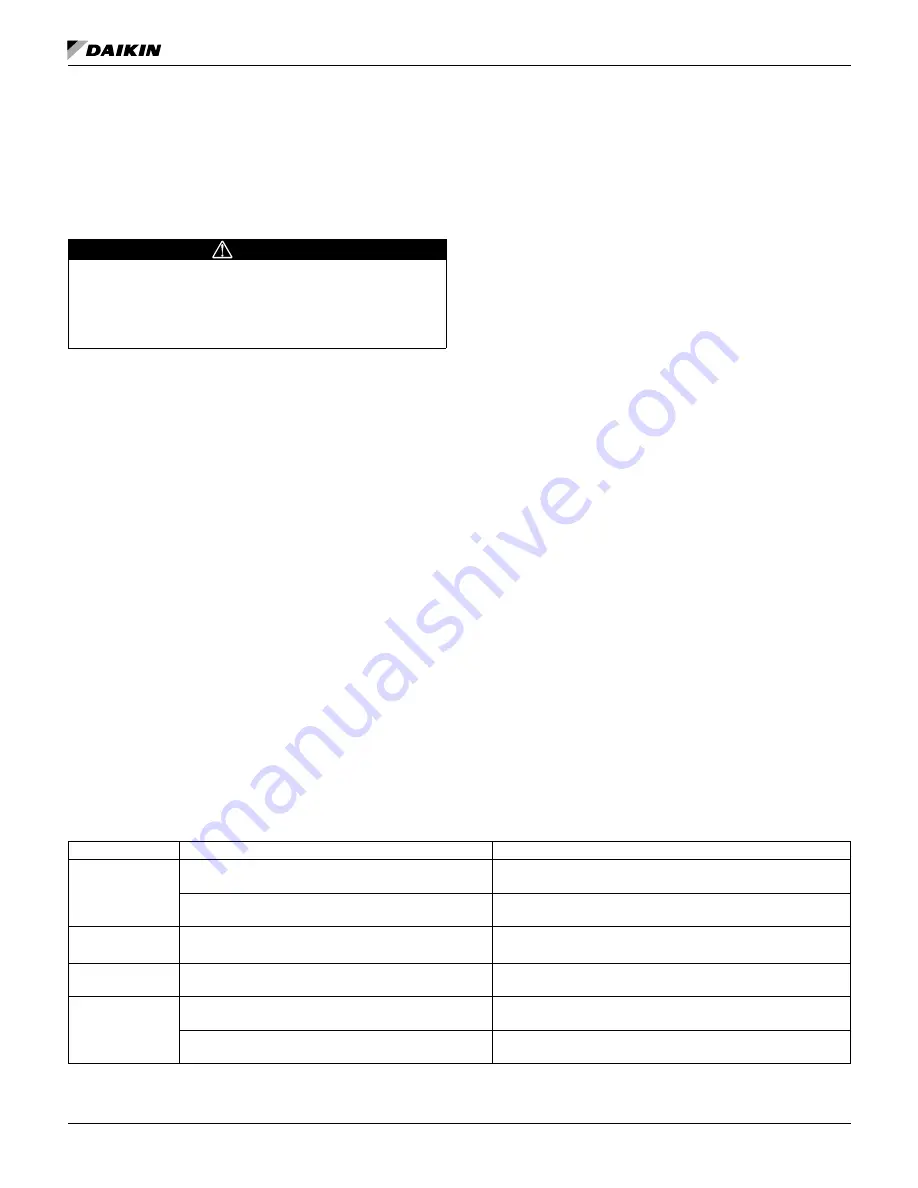
IOM 1242-2 • PATHFINDER
®
MODEL AWV CHILLERS
88 www.DaikinApplied.com
s
ysTem
m
aInTenanCe
Harsh Chemical and Acid Cleaners
Harsh chemicals, household bleach or acid cleaners should
not be used to clean epoxy coated coils. These cleaners can
be very difficult to rinse out of the coil and can accelerate
corrosion and attack the epoxy coating. If there is dirt below
the surface of the coil, use the recommended coil cleaners as
described above.
WARNING
Use caution when applying coil cleaners. They can contain
potentially harmful chemicals. Wear breathing apparatus and
protective clothing. Carefully follow the cleaner manufacturer’s
MSDS sheets. Thoroughly rinse all surfaces to remove any
cleaner residue. Do not damage the fins.
Liquid Line Sight Glass
Observe the refrigerant sight glasses weekly. A clear glass of
liquid indicates that there is adequate refrigerant charge in the
system to provide proper feed through the expansion valve.
Bubbling refrigerant in the sight glass, during stable run
conditions, may indicate that there can be an EXV problem
since the EXV regulates refrigerant flow. Refrigerant gas
flashing in the sight glass could also indicate an excessive
pressure drop in the liquid line, possibly due to a clogged filter-
drier or a restriction elsewhere in the liquid line.
An element inside the sight glass indicates the moisture
condition corresponding to a given element color. If the sight
glass does not indicate a dry condition after about 12 hours of
operation, an oil acid test is recommended.
Do not use the sight glass on the EXV body for refrigerant
charging. Its purpose is to view the position of the valve.
Lead-Lag
A feature on all Daikin Pathfinder
®
air-cooled chillers is a
system for alternating the sequence in which the compressors
start to balance the number of starts and run hours. Lead-
Lag of the refrigerant circuits is accomplished automatically
through the MicroTech
®
III controller. When in the auto mode,
the circuit with the fewest number of starts will be started first.
If all circuits are operating and a stage down in the number of
operating compressors is required, the circuit with the most
operating hours will cycle off first. The operator can override
the MicroTech
®
III controller, and manually select the lead
circuit as circuit #1 or #2.
Pump Operation
It is highly recommended that the chiller unit control the chilled
water pump(s). The integral chiller control system has the
capability to selectively start pump A or B or automatically
alternate pump selection at each start and also has pump
standby operation capability.
Failure to have the chiller control the pumps may cause the
following problems:
1. If any device, other than the chiller, should try to start the
chiller without first starting the pumps, the chiller will lock
out on the No Flow alarm and require a manual reset
to restart. This can be disruptive to the normal cooling
process.
2. In areas where freeze-up is a concern, the chiller control
senses the chilled water temperature and turns on an
immersion heater in the evaporator. It also signals the
chilled water pump to start, providing flow through the
evaporator and additional protection against evaporator
and outside pipe freeze-up. Other pump starting
methods will not automatically provide this protection.
Note:
The owner/operator must be aware that when the
water temperature falls below freezing temperatures it
is imperative NOT to stop the pump(s) as immediate
freeze-up can occur.
This method of freeze protection is only effective as
long as the facility and the chiller have power. The only
positive freeze protection during power failures is to
drain the evaporator and blow out each tube or add the
appropriate concentration of glycol to the system.
Compressor VFD
Table 56: Compressor VFD Inspection Areas
Inspection Area Inspection Points
Corrective Action
General
Inspect equipment for discoloration from
overheating or deterioration.
Replace damaged equipment as required.
Inspect for dirt, foreign particles, or dust collection
on components
Inspect door seal if so equipped. Use dry air to clear
foreign matter.
Conductors and
Wiring
Inspect wiring and connections for discoloration,
damage or heat stress.
Repair or replace damaged wire.
Terminals
Inspect terminals for loose, stripped, or damaged
connections.
Tighten loose screws and replace damaged screws or
terminals.
Relays and
Contactors
Inspect contactors and relays for excessive noise
during operation.
Check coil voltage for over or under voltage condition.
Inspect coils for signs of overheating such as
melted or cracked insulation.
Replace damaged removable relays, contactors or circuit
board.
Summary of Contents for AWV008
Page 4: ......