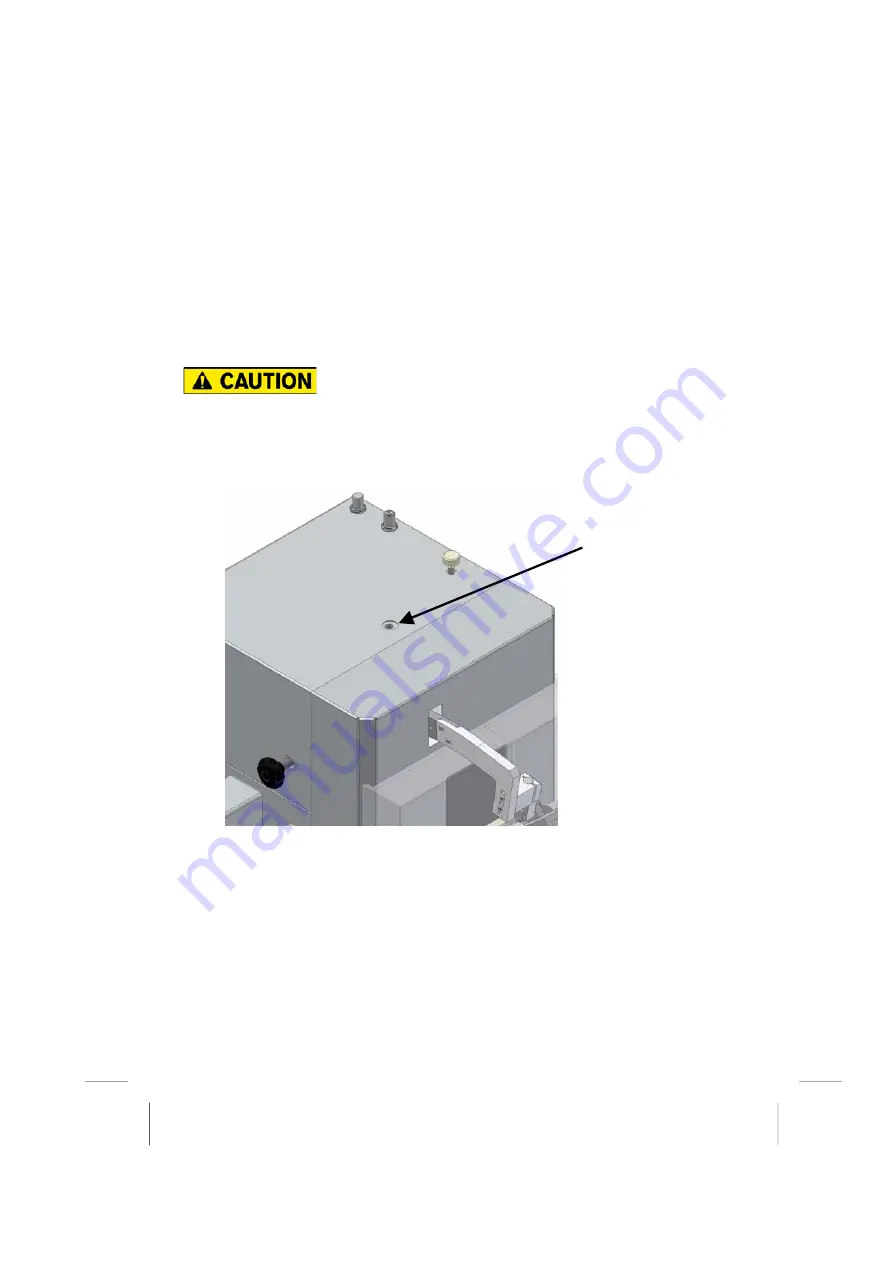
9
2)
Inspect the crate for any damage before unpacking.
3)
Report any damage immediately to both Dage and the carriers.
4)
Remove the spring-metal clips around the top of the crate and remove the lid.
5)
Remove all of the remaining spring-metal clips and remove the sides of the crate.
6)
Unpack all of the accessories to the machine and move to a location, leaving enough
room to move the machine about.
ENSURE THE LIFTING EYE IS SECURELY FIITED
PRIOR TO LIFTING
7)
Using the Lifting eye supplied with the machine and a suitable lifting hoist lift the
machine and place on the work bench as outlined in section
3.1.1 in the
Operators
Guide.
The lifting eye is fixed to the top of the machine.
3.1.1
Workbench
It should be of sturdy construction, rigid and free from vibration
It should be sufficiently high to allow the largest operator to sit under comfortably.
Its maximum thickness, at the operator position, should not exceed 60mm.
Its legs or supports should not obstruct the operator.
Lifting eye fits here