0.14
G= (L1-7.5) x 0.05
RP200
G = (L1-30) x 0.06 + L2 x A + L3 x A + L4 x A + L5 x A + L6 x A + L7 x A
RP250
G = (L1-30) x 0.09 + L2 x A + L3 x A + L4 x A + L5 x A + L6 x A + L7 x A
RYP200 G = (L1-30) x 0.10 + L2 x A + L3 x A + L4 x A + L5 x A + L6 x A + L7 x A
RYP250 G = (L1-30) x 0.14 + L2 x A + L3 x A + L4 x A + L5 x A + L6 x A + L7 x A
Branched pipe
A
RP200,250
Ø 9.5
0.03 kg/m
RYP200,250
Ø 6.4
0.03 kg/m
Ø 9.5
0.05 kg/m
R22:
R200
G = 0
R250
G = 0
RY200
G = (L1-7.5) x 0.03 + L2 x A + L3 x A + L4 x A + L5 x A + L6 x A + L7 x A
RY250
G = (L1-7.5) x 0.05 + L2 x A + L3 x A + L4 x A + L5 x A + L6 x A + L7 x A
Branched pipe
A
RY200,250
Ø 6.4
0.005 kg/m
Ø 9.5
0.015 kg/m