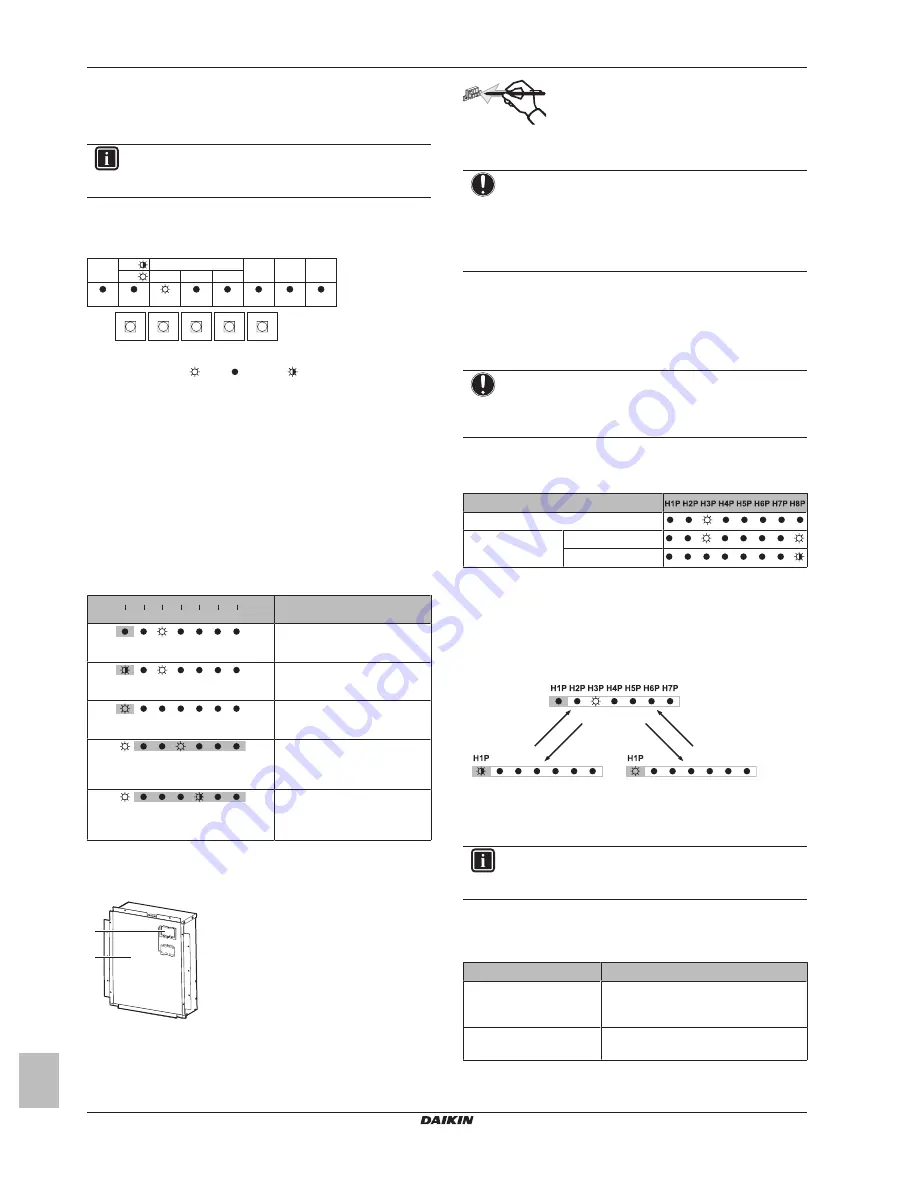
6 Configuration
Installation and operation manual
14
EWAQ016~ EWYQ016~064CAW
Packaged air-cooled water chiller
4P489435-1B – 2017.10
To continue the configuration of the system, it is required to give
some input to the PCB of the unit. This chapter will describe how
manual input is possible by operating the pushbuttons/DIP switches
on the PCB and reading the feedback from the LEDs.
INFORMATION
If you get confused in the middle of the process, push BS1.
Then it returns to setting mode 1 (H1P is off).
6.2.2
Field setting components
The components to make field settings are as follows:
BS2
SET
BS1
MODE
BS3
RETURN
BS4
TEST
BS5
RESET
H7P
MODE
TEST:
L.N.O.P. DEMAND
C/H SELECT
HWL:
IND MASTER SLAVE
MULTI
H1P
H2P
H3P
H4P
H5P
H6P
H8P
BS1~BS5
Pushbuttons
H1P~H8P
LEDs
ON (
) OFF ( ) Flashing (
)
Pushbuttons
Use the pushbuttons to make the field settings.
BS1
MODE: For changing the set mode
BS2
SET: For field setting
BS3
RETURN: For field setting
BS4
Not used
BS5
Not used
LEDs
The LEDs give feedback about the field settings, which are defined
as [Mode-Setting]=Value.
H1P
Shows the mode
H2P~H7P
Shows the settings and values, represented in binary code
H8P
NOT used for field settings, but used during initialisation
Example:
H1P H2P H3P H4P H5P H6P H7P
-
+
+
+
+
+
[
H1P
32 16
8
4
2
1]
Description
(H1P OFF)
Default situation
(H1P flashing)
Mode 1
(H1P ON)
Mode 2
+
+
+
+
+
0
0
8
0
0
0
(H2P~H7P = binary 8)
Setting 8
(in mode 2)
+
+
+
+
+
0
0
0
4
0
0
(H2P~H7P = binary 4)
Value 4
(in mode 2)
6.2.3
To access the field setting components
Remove the inspection cover to carry out field settings.
b
a
Operate the switches and pushbuttons with an insulated stick (such
as a closed ball-point pen) to avoid touching of live parts.
Make sure to re-attach the inspection cover into the electrical
component box cover after the job is finished.
NOTICE
Make sure that all outside panels, except for the service
cover on the electrical component box, are closed while
working.
Close the lid of the electrical component box firmly before
turning on the power.
6.2.4
To access mode 1 or 2
After the units are turned ON, the display goes to its default
situation. From there, you can access mode 1 and mode 2.
Initialisation: default situation
NOTICE
Be sure to turn on the power 6 hours before operation in
order to have power running to the crankcase heater and
to protect the compressor.
Turn on the power supply of the outdoor unit, and turn on the
external operation switch. After initialisation, the display indication
state will be as below (default situation when shipped from factory).
Single unit
Multi-unit
Left unit (master)
Right unit (slave)
If the default situation is not displayed after 10~12 minutes, check
the malfunction code. Solve the malfunction code accordingly.
The HAP LED flashes to indicate normal microcomputer operation.
Switching between modes
Use BS1 to switch between the default situation, mode 1 and
mode 2.
BS1 [5 s]
BS1
BS1
BS1
a
c
b
a
Default situation (H1P OFF)
b
Mode 1 (H1P flashing)
c
Mode 2 (H1P ON)
BS1
Press BS1.
BS1 [5 s]
Press BS1 for at least 5 s.
INFORMATION
If you get confused in the middle of the process, press BS1
to return to the default situation.
6.2.5
To use mode 1
Mode 1 is used to monitor the status of the unit.
What
How
Accessing monitoring
mode 1
Once mode 1 is selected (push BS1
one time), you can select the wanted
setting. It is done by pushing BS2.
To quit and return to the
initial status
Press BS1.
Summary of Contents for EWAQ016CAW
Page 37: ......
Page 38: ......
Page 39: ......
Page 40: ...4P489435 1B 2017 10 Copyright 2017 Daikin 4P489435 1 B 00000004...