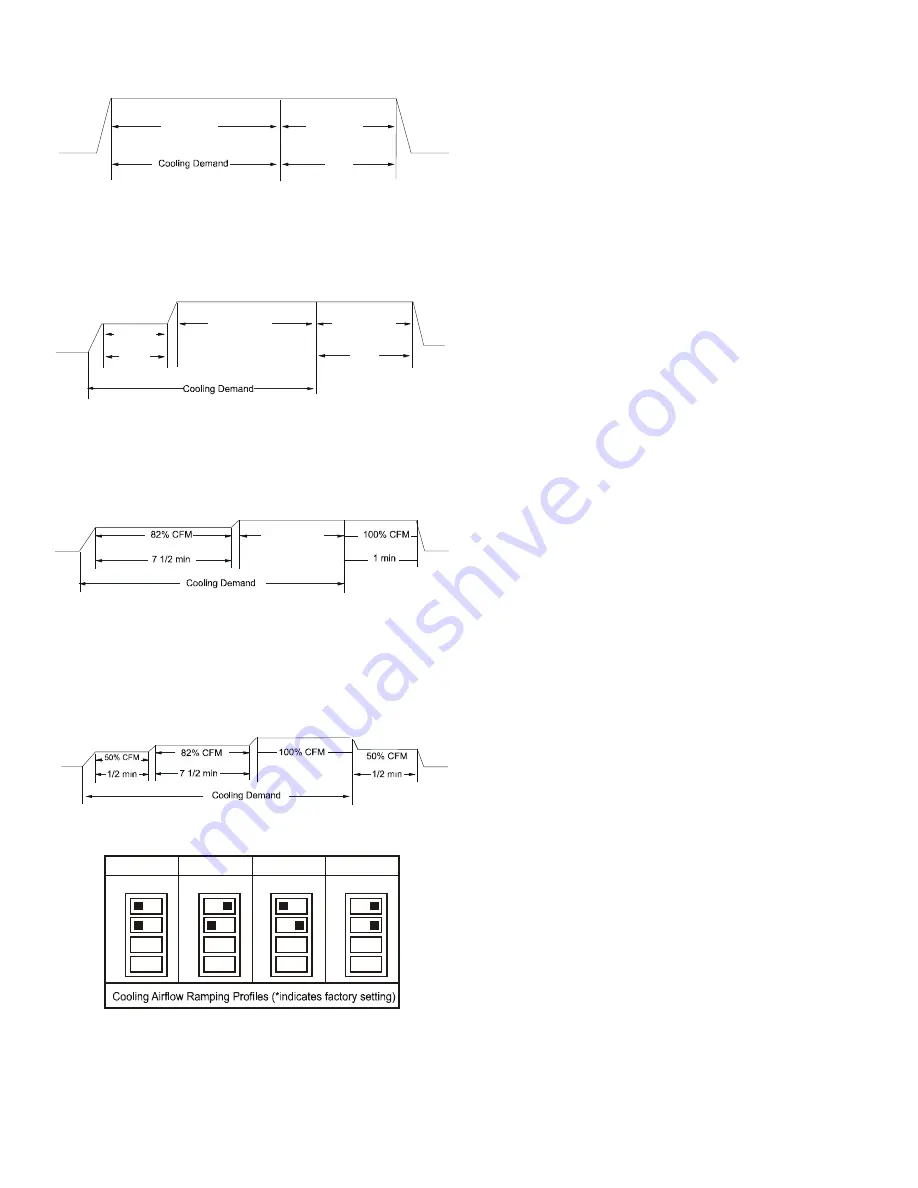
18
• Profile A provides only an OFF delay of one (1) minute at
100% of the cooling demand airflow.
OFF
100% CFM
100% CFM
1 min
OFF
Figure 26
• Profile B ramps up to full cooling demand airflow by first
stepping up to 50% of the full demand for 30 seconds. The
motor then ramps to 100% of the required airflow. A one (1)
minute OFF delay at 100% of the cooling airflow.
50% CFM
1/2 min
100% CFM
100% CFM
1 min
OFF
OFF
Figure 27
• Profile C ramps up to 82% of the full cooling demand airflow
and operates there for approximately 7 1/2 minutes. The
motor then steps up to the full demand airflow. Profile C also
has a one (1) minute 100% OFF delay.
100% CFM
OFF
OFF
Figure 28
• Profile D ramps up to 50% of the demand for 1/2 minute,
then ramps to 82% of the full cooling demand airflow and
operates there for approximately 7 1/2 minutes. The motor
then steps up to the full demand airflow. Profile D has a 1/2
minute at 50% airflow OFF delay.
OFF
OFF
Figure 29
S5
S6
S5
S6
S5
S6
S5
S6
OFF
OFF
OFF
OFF
ON
ON
ON
ON
Tap A*
Tap B
Tap C
Tap D
Dip Switches - Cooling Airflow Ramping Profiles
Figure 30
7. If an electric heater kit has been installed, determine the
heater kilowatt (kW) rating. Using the Electric Heat Airflow
table on page 16, set dip switches 9, 10, and 11 for the
installed heater. The adjust setting (already established
by the cooling speed selection) also applies to the electric
heater kit airflow meaning electric heater airflow is adjusted
by the same amount. This does not apply to systems setup
with a communicating thermostat. Verify selected CFM by
counting the green CFM LED blinks.
If an electric heater kit has not been installed, set dip
switches 9, 10, and 11 to any valid heater kit setting (see
airflow table for valid settings). This will prevent an Ec Error
code from being displayed.
NOTE:
For installations not indicated in the preceding
Temperature Rise Tables, the following formula is to be used:
TR = (kW x 3412) x (Voltage Correction) / (1.08 x CFM)
Where:
TR
= Temperature Rise
kW = Heater Kit Actual kW
3412
= Btu per kW
Voltage Correction =.96 (230 Supply Volts)
=.92 (220 Supply Volts)
=.87 (208 Supply Volts)
1.08 = Constant
CFM = Measured Airflow
NOTE:
The Temperature Rise Tables can also be used to
determine the air handler airflow delivery. When using these
tables for this purpose set the room thermostat to maximum heat
and allow the system to reach steady state conditions. Insert two
thermometers, one in the return air and one in the supply air. The
temperature rise is the supply air temperature minus the room air
temperature.
Use HKR specification sheets to determine the HKR available for
a given air handler.
Heat Kit Selection
For heat kit selection, see the Specification Sheet for each
specific Air Handler.
17 Troubleshooting
17.1 Electrostatic Discharge (ESD) Precautions
NOTE:
Discharge body’s static electricity before touching
unit. An electrostatic discharge can adversely affect electrical
components.
Use the following precautions during air handler installation
and servicing to protect the integrated control module from
damage. By putting the air handler, the control, and the person
at the same electrostatic potential, these steps will help avoid
exposing the integrated control module to electrostatic discharge.
This procedure is applicable to both installed and uninstalled
(ungrounded) blowers.
1. Disconnect all power to the blower. Do not touch the
integrated control module or any wire connected to the
control prior to discharging your body’s electrostatic charge
to ground.
2. Firmly touch a clean, unpainted, metal surface of the air
handler blower near the control. Any tools held in a person’s
hand during grounding will be discharged.
3. Service integrated control module or connecting wiring