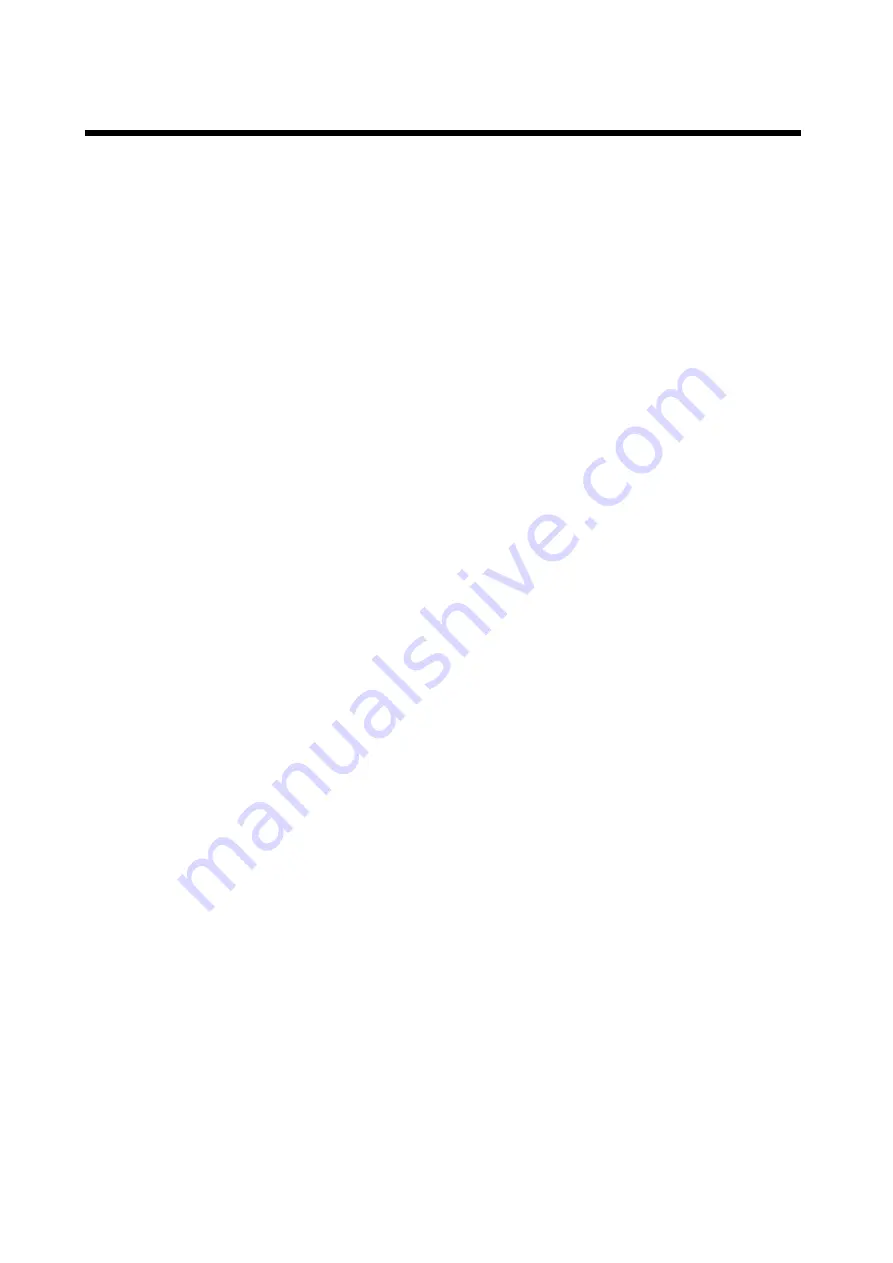
D-EIMWC00908-16EN - 38/52
Operation
Capacity Control System
The capacity of the chiller is controlled by:
1. Staging the compressors on and off;
2. By adjusting the capacity of each compressor by opening or closing the inlet vanes to control the quantity of
refrigerant entering the impeller; and,
3. Varying compressor speed to change capacity.
The speed control and vane control work in conjunction. As load decreases, compressor speed is reduced as low as
possible but above the point where stall might begin. If further capacity reduction is required, the guide vanes will close to
whatever position is required to match the compressor capacity to the load.
Surge and Stall
Stall and surge are a characteristic of all centrifugal compressors. These conditions can occur at low load conditions
when the operating point moves to the left of the compressor surge line on the performance curve.
In surge, the discharge gas alternately flows backward and forward through the impeller reversing about every two
seconds. Increased noise, vibration and heat occur and motor current varies widely. Surge can damage a compressor.
The compressors are equipped with safety features that help prevent surge from occurring.
Another instability is stall or incipient surge, which occurs a little to the left, or before, the surge condition. Discharge gas
in the diffuser forms rotating stall pockets or cells. The compressor sound level will change and the impeller starts to heat
up. Motor current remains steady.
Normal Unit Startup/Shutdown
Startup and shutdown, other than seasonal shutdowns, are considered to be normal operation and the following
procedures apply (assuming that the equipment room temperature are above freezing). The procedures would be used
for a weekend shutdown, for example.
Note that the chiller is part of an entire building heating and cooling system that are usually unique to a particular site.
For example, the chilled water loop and chilled water pump can also be used for heating and therefore must be
operational year-around. The cooling tower can be used for other equipment besides the chiller and may have to remain
functional even though the chiller is not. The following procedures, therefore, must take the peculiarities of the entire
system into account.
Shutdown
If the unit is to be secured for several days, and is already off due to lack of load, the UNIT switch in the Unit Control
Panel (and the remote Start/Stop switch, if used) should be placed in the OFF position. If the chilled water pump and
cooling tower are not required for other purposes, they too can be turned off. If the pumps are controlled by the unit
controller, they will shut down after the compressors.
If the chiller is running, the chilled water and condenser water pumps must remain on until the compressors are stopped.
This is true regardless of how the unit is turned off, whether by the local switches or through a remote signal. The
compressors go through a short shutdown sequence, shutting guide vanes and performing other functions, before it
finally stops. The pumps must remain on during this shutdown period.
Once the compressors and pumps have stopped, no further action is required other than opening disconnects, if so
desired.
Startup
Any disconnects that were opened must be closed. The chilled water pump and cooling tower should be turned on and
flow verified. The chiller can then be started by placing the UNIT switch (and the remote Start/Stop switch, if used) in the
ON position. There is no lube warm-up period required. The compressors go through a starting sequence and may not
start immediately. Once started, it is prudent to observe unit operation on the operator interface screen for several
minutes to check for normal functioning.
Start/Stop Switching
There are four ways to start/stop the chiller. Three are selected in SETPOINT\ MODE\SP3, the fourth way is through
panel-mounted switches:
1.
Operator Interface Panel,
(LOCAL) Home Screen 1 has AUTO and STOP buttons that are only active when the unit
is in "LOCAL CONTROL". This prevents the unit from being accidentally started or stopped when it is under control
from a remote switch or BAS. When these buttons are pressed, the unit will cycle through its normal starting or
stopping sequence, both compressors will be stopped and normal dual compressor starting procedure will be in
effect.
2. Remote SWITCH,
Selecting SWITCH in SP3 will put the unit under the control of a remote switch that must be wired
into the control (see Field Wiring Diagram)
Summary of Contents for C10FZXS
Page 16: ...D EIMWC00908 16EN 16 52 Figure 4 Evaporator pressure drop...
Page 17: ...D EIMWC00908 16EN 17 52...
Page 18: ...D EIMWC00908 16EN 18 52 Figure 5 Condenser pressure drop...
Page 34: ...D EIMWC00908 16EN 34 52 Figure 12 Compressor overview...
Page 50: ...D EIMWC00908 16EN 50 52...
Page 51: ...D EIMWC00908 16EN 51 52...