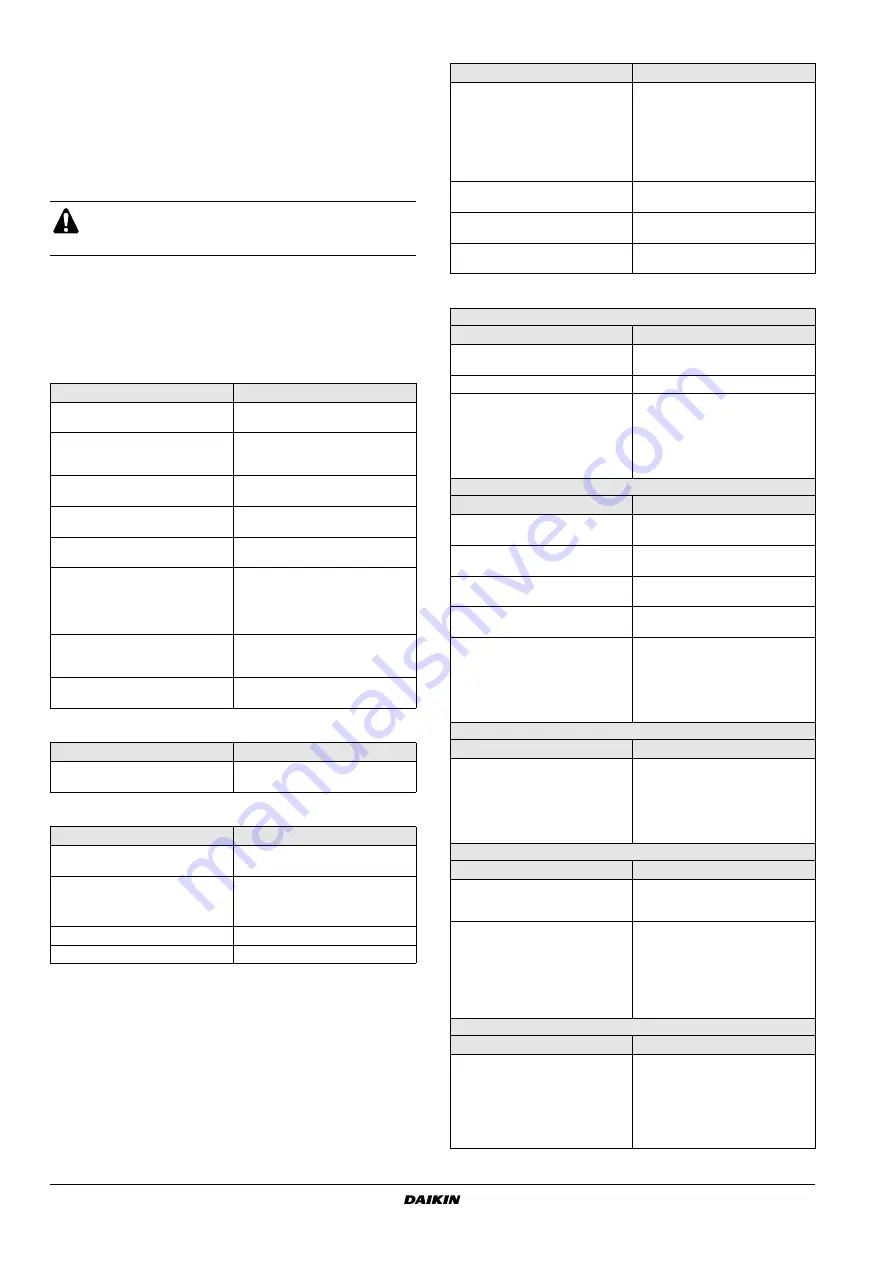
Operation manual
19
EWWP045~06 ECB1~3MUW
Packaged water-cooled water chillers
4PW30041-1A
T
ROUBLESHOOTING
This section provides useful information for diagnosing and correct-
ing certain troubles which may occur in the unit.
Before starting the trouble shooting procedure, carry out a thorough
visual inspection of the unit and look for obvious defects such as
loose connections or defective wiring.
Before contacting your local dealer, read this chapter carefully, it will
save you time and money.
When a safety device was activated, stop the unit and find out why
the safety device was activated before resetting it. Under no circum-
stances safety devices may be bridged or changed to a value other
than the factory setting. If the cause of the problem cannot be found,
call your local dealer.
Symptom 1: The unit does not start, but the ON LED lights up
Symptom 2: The unit does not start, but the ON LED is flashing
Symptom 3: The unit does not start and the ON LED does not light up
Symptom 4: One of the circuits does not start up
Symptom 5: One of the following safety devices is activated
When carrying out an inspection on the supply panel or on
the switch box of the unit, always make sure that the circuit
breaker of the unit is switched off.
P
OSSIBLE
CAUSES
C
ORRECTIVE
ACTION
The temperature setting is not
correct.
Check the controller setpoint.
The flowstart timer is still running.
The unit will start after approx. 15
seconds. Make sure that water is
flowing through the evaporator.
Neither one of the circuits can start
up.
Refer to
.
Unit is in manual mode (all
compressors at 0%).
Check on the controller.
Power supply failure.
Check the voltage on the supply
panel.
Blown fuse or interrupted protection
device.
Inspect fuses and protection
devices. Replace by fuses of the
same size and type (refer to
"Electrical specifications" on
page 2
Loose connections.
Inspect connections of the field
wiring and the internal wiring of the
unit. Tighten all loose connections.
Shorted or broken wires.
Test circuits using a tester and repair
if necessary.
P
OSSIBLE
CAUSES
C
ORRECTIVE
ACTION
The remote ON/OFF input is
enabled and the remote switch is off.
Put the remote switch on or disable
the remote ON/OFF input.
P
OSSIBLE
CAUSES
C
ORRECTIVE
ACTION
All circuits are in failure mode.
Refer to
following safety devices is activated
One of the following safety devices is
activated:
• Flow switch (S8L,S9L)
• Emergency stop
Refer to
following safety devices is activated
The ON LED is broken.
Contact your local dealer.
The unit is in bypass mode.
Check the bypass remote contact.
P
OSSIBLE
CAUSES
C
ORRECTIVE
ACTION
One of the following safety devices is
activated:
• Compressor thermal protector (Q*M)
• Overcurrent relay (K*S)
• Discharge thermal protector (S*T)
• Low pressure switch
• High pressure switch (S*HP)
• Reverse phase protector (R*P)
• Freeze-up
Check on the controller and refer to
Symptom 5: One of the following
safety devices is activated
.
The anti-recycling timer is still active.
The circuit can only start up after
approximately 10 minutes.
The guard timer is still active.
The circuit can only start up after
approximately 1 minute.
The circuit is limited to 0%.
Check the "enable/disable capacity
limitation" remote contact.
Symptom 5.1: Overcurrent relay of compressor
P
OSSIBLE
CAUSES
C
ORRECTIVE
ACTION
Failure of one of the phases.
Check fuses on the supply panel or
measure the supply voltage.
Voltage too low.
Measure the supply voltage.
Overload of motor.
Reset. If the failure persists, call your
local dealer.
RESET
Push the blue button on the over-
current relay inside the switch box
and reset the controller.
Symptom 5.2: Low pressure switch
P
OSSIBLE
CAUSES
C
ORRECTIVE
ACTION
Water flow to water heat exchanger
too low.
Increase the water flow.
Shortage of refrigerant.
Check for leaks and refill refrigerant,
if necessary.
Unit is working out of its operation
range.
Check the operation conditions of
the unit.
Inlet temperature to the water heat
exchanger is too low.
Increase the inlet water temperature.
Flow switch is not working or no
water flow.
Check the flow switch and the water
pump.
RESET
After pressure rise, this safety resets
automatically, but the controller still
needs to be reset.
Symptom 5.3: High-pressure switch
P
OSSIBLE
CAUSES
C
ORRECTIVE
ACTION
Water flow to condenser is too low.
Increase the water flow and/or check
the strainer for clogging.
RESET
After finding the cause, push the
button on the high-pressure switch
housing and reset the controller.
Symptom 5.4: Reverse phase protector is activated
P
OSSIBLE
CAUSES
C
ORRECTIVE
ACTION
Two phases of the power supply are
connected in the wrong phase
position.
Invert two phases of the power
supply (by licensed electrician).
One phase is not connected
properly.
Check the connection of all phases.
RESET
After inverting two phases or fixing
the power supply cables properly,
the protector is reset automatically,
but the controller still needs to be
reset.
Symptom 5.5: Discharge thermal protector is activated
P
OSSIBLE
CAUSES
C
ORRECTIVE
ACTION
Unit is working outside the operation
range.
Check the operation condition of the
unit.
RESET
After temperature decrease, the
thermal protector resets
automatically but the controller still
needs to be reset.