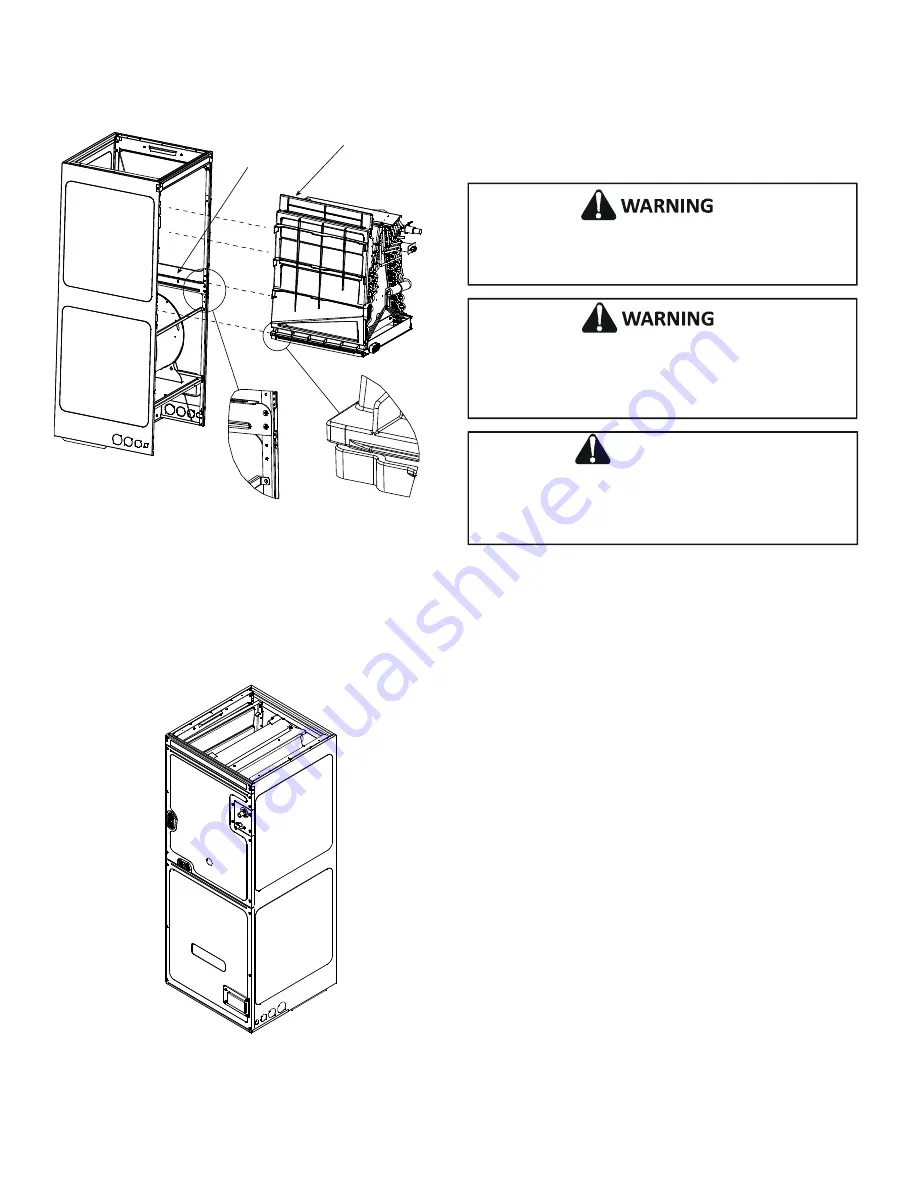
7
4. Using the drain pan to hold the coil assembly, slide the coil
assembly back into the cabinet on the downflow brackets as
shown in Figure 8.
Coil Slides on the
downflow bracket
IMPORTANT NOTE:
Ensure coil slides on the rails along the groove provided on the drain pan side walls.
Failure to do so will resul
�
n improper condensate drainage.
Remove Drain Pan Extension
before inserting coil for
downflow application
COIL INSTALLATION FOR DOWNFLOW
Figure 8
5. Re-install the center support (if removed) using the two (2)
screws removed in Step 4.
6. Re-install the access panels removed in Step 1 as shown in
Figure 9.
ACCESS PANEL CONFIGURATION FOR DOWNFLOW OR
HORIZONTAL RIGHT
Figure 9
7. The bottom left drain connection is the primary drain for
this application and condensate drain line must be attached
to this drain connection. The top connection of the three
drain connections on the drain pan must remain plugged for
this application. The bottom left drain connection is for the
secondary drain line (if used).
7 Refrigerant Lines
This product is factory-shipped with R410A and dry nitrogen
mixture gas under pressure. Use appropriate service tools and
follow these instructions to prevent injury.
A quenching cloth is strongly recommended to prevent
scorching or marring of the equipment finish when brazing
close to the painted surfaces. Use brazing alloy of 5% minimum
silver content.
Applying too much heat to any tube can melt the tube. Torch
heat required to braze tubes of various sizes must be
proportional to the size of the tube. Service personnel must
use the appropriate heat level for the size of the tube being
brazed
.
CAUTION
NOTE:
Refrigerant tubing must be routed to allow adequate
access for servicing and maintenance of the unit.
Do not install the air handler in a location that violates the
instructions provided with the condenser. If the unit is located in
an unconditioned area with high ambient temperature and/or high
humidity, the air handler may be subject to nuisance sweating
of the casing. On these installations, a wrap of 2” fiberglass
insulation with a vapor barrier is recommended.
7.1 Tubing Size
For the correct tubing size, follow the specification for the
condenser/heat pump.
7.2 Tubing Preparation
All cut ends are to be round, burr free, and clean. Failure to
follow this practice increases the chances for refrigerant leaks.
The suction line is spun closed and requires tubing cutters to
remove the closed end.
NOTE: To prevent possible damage to the tubing joints, do not
handle coil assembly with manifold or flowrator tubes. Always
use clean gloves when handling coil assemblies.
NOTE: The use of a heat shield is strongly recommended when
brazing to avoid burning the serial plate or the finish of the unit.
Heat trap or wet rags must be used to protect heat sensitive
components such as service valves and TXV valves sensing
bulb.
7.3 Tubing Connections for TXV Models
TXV models come with factory installed TXV with the bulb
pre-installed on the vapor tube.
1. Remove refrigerant tubing panel or coil (lower) access panel.
2. Remove access valve fitting cap and depress the valve stem
in access fitting to release pressure. No pressure indicates
possible leak.