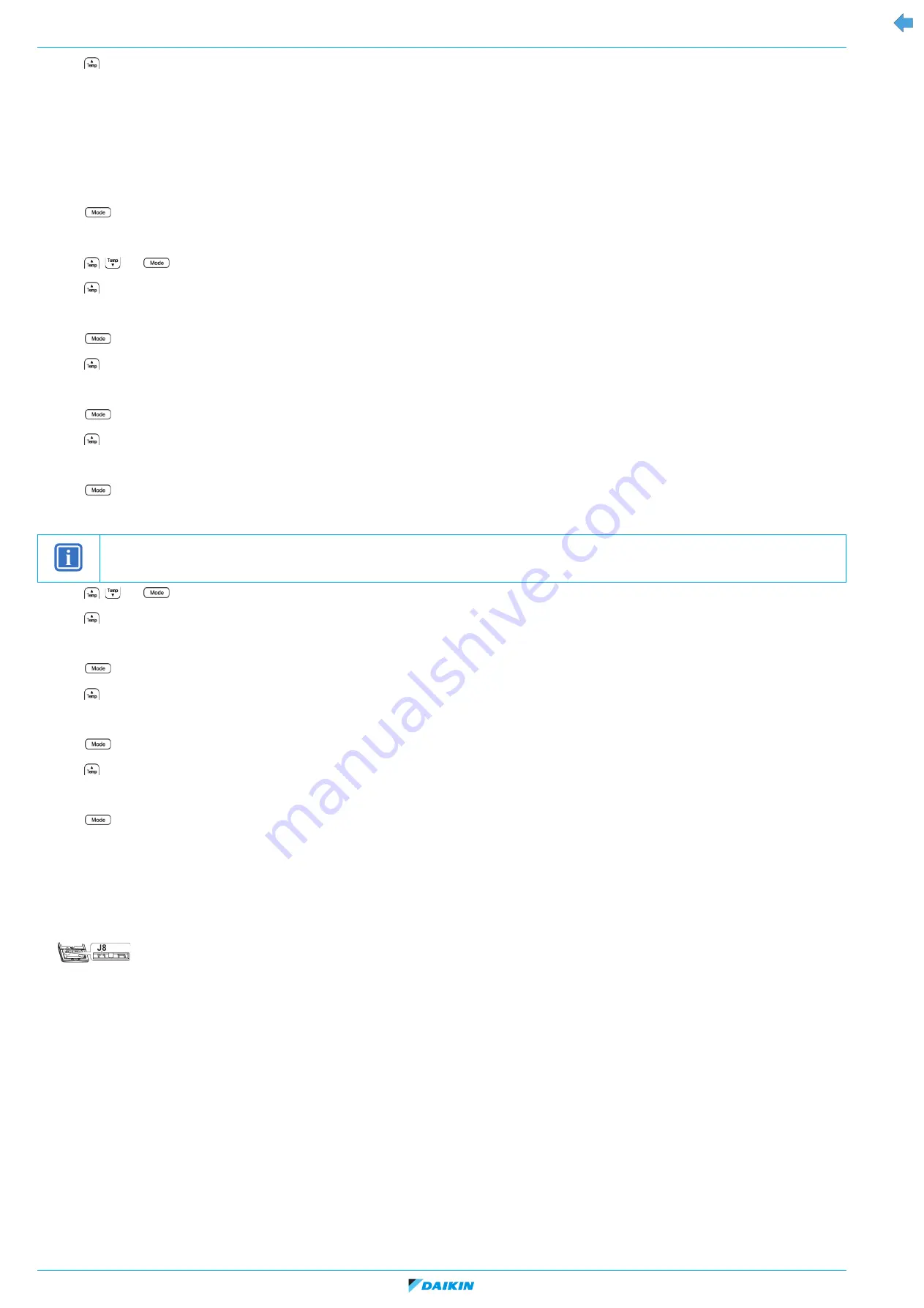
ESIE17-19C
|
Part 5. Appendix
5.1. Field setting
Optimized Heating 4
Page 104
19/08/19
|
Version 1.1
8. Press .
9. Select the value to set the desired target temperature:
- 0=
-2,0°C
- 1=
-1,0°C
-
2= 0°C (factory setting)
- 3=
+1,0°C
- 4=
+2,0°C
10. Press
to confirm.
5.1.1.2.3 To control the indoor unit fan during thermostat off in cooling
1. Press ,
and
simultaneously.
2. Press .
3. Select SU.
4. Press
to confirm.
5. Press .
6. Select 4.
7. Press
to confirm.
8. Press .
9. Select 0 (0: fan ON, 1: fan OFF).
10. Press
to confirm.
5.1.1.2.4 To change auto restart ON to OFF
1. Press ,
and
simultaneously.
2. Press .
3. Select SU.
4. Press
to confirm.
5. Press .
6. Select 10.
7. Press
to confirm.
8. Press .
9. Select 0 (0: auto restart OFF, 1: auto restart ON).
10. Press
to confirm.
5.1.1.2.5 To control cooling mode only
Prerequisite
: Stop operation of the unit (via the user interface, operation switch, ...).
Prerequisite
: Turn OFF the respective circuit breaker.
1. Cut the jumper J8 on the user interface of the indoor unit.
2. Turn ON the unit using the respective circuit breaker.
3. Start the unit operation (via the user interface, operation switch, ...).
I
NFORMATION
After power failure, the unit will automatically restart (default setting). It is possible to switch OFF auto restart. For example: after a long power failure, generators have to start-up. As
there is limited energy and the air conditioners do NOT have priority, it is recommended to switch OFF auto restart.