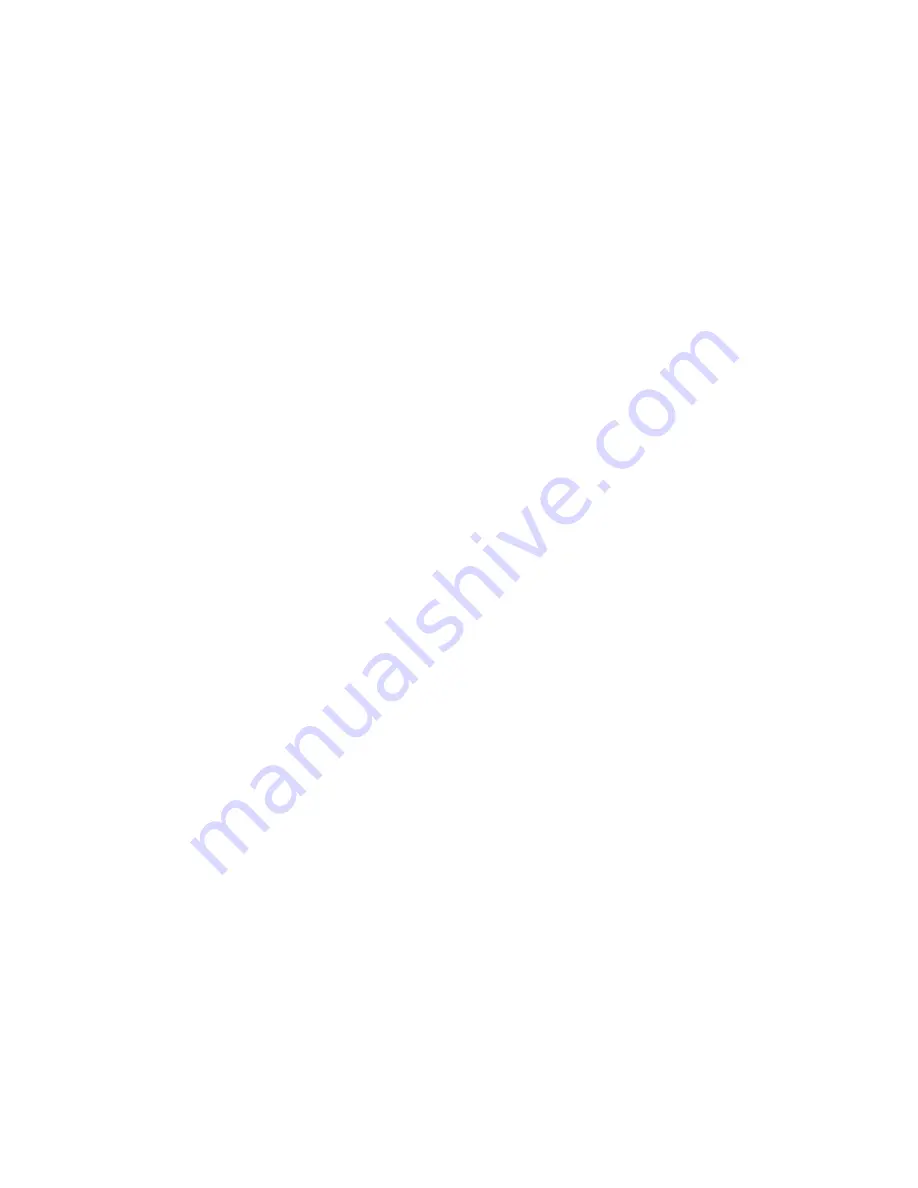
Page 24 of 48
IM 934-5
Operation
Memory Recall
The digital control shall start with the last settings used prior
to power down. These settings are saved in a non-volatile
memory. Factory set mode is OFF.
On/Off Triggering
Control can be turned On/Off via LUI, Remote T’stat, or
Sleep feature. The control will show the temperature set
point when the mode is Cool, Cool Dry, or Heat. The display
will be blank in Fan mode.
1.
On/Off triggering with LUI
Control shall turn On or Off when the On/Off button is
pressed in LUI. Once turned on control shall start on the
last mode used before it was turned Off.
2.
On/Off triggering with the Remote T’stat
Control shall be turned On if it was Off from the Remote
T’stat when it is set up to be controlled by a Remote
T’stat. A call for heat or cool from the Remote T’stat will
be used to turn the control on. Control remains on until
manually turned Off.
3.
On/Off triggering with the Sleep feature
Sleep feature works in combination with the Timer
setting. Sleep time setting shall be user adjustable from
1 to 15 hours via the Touchpad. The timer will count
down and when it reaches “0” it will turn the control Off
if control was previously On and vice versa, if it was
Off it will turn On after time expires. As mentioned in
protections
section of this spec the Sleep operation is
overridden by room freeze protection.
Control Off
When the control is in the Off Mode, relay outputs will be
disabled with the exception of the indoor fan (blower). It
will stay on to meet the
Hot Keep
specification. Indicator
LED’s are all off.
Temperature Range
The maximum operating temperature range is selectable via
the Touchpad and is 60°F to 85°F with the limits included.
The Remote Thermostat selectable operating range is 60°F
to 90°F with limits included. The range is set in the Set-up
menu.
Indoor and Outdoor Fan Operation
The indoor fan can be set to operate on High or Low speed
with the Fan Speed Button on the touchpad. It can also be set
for Continuous or Cycle operation on the touchpad. When
set for Continuous, the “CONT” LED will be on and the fan
will run continuously. When set for Cycle, the “CYCLE”
LED will be on and the fan will turn on at a call for heat or
cooling.
Fan Cycle Operation
On a call for Heating or Cooling, the indoor fan and the
heating source or the compressor will be activated. When the
call is satisfied and the heating source or the compressor is
deactivated, the indoor fan will repeatedly run for 2 minutes
on and the number of minutes selected on the PC Board off,
until the next cut-in cycle. The number of cycles with timing
as described above is determined based on the OFF FAN
CYCLE jumper setting.
Remote T’Stat Mode
The unit can be jumper configured to take commands from
a Remote Thermostat. The Remote Thermostat will call for
Heat and Cool through the electronic controller.
1. The Remote T’stat will control through the board the
work of the compressor, indoor and outdoor fans, the
reversing valve, and the heater
2. System will run in Cool mode when Y signal is high. In
cool mode compressor (therefore outdoor fan) shall turn
on
3. Cold start feature (see Modes of Operation – Cold Start),
Cool dry mode (see Cold Dry Mode) and Sleep feature
(see Sleep Feature) are not available in Remote T’stat
cool mode
4. In T'STAT mode, the fan speed can be changed at the
Touchpad and the fan mode is dictated by the Remote
t'stat.
System Select Operation Using Remote
Thermostat
System will run in Heat mode and engage certain outputs
based on the system selection (jumper) as described below
(see Standard Digital Control Board Wiring Diagram on
page 31).
AC/ELE
• If AC/ELE is selected then a signal on W terminal will
call for heating.
HP or HP/ELE
• If HP or HP/ELE is selected then signals on Y and B
terminals will call for heating.
NOTES:
1. Hot start and Sleep features are not available in
Remote T’stat heat mode.
2. Control’s operation is subject to its own
protection features when controlled by a Remote
T’stat
3. Indoor fan mode and the speed will default
to “cycle” and “high” when unit is controlled by
Remote T’stat
4. The indoor fan is turned on when G signal is
high. When there is no signal on G terminal then
the indoor fan will be turned off.
Summary of Contents for McQuay IM 934-5
Page 46: ......
Page 47: ......
Page 48: ...2013 McQuay International 800 432 1342 www daikinmcQuay com IM 934 5 8 13 Page 48 of 48...