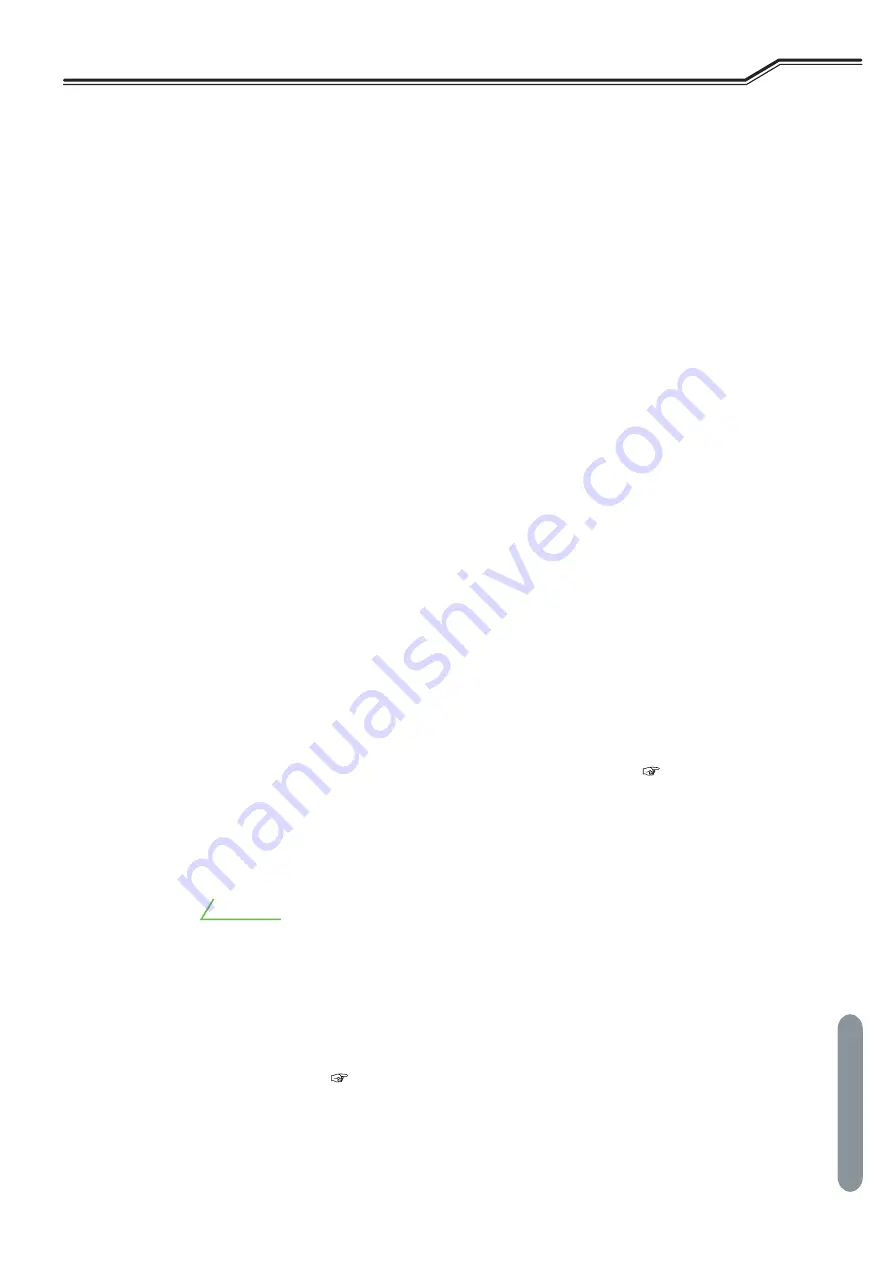
S
ETTING
I
NTERNAL
F
UNCTIONS
W
ELDING
C
ONDITION
C
HAPTER
6
91
Chapter 6
W
elding Condition
6.7.2.14 F16: Slowdown speed adjustment
Slow-down speed is the speed to slowly feed the wire from the time of the machine start to the time of arc start.
The slowdown speed is automatically set to an appropriate speed depending on the welding process and wire diameter;
meanwhile, it can be adjusted through this function if manual setting is preferred.
The setting range is ±1.0 m/min, yet cannot be adjusted slower than 0.4 m/min. Based on "0," adjusting it to the negative
direction lowers the speed, and adjusting it to the positive direction accelerates the speed.
When the starting performance is poor, decrease the slow-down speed to a negative value (which lowers the wire feed
speed).
When the starting performance is not poor, setting the slow-down speed to a positive value (which accelerates the wire
feed speed) can shorten the tact time.
6.7.2.15 F17/F18: Anti-stick time/voltage adjustment
Set the anti-stick time/voltage, which is the anti-stick processing time and voltage. Optimum setting of the anti-stick time/
voltage enables to obtain the following effects:
•
At the welding completion, wire adhesion to the base material can be prevented.
•
The shape of wire tip can be arranged to obtain a stable start of the next welding.
The time and voltage for anti-stick process are automatically set to appropriate conditions depending on the welding
process (wire type) and wire diameter; meanwhile, it can be adjusted through this function if wire should cause adhesion
at the end of welding or if burning is too intense.
•
Adjust the anti-stick process time in the range of ±50 (unit: 0.01 seconds) through the internal function F17. Based on
"0," adjusting it to the negative direction shortens the time, and adjusting it to the positive extends the time.
•
Adjust the anti-stick process voltage in the range of ± 9.9 V through the internal function F18. Based on "0," adjusting
it to the negative values decreases the voltage, and adjusting it to the positive increases the voltage.
6.7.2.16 F19: Alarm setting switching
When alarm occurs, the output of welding power source can be stopped.
Yet for some alarm codes, it is possible to continue welding even if the alarm level is detected, which may sometimes cause
the alarm display to be ignored. Using the alarm setting switch function ensures to stop the output from the welding
power source.
•
[ON]: any alarm detection stops the output of welding power source.
•
[OFF]: alarm detection does not stop the output of welding power source.
Means to reset alarms is the same as those for errors, including restoration of the power. (
-
6.7.2.17 F20: Low input voltage detection level
Set the low input voltage detection level on the primary side. When the input voltage is lower than the set value, an error
code is displayed.
Set the value in the range of 260 to 400 V.
T I P S
• The factory default setting is 320 V. However, the specification of input voltage as welding power
source is the range of 340 to 460 V. If input voltage is lower than this range, it may affect welding
performance.
6.7.2.18 F21: Maximum cooling fan operation
The cooling fan can be rotated at the maximum rotation speed at all time.
•
[ON]: The cooling fan rotates at the maximum rotation speed at all time. Even when it is set to [ON], ensure not to
exceed the specified duty cycle. (
•
[OFF]: The cooling fan rotates in a control mode (power-saving operation) due to the temperature detection inside the
welding power source.
This mode is effective in saving power consumption and preventing suction of extra powder dusts.