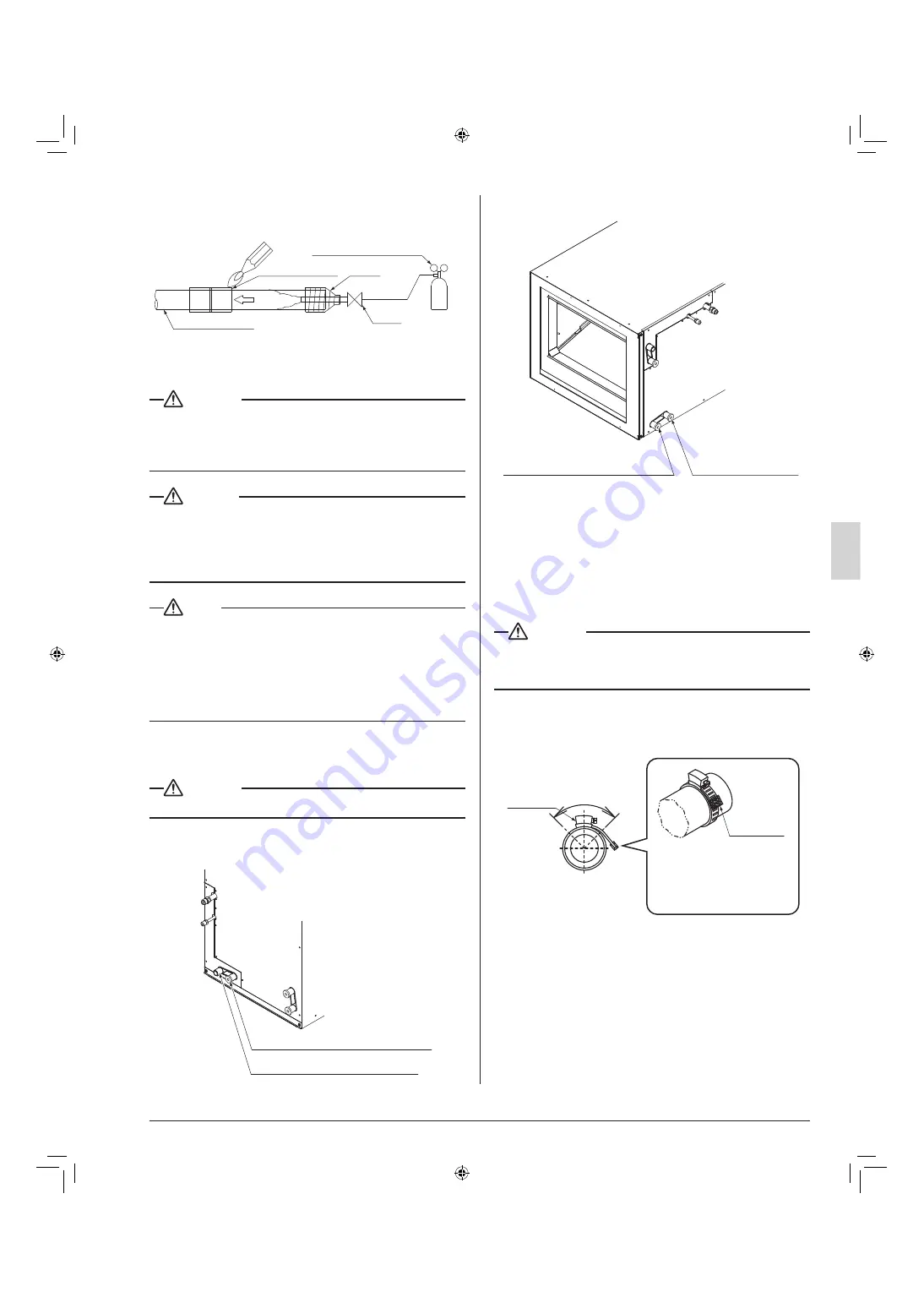
English
8
When brazing the refrigerant piping, perform nitrogen re-
•
placement fi rst, or perform the brazing while feeding nitro-
gen into the refrigerant piping.
(Refer to Fig. 6)
Refrigerant piping
Part to be brazed
Taping
Pressure-reducing valve
hands
valve
Nitrogen
Nitrogen
Fig. 6
CAUTION
When brazing piping while feeding nitrogen inside the
•
piping, make sure to set the nitrogen pressure to 2.9 psi or
less using the pressure reducing valve.
(This pressure is such that a breeze is blown to your cheek.)
DANGER
Use of oxygen could result in an explosion resulting in
•
serious injury or death. Only use dry nitrogen gas.
Refrigerant gas may produce toxic gas if it comes in contact
•
with fi re such as from a fan heater, stove or cooking device.
Exposure to this gas could cause severe injury or death.
NOTE
Do not use fl ux when brazing refrigerant piping. Therefore,
•
use the phosphor copper brazing fi ller metal (BCuP) which
does not require fl ux.
Flux has an extremely negative effect on refrigerant piping
systems. For instance, if chlorine based fl ux is used, it will
cause piping corrosion. Flux containing fl uorine will damage
refrigerant oil.
DRAIN PIPING WORK
6.
CAUTION
Make sure all water is out before making the duct connection.
•
Install drain piping as described Fig. 7.
(1)
Secondary drain piping connection hole
Primary drain piping connection hole
In case of vertical installation
Fig. 7-1
Primary drain piping connection hole
Secondary drain piping
connection hole
In case of horizontal installation
Fig. 7-2
Perform drain work so that the unit is drained thoroughly.
•
(Be sure to insulate the following 2 locations since
condensation may cause water leakage.)
Be sure to use the included Drain hose (5) and Metal
•
clamp (4).
Insert the Drain hose (5) up to the step on the drain
socket. Within the range of the tape section at the
end of the inserted hose, tighten the Metal clamp (4)
to the torques of 0.99 ± 0.1 lbf·ft (11.9 ± 1.2 lbf·in).
CAUTION
Do not tighten the Metal clamp (4) to torques exceeding the
•
specifi cation. Otherwise, the Drain hose (5), the socket, and
the Metal clamp (4) may become damaged.
To avoid the Sealing pad (large) (9) from tearing at the
•
edge of the Metal clamp (4), either affi x a plastic tape
on the edge of the Metal clamp (4) or bend the end of
the Metal clamp (4) inward as shown in the fi gure.
Plastic tape
To avoid tearing the Sealing
pad (large) (9), affix a
plastic tape.
Tightening
section
Approx. 90°
<When affixing plastic tape>
Cross section A-A
01_EN_3P250363-4C.indd 8
01_EN_3P250363-4C.indd 8
12/28/2011 11:51:50 AM
12/28/2011 11:51:50 AM