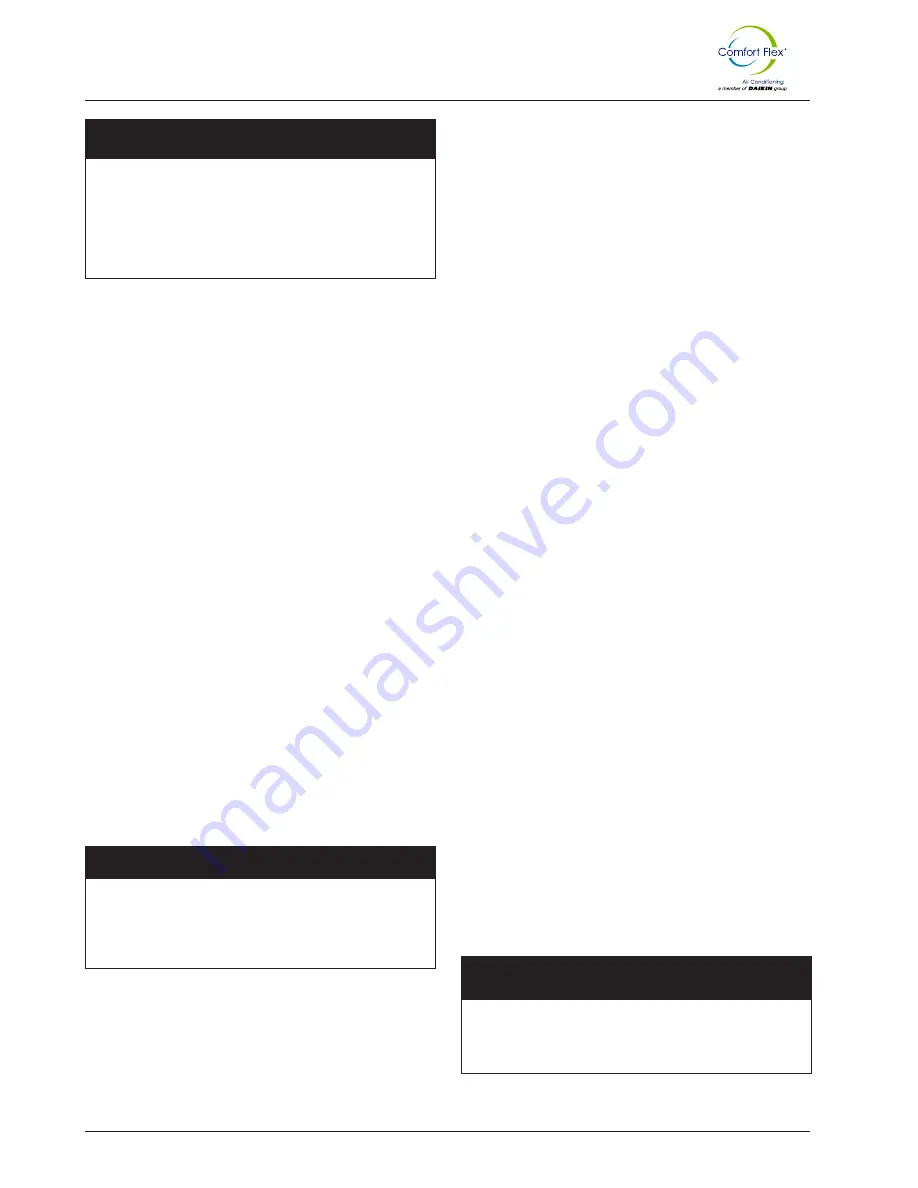
iom-cliv-eng
www.comfort-flex.com
11
!
CAUTION
!
Adding glycol or draining the system is the recommended
method of freeze protection. If the chiller does not have
the ability to control the pumps and the water system is not
drained or does not have adequate glycol at subfreezing
temperatures, catastrophic evaporator failure can occur.
FLOW SWITCH
All chillers require a chilled water flow switch to verify that there
is adequate water flow through the evaporator and to shut down
the unit if necessary to prevent evaporator freeze-up under low or
no flow conditions.
A factory-installed thermal dispersion flow switch will be installed
on packaged models. On remote evaporator models, the flow
switch can be supplied separately in the field, or optionally
shipped loose for field installation.
Terminals for field mounting and wiring of the water flow switch
are provided in the unit control center.
Wire from the Y and R terminals on the switch to the terminals on
the unit control panel shown in the field wiring diagrams, page 21
through page 26. Mount the flow switch on the outlet water line
to shut off the unit when water flow is interrupted. A flow switch
is an equipment protection control and should never be used to
cycle the unit.
Installation should be in accordance with the manufacturer’s
instructions included with the switch. Flow switches should be
calibrated to shut the unit off when operating below the minimum
flow rate.
There is also a set of paddle switch contacts on the switch that
can be used for an indicator light or alarm to indicate when a “no
flow” condition exists. Protect any flow switches that are installed
outdoors from freezing. It is not recommended that differential
pressure switches be installed outdoors. They may freeze and
not indicate a no-flow condition.
EVAPORATOR FREEZE PROTECTION
Evaporator freezing can be a problem in the application of air-
cooled water chillers in sub-zero temperature areas. To protect
against freezing, the evaporator comes with insulation and an
electric heater.
Although the evaporator is equipped with freeze protection,
it does not protect the water piping external to the unit or the
evaporator itself if there is a power failure or the heater burns out,
or if the chiller cannot control the chilled water pumps. Use one of
the following recommendations for additional freeze protection:
COLD WATER PUMP
It is important that the chilled water pumps are connected to
and controlled by the chiller microprocessor. The controller will
activate the pump whenever at least one chiller circuit is enabled
for operation, whether there is a call for cooling or not.
This helps ensure proper start-up sequencing of the unit. The
pump will also turn on when the water temperature is below the
freeze set point for longer than the specified time to help prevent
evaporator freeze-up. Connection points are shown in the field
wiring diagram beginning on page 21+.
1. If the unit will not operate during the winter, drain the evapora-
tor and cold water lines and flush them with glycol.
2. Add a glycol solution to the chilled water system. Breakage
protection should be approximately 10°F below the minimum
design ambient temperature.
3. Insulate exposed piping.
4. Add thermostatically controlled heat by wrapping lines with
heat tape.
5. When glycol is added to the water system for freeze protec-
tion, the refrigerant suction pressure will be lower, the cooling
performance will be lower, and the water side pressure drop
will be higher.
If the chiller is not allowed to control the pump, the following
problems may occur:
1. if the chiller attempts to start without first starting the pump,
the chiller will lock out with the no flow alarm and require a
manual restart.
!
CAUTION
!
Improper use of detergents, chemicals and additives in the
cooling system water can adversely affect the performance
of the chiller and potentially result in repair costs not covered
under warranty. Any decision to use these products is at
the discretion of the owner/occupant/operator/user, and the
owner/occupant/operator/user assumes full responsibility for
any damage that may occur due to their use.
Installation and Application Information
GLYCOL SOLUTIONS
The use of glycol can affect system performance depending on
its concentration and should be taken into account during initial
system design. When glycol is added to the chilled water system
to protect against freezing, it should be noted that the refrigerant
suction pressure will be lower, the cooling performance will
be lower and the water side pressure drop will be higher. The
reduction in performance depends on the glycol concentration
and temperature. Test the coolant with a clean and accurate
glycol refractometer to determine the freezing point.
!
CAUTION
!
The installed glycol level must match the nominal glycol
percentage indicated on the submitted chiller technical data
sheet. Failure to meet the nominal glycol percentage may
result in damage to the unit and loss of unit warranty.
2. If the chiller evaporator water temperature drops below the
“freezing set point”, the chiller will attempt to start the water
pumps to prevent the evaporator from freezing.
3. If the chiller does not have the ability to start the pumps, the
chiller will alarm for lack of water flow.
4. If the chiller does not have the ability to control the pumps
and the water system must not be drained in sub-zero tem-
peratures or contain glycol, the chiller may be subject to cat-
astrophic evaporator failure due to freezing. The evaporator
freeze-up rate is based on the evaporator heater and pump
operation. The external brazed plate heater alone may not
be able to adequately protect the evaporator from freezing
without water circulation.