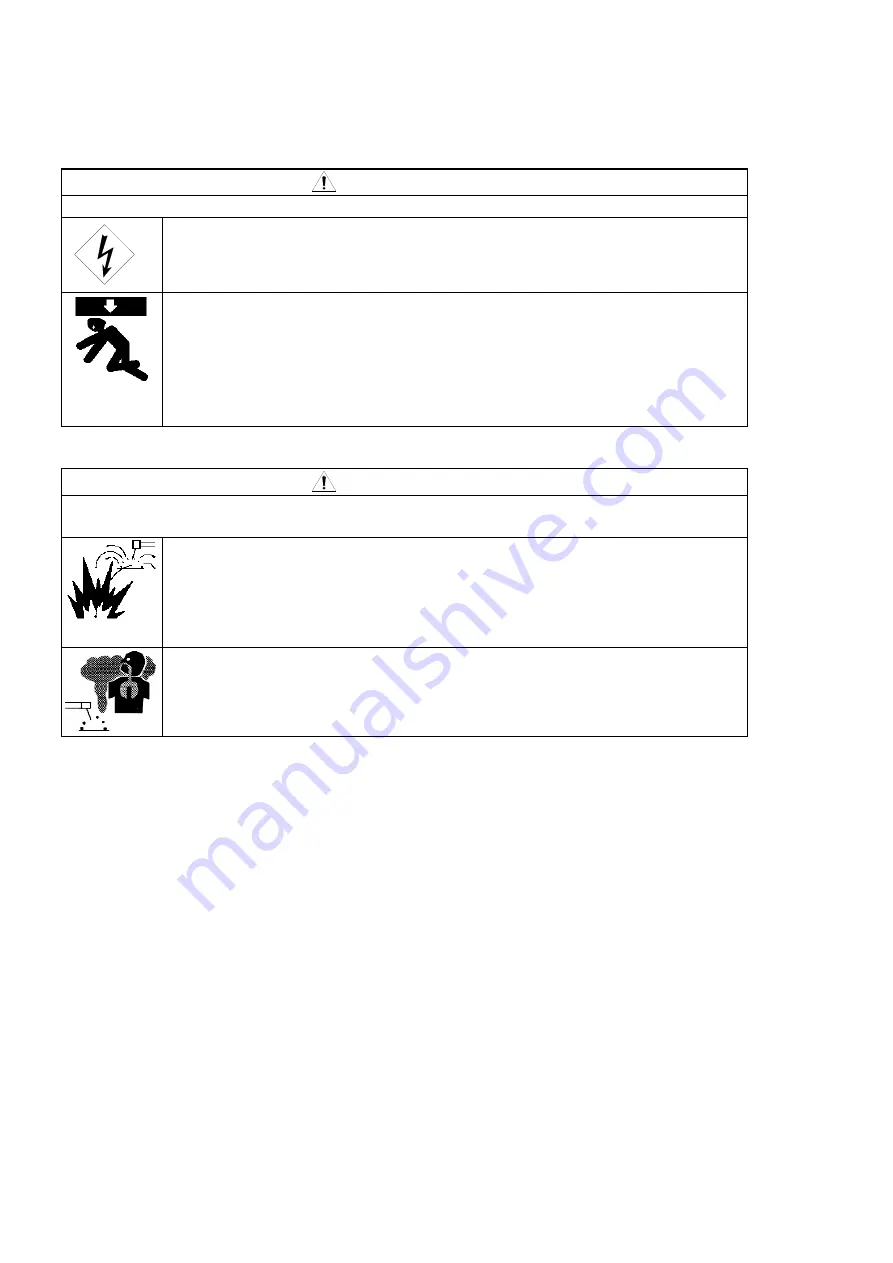
No.P6972
P. 18/ 64
7. TRANSPORTATION AND INSTALLATION
7.1 Transportation
WARNING
Observe the following to prevent damage while transporting the welding machine.
Do not touch live electrical parts inside or outside of the welding machine.
When moving the welding machine, use the line disconnect switch to turn off
the input power.
When lifting the welding power source with a crane, secure the case and the
cover, and firmly tighten the eyebolts
Lift only one welding power source at a time with two wires. Lifting the
welding power source with other equipment may cause it to fall.
When carrying the welding power source with a forklift, secure the wheels to
prevent possible rolling of the power source.
7.2 Installation
WARNING
When installing the welding machine, observe the following to prevent possibility of fires
caused by welding and physical damage caused by fumes and gases.
Do not install the welding machine near combustible materials and
flammable gas.
Remove combustible materials to prevent the possibilities of being struck by
the spatter.
If can not be removed, cover them with a noncombustible cover.
To prevent gas-poisoning or choking, use exhaust equipment or protective
respirators that are prescribed by safety regulations.
To welding in a narrow space, ventilate the space sufficiently or wear
protective respirators, and work only under proper supervision.