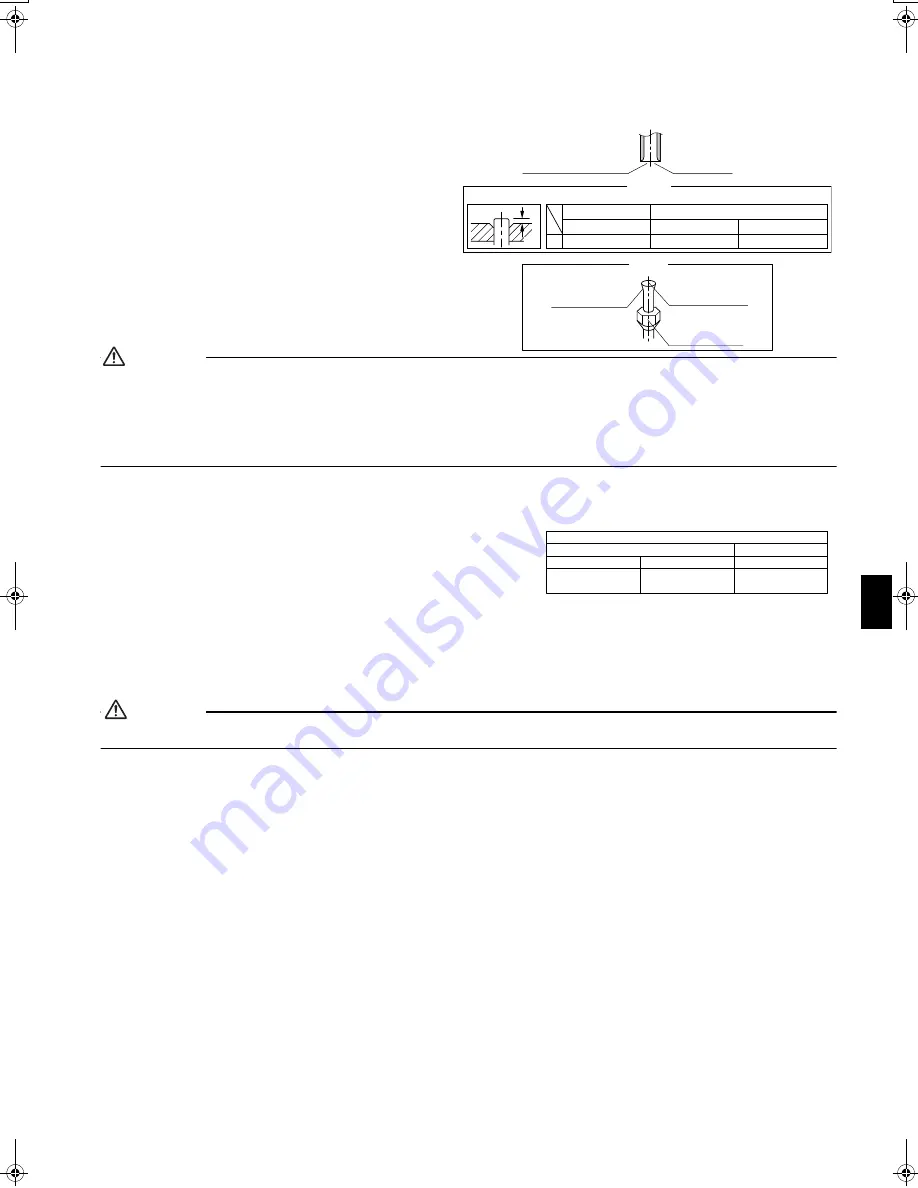
■
English
6
REFRIGERANT PIPING WORK
See the installation manual supplied with the outdoor unit.
1.
FLARING THE PIPE END
1) Cut the pipe end with a pipe cutter.
2) Remove burrs with the cut surface facing downward
so that the chips do not enter the pipe.
3) Put the flare nut on the pipe.
4) Flare the pipe.
5) Check that the flaring is properly made.
Warning
Do not use mineral oil on flared part.
Prevent mineral oil from getting into the system as this would reduce the lifetime of the units.
Never use piping which has been used for previous installations. Only use parts which are delivered with the unit.
Do never install a drier to this R410A unit in order to guarantee its lifetime.
The drying material may dissolve and damage the system.
Incomplete flaring may cause refrigerant gas leakage.
2.
REFRIGERANT PIPING
1) To prevent gas leakage, apply refrigeration machine oil on both
inner and outer surfaces of the flare. (Use refrigeration oil for
R410A)
2) Align the centres of both flares and tighten the flare nuts 3 or 4
turns by hand. Then tighten them fully with the torque wrenches.
• Use torque wrenches when tightening the flare nuts to prevent
damage to the flare nuts and escaping gas.
Caution
Overtightening may damage the flare and cause leaks.
A
A
(Cut exactly at right angles.)
Remove burrs
Flare’s inner surface
must be flaw-free.
The pipe end must
be evenly flared in a
perfect circle.
Make sure that the
flare nut is fitted.
Check
0 ~ 0.5 mm
1.0 ~ 1.5 mm
1.5 ~ 2.0 mm
Set exactly at the position shown below.
Clutch-type
Flare tool for R410A
Clutch-type (Rigid-type) Wing-nut type (Imperial-type)
Conventional flare tool
Flaring
Die
Flare nut tightening torque
Gas side
Liquid side
3/8 inch
1/2 inch
1/4 inch
32.7~39.9N•m
(333~407kgf•cm)
49.5~60.3N•m
(505~615kgf•cm)
14.2~17.2N•m
(144~175kgf•cm)
01_EN_3P132003-2N.fm Page 6 Tuesday, December 5, 2006 2:02 PM