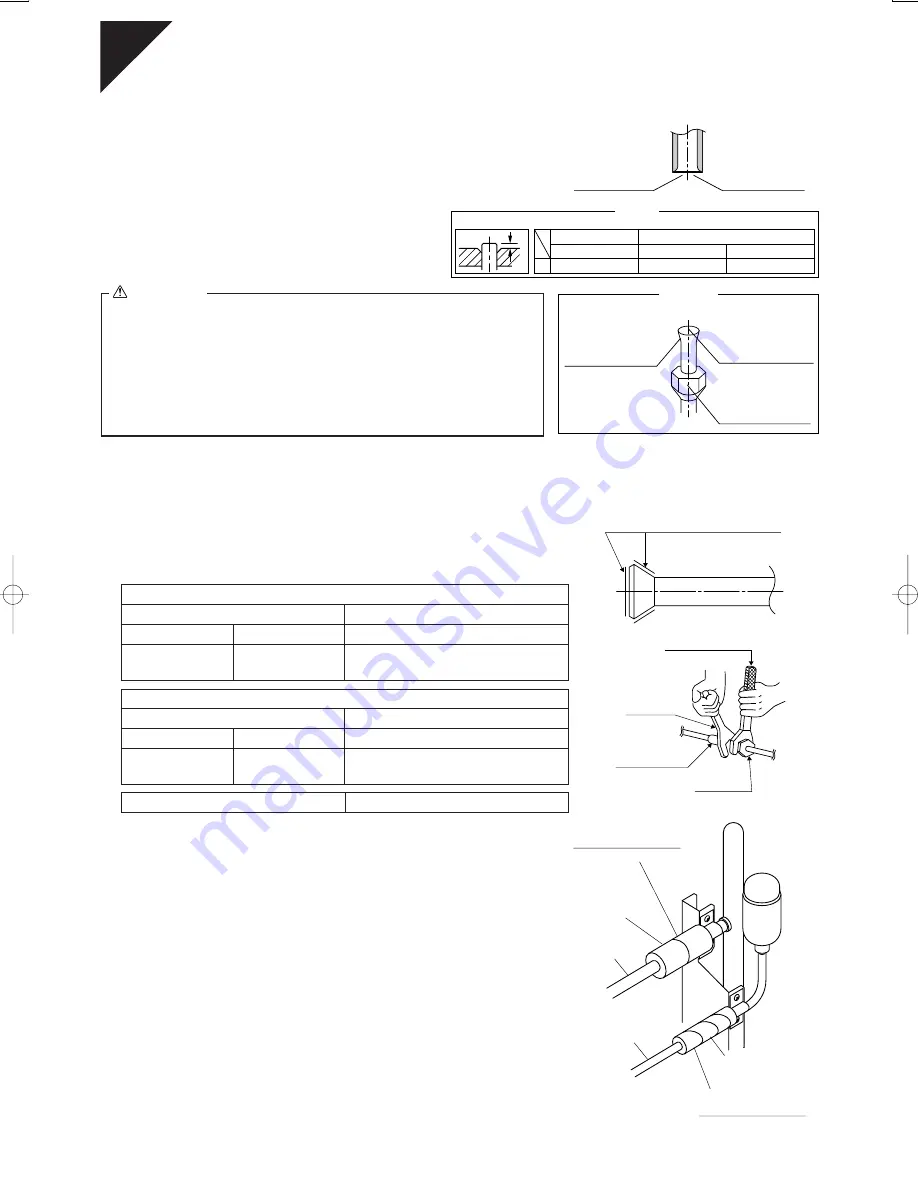
5
Coat here with
refrigeration machine oil
Torque wrench
Piping union
Flare nut
Spanner
Insulation for fitting
(attached)
(For gas pipe)
Large sealing pad
(attached)
Gas pipe
Liquid pipe
Insulation for fitting
(attached)
(For liquid pipe)
Small sealing pad
(attached)
(Cut exactly at
right angles.)
Remove burrs
Set exactly at the position shown below.
A
Flaring
Die
A
0 ~ 0.5 mm
Clutch-type
Flare tool for R-410A
1.0 ~ 1.5 mm
Clutch-type (Rigid-type)
1.5 ~ 2.0 mm
Wing-nut type (Imperial-type)
Conventional flare tool
Check
Flare's inner
surface must be
flaw-free.
The pipe end
must be evenly
flared in a
perfect circle.
Make sure that
the flare nut is
fitted.
REFRIGERANT PIPING WORK
See the installation manual supplied with the Multi outdoor unit for outdoor unit.
1
FLARING THE PIPE END
1. Cut the pipe end with a pipe cutter.
2. Remove burrs with the cut surface facing
downward so that the chips do not enter the pipe.
3. Put the flare nut on the pipe.
4. Flare the pipe.
5. Check that the flaring is properly made.
WARNING
Do not use mineral oil on flared part.
Prevent mineral oil from getting into the system as this would reduce the
lifetime of the units.
Never use piping which has been used for previous installations. Only use
parts which are delivered with the unit.
Do never install a drier to this R-410A unit in order to guarantee its lifetime.
The drying material may dissolve and damage the system.
Incomplete flaring may cause refrigerant gas leakage.
2
REFRIGERANT PIPING
1. Align the centres of both flares and tighten the flare nuts 3 or 4 turns by hand.
Then tighten them fully with the torque wrenches.
●
Use torque wrenches when tightening the flare nuts to prevent damage to
the flare nuts and escaping gas.
2. To prevent gas leakage, apply refrigeration machine oil on both inner and
outer surfaces of the flare. (Use refrigeration oil for R-410A)
●
Wrap only the gas line side with the sealing pad. Bend the pad over the
insulation for fitting (union) from above.
Flare nut tightening torque
Gas side
Liquid side
3/8 inch
1/2 inch
1/4 inch
32.7~39.9 N•m
49.5~60.3 N•m
14.2~17.2 N•m
(333~407 kgf•cm) (505~615 kgf•cm)
(144~175 kgf•cm)
Service port cap tightening torque
10.8~14.7 N•m (110~150 kgf•cm)
Valve cap tightening torque
Gas side
Liquid side
3/8 inch
1/2 inch
1/4 inch
21.6~27.4 N•m
26.5~32.3 N•m
21.6~27.4 N•m
(220~280 kgf•cm) (270~330 kgf•cm)
(220~280 kgf•cm)
Summary of Contents for CDKS25BVMB
Page 11: ...2P098794 3 M02B075 0210 HT...