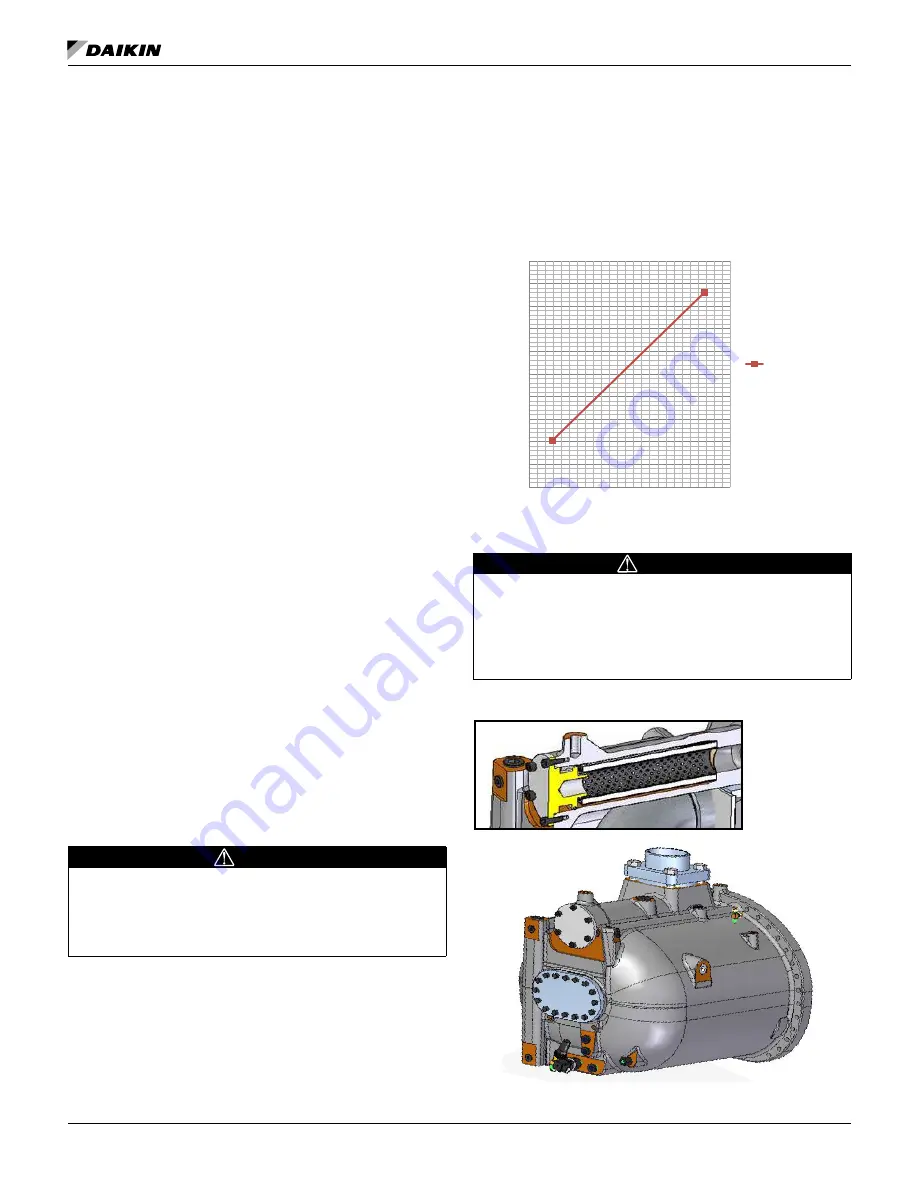
s
ysTem
m
aInTenanCe
www.DaikinApplied.com 85
IOM 1242-2 • PATHFINDER
®
MODEL AWV CHILLERS
s
ysTem
m
aInTenanCe
General
On initial startup and periodically during operation, it will
be necessary to perform certain routine service checks.
Among these are checking the liquid line sight glasses, and
the compressor oil level sight glass. In addition, check the
MicroTech
®
III controller temperature and pressure readings
with gauges and thermometers to see that the unit has normal
condensing/suction pressure and superheat/subcooling
readings.
A Periodic Maintenance Log is located at the end of this
manual. It is suggested that the log be copied and a report be
completed on a regular basis. The log will serve as a useful
tool for a service technician in the event service is required.
Initial startup date, vibration readings, compressor megger
readings and oil analysis information should be kept for
reference baseline data.
If the service technician has determined that the refrigerant
charge has been contaminated, the charge should be
recovered and tested for contaminates or noncondensables.
Appropriate actions should be taken based on testing and
Clean Air Act regulations.
Vibration Monitoring (Optional)
Vibration readings are often used as an indicator of a possible
problem requiring maintenance. If vibration monitoring is part
of the site PM program, the compressor can be checked with a
vibration analyzer on an annual basis. When doing the annual
testing, the load should be maintained as closely as possible
to the load of the original test. The initial vibration analysis test
provides a benchmark of the compressor, and when performed
routinely, can give a warning of impending problems.
Lubrication
The fan motor bearings are permanently lubricated. No further
lubrication is required. Excessive fan motor bearing noise is an
indication of a potential bearing failure.
POE type oil is used for compressor lubrication. This type of
oil is extremely hygroscopic, which means it will quickly absorb
moisture if exposed to air and form acids that can be harmful
to the chiller. Avoid prolonged exposure of refrigerant to the
atmosphere to prevent this problem.
CAUTION
POE oil must be handled carefully using proper protective
equipment (gloves, eye protection, etc.). The oil must not
come into contact with certain polymers (e.g. PVC) as it may
absorb moisture from this material. Also, do not use oil or
refrigerant additives to the system.
It is important that only the manufacturer’s recommended oil be
used. Acceptable POE oil types are:
• CPI/Lubrizol Emkarate RL68H
• Exxon/Mobil EAL Arctic 68
• Hatcol 3693
The compressor oil heater is 250 watts and is on when the
compressor is off and off when the compressor is on.
Oil Filter Removal and Renewal
Prior to this procedure, pump out the compressor. Isolate the
electrical supply to the control panels and compressor motor
terminal. Filter should be changed when pressure drop delta
goes above the linear line in
Figure 74.
Figure 74: Pressure Drop to Change Oil Filter
WARNING
After the compressor has been pumped down and isolated,
the oil contained inside the filter housing will remain hot
enough to cause burns for some time afterwards. Always
allow sufficient time for the oil to cool down so that it is cool
enough not to be a danger when drained off (less than 35°C is
recommended). Severe injury from burns can result.
Figure 75: Oil Filter Location (Including Cutaway View)
y = 0.3846x + 10.596
0
10
20
30
40
50
60
70
80
90
100
0
50
100
150
200
250
O
il
Pre
ss
ure
D
iff
ere
nc
e =
C
on
de
ns
er
Pre
ss
ure
-
O
il
Pr
essu
re
(P
SI
G
)
Operating Pressure Difference = Condenser Pressure -
Evaporator Pressure (PSIG)
Recommended Filter
Delta P Change
Linear (Oil Filter
Pressure Drop)
Summary of Contents for AWV008
Page 4: ......