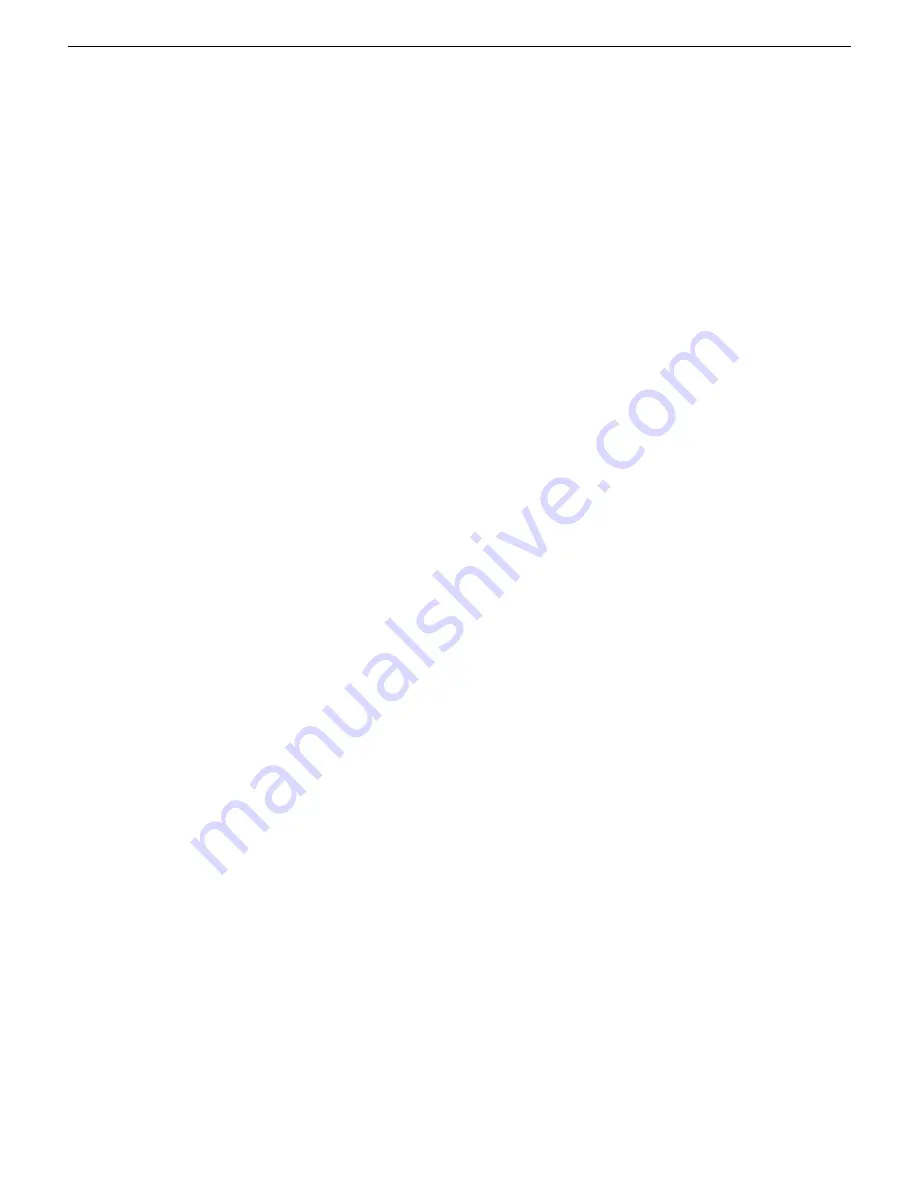
ENGINE CONTROLS 1F – 405
DAEWOO V–121 BL4
ciently. Because of the constant measuring and adjusting
of the air/fuel ratio, the fuel injection system is called a
”closed loop” system.
The PCM/ECM uses voltage inputs from several sensors
to determine how much fuel to provide to the engine. The
fuel is delivered under one of several conditions, called
”modes.”
Starting Mode
When the ignition is turned ON, the PCM/ECM turns the
fuel pump relay on for two seconds. The fuel pump then
builds fuel pressure. The PCM/ECM also checks the En-
gine Coolant Temperature (ECT) sensor and the Throttle
Position (TP) sensor and determines the proper air/fuel ra-
tio for starting the engine. This ranges from 1.5 to 1 at
–97
³
F (–36
³
C) coolant temperature to 14.7 to 1 at 201
³
F
(94
³
C) coolant temperature. The PCM/ECM controls the
amount of fuel delivered in the starting mode by changing
how long the fuel injector is turned on and off. This is done
by ”pulsing” the fuel injectors for very short times.
Clear Flood Mode
If the engine floods with excessive fuel, it may be cleared
by pushing the accelerator pedal down all the way. The
PCM/ECM will then completely turn off the fuel by eliminat-
ing any fuel injector signal. The PCM/ECM holds this injec-
tor rate as long as the throttle stays wide open and the en-
gine is below approximately 400. If the throttle position
becomes less than approximately 80 percent, the PCM/
ECM returns to the starting mode.
Run Mode
The run mode has two conditions called ”open loop” and
”closed loop.”
Open Loop
When the engine is first started and it is above 400 rpm,
the system goes into ”open loop” operation. In ”open loop,”
the PCM/ECM ignores the signal from the O2S and calcu-
lates the air/fuel ratio based on inputs from the ECT sensor
and the MAP sensor. The sensor stays in ”open loop” until
the following conditions are met:
S
The O2S sensor has a varying voltage output,
showing that it is hot enough to operate properly.
S
The ECT sensor is above a specified temperature.
S
A specific amount of time has elapsed after starting
the engine.
Closed Loop
The specific values for the above conditions vary with dif-
ferent engines and are stored in the Electronically Eras-
able Programmable Read–Only Memory (EEPROM).
When these conditions are met, the system goes into
”closed loop” operation. In ”closed loop,” the PCM/ECM
calculates the air/fuel ratio (fuel injector ontime) based on
the signal from the oxygen sensor. This allows the air/fuel
ratio to stay very close to 14.7 to 1.
Acceleration Mode
The PCM/ECM responds to rapid changes in throttle posi-
tion and airflow and provides extra fuel.
Deceleration Mode
The PCM/ECM responds to changes in throttle position
and airflow and reduces the amount of fuel. When decel-
eration is very fast, the PCM/ECM can cut off fuel com-
pletely for short periods of time.
Battery Voltage Correction Mode
When battery voltage is low, the PCM/ECM can compen-
sate for a weak spark delivered by the ignition module by
using the following methods:
S
Increasing the fuel injector pulse width.
S
Increasing the idle speed rpm.
S
Increasing the ignition dwell time.
Fuel Cut–Off Mode
No fuel is delivered by the fuel injectors when the ignition
is OFF. This prevents dieseling or engine run–on. Also, the
fuel is not delivered if there are no reference pulses re-
ceived from the central power supply. This prevents flood-
ing.
EVAPORATIVE EMISSION CONTROL
SYSTEM OPERATION
The basic Evaporative (EVAP) Emission control system
used is the charcoal canister storage method. This meth-
od transfers fuel vapor from the fuel tank to an activated
carbon (charcoal) storage device (canister) to hold the va-
pors when the vehicle is not operating. When the engine
is running, the fuel vapor is purged from the carbon ele-
ment by intake airflow and consumed in the normal com-
bustion process.
Gasoline vapors from the fuel tank flow into the tube la-
beled TANK. These vapors are absorbed into the carbon.
The canister is purged by the powertrain control module
(PCM)/engine control module (ECM) when the engine has
been running for a specified amount of time. Air is drawn
into the canister and mixed with the vapor. This mixture is
then drawn into the intake manifold.
The PCM/ECM supplies a ground to energize the EVAP
emission canister purge solenoid valve. This valve is Pul-
seWidth Modulated (PWM) or turned on and off several
times a second. The EVAP emission canister purge PWM
duty cycle varies according to operating conditions deter-
mined by mass airflow, fuel trim, and intake air tempera-
ture.
Poor idle, stalling, and poor driveability can be caused by
the following conditions:
S
An inoperative EVAP emission canister purge sole-
noid valve.
S
A damaged canister.
S
Hoses that are split, cracked, or not connected to
the proper tubes.
Summary of Contents for NUBIRA
Page 1: ......
Page 29: ...WIPERS WASHER SYSTEMS 9D 3 DAEWOO V 121 BL4 WIPERS AND WASHER SYSTEM HATCHBACK...
Page 58: ...DOORS 9P 3 DAEWOO V 121 BL4 SCHEMATIC AND ROUTING DIAGRAMS POWER DOOR LOCKS...
Page 59: ...9P 4IDOORS DAEWOO V 121 BL4 POWER WINDOWS FRONT AND REAR...
Page 92: ...9Q 2IROOF DAEWOO V 121 BL4 SCHEMATIC AND ROUTING DIAGRAMS POWER SUNROOF SYSTEM...
Page 229: ...ANTILOCK BRAKE SYSTEM 4F 5 DAEWOO V 121 BL4 SCHEMATIC AND ROUTING DIAGRAMS ABS CIRCUIT 1 OF 4...
Page 230: ...4F 6IANTILOCK BRAKE SYSTEM DAEWOO V 121 BL4 ABS CIRCUIT 2 OF 4...
Page 231: ...ANTILOCK BRAKE SYSTEM 4F 7 DAEWOO V 121 BL4 ABS CIRCUIT 3 OF 4...
Page 232: ...4F 8IANTILOCK BRAKE SYSTEM DAEWOO V 121 BL4 ABS CIRCUIT 4 OF 4...
Page 252: ...5C0 6ICLUTCH DAEWOO V 121 BL4 1 Flywheel 2 Clutch Disc 3 Pressure Plate 4 Release Bearing...
Page 272: ...SECTION 2 POSITION OF CONNECTORS AND GROUNDS...
Page 276: ...POSITION OF CONNECTORS AND GROUNDSW2 5 2 ENGINE CONTROL BATTERY S 2 0 DOHC ENGINE...
Page 277: ...2 6WPOSITION OF CONNECTORS AND GROUNDS 3 INSTRUMENT PANEL INSIDE...
Page 278: ...POSITION OF CONNECTORS AND GROUNDSW2 7 4 AIR BAG INSTRUMENT PANEL 5 BODY...
Page 279: ...2 8WPOSITION OF CONNECTORS AND GROUNDS 6 W H DOOR 1 Front Door 2 Rear Door...
Page 281: ...2 10WPOSITION OF CONNECTORS AND GROUNDS 8 ABS MODULE WHEEL SPEED SENSOR...
Page 282: ...POSITION OF CONNECTORS AND GROUNDSW2 11 9 REAR 10 FUEL TANK TRUNK LID...
Page 285: ...2 14WPOSITION OF CONNECTORS AND GROUNDS S303 BLACK N B H B S303 BLACK S W...
Page 286: ...SECTION 3 WIRING DIAGRAM FOR POWER SUPPLIES...
Page 287: ...3 2WWIRING DIAGRAM FOR POWER SUPPLIES 1 IGNITION SWITCH CIRCUIT...
Page 290: ...WIRING DIAGRAM FOR POWER SUPPLIESW3 5 4 ENGINE ROOM FUSE RELAY CIRCUIT...
Page 291: ...3 6WWIRING DIAGRAM FOR POWER SUPPLIES...
Page 292: ...WIRING DIAGRAM FOR POWER SUPPLIESW3 7...
Page 293: ...SECTION 4 USAGE AND CAPACITY OF FUSES...
Page 297: ...SECTION 5 ELECTRICAL WIRING DIAGRAMS...
Page 301: ...9A 2IBODY WIRING SYSTEM DAEWOO V 121 BL4 POWER DISTRIBUTION SCHEMATIC...
Page 302: ...BODY WIRING SYSTEM 9A 3 DAEWOO V 121 BL4...
Page 306: ...BODY WIRING SYSTEM 9A 7 DAEWOO V 121 BL4 REAR HARNESS ROUTING...
Page 307: ...9A 8IBODY WIRING SYSTEM DAEWOO V 121 BL4 FRONT HARNESS ROUTING...
Page 308: ...BODY WIRING SYSTEM 9A 9 DAEWOO V 121 BL4 FLOOR HARNESS ROUTING...
Page 309: ...9A 10IBODY WIRING SYSTEM DAEWOO V 121 BL4 INSTRUMENT HARNESS ROUTING...
Page 310: ...BODY WIRING SYSTEM 9A 11 DAEWOO V 121 BL4 DOOR HARNESS ROUTING...
Page 314: ...9B 4ILIGHTING SYSTEMS DAEWOO V 121 BL4 PARKING TAIL POSITION AND LICENSE LAMPS CIRCUIT...
Page 315: ...LIGHTING SYSTEMS 9B 5 DAEWOO V 121 BL4 TURN AND HAZARD LAMPS CIRCUIT...
Page 316: ...9B 6ILIGHTING SYSTEMS DAEWOO V 121 BL4 BRAKE AND BACKUP LAMPS CIRCUIT...
Page 318: ...9B 8ILIGHTING SYSTEMS DAEWOO V 121 BL4 HEADLAMPS CIRCUIT...
Page 319: ...LIGHTING SYSTEMS 9B 9 DAEWOO V 121 BL4 DAYTIME RUNNING LAMPS CIRCUIT...
Page 320: ...9B 10ILIGHTING SYSTEMS DAEWOO V 121 BL4 FOG LAMPS CIRCUIT...
Page 342: ...9C 2IHORNS DAEWOO V 121 BL4 SCHEMATIC AND ROUTING DIAGRAMS HORN WIRING SYSTEM...
Page 347: ...9F 2IAUDIO SYSTEMS DAEWOO V 121 BL4 SCHEMATIC AND ROUTING DIAGRAMS AUDIO SYSTEM CIRCUIT...
Page 365: ...CRUISE CONRTOL SYSTEM 9U 3 DAEWOO V 121 BL4 CRUISE CONTROL SYSTEM AUTOMATIC TRANSAXLE 2 OF 2...
Page 366: ...9U 4ICRUISE CONRTOL SYSTEM DAEWOO V 121 BL4 CRUISE CONTROL SYSTEM MANUAL TRANSAXLE 1 OF 2...
Page 367: ...CRUISE CONRTOL SYSTEM 9U 5 DAEWOO V 121 BL4 CRUISE CONTROL SYSTEM MANUAL TRANSAXLE 2 OF 2...
Page 407: ...GENERAL INFORMATION 0B 25 DAEWOO V 121 BL4...
Page 408: ...0B 26IGENERAL INFORMATION DAEWOO V 121 BL4 Vehicle Lifting Points...
Page 427: ...1C 8IDOHC ENGINE MECHANICAL DAEWOO V 121 BL4 COMPONENT LOCATOR UPPER END...
Page 429: ...1C 10IDOHC ENGINE MECHANICAL DAEWOO V 121 BL4 LOWER END...
Page 521: ...1F 16IENGINE CONTROLS DAEWOO V 121 BL4 PCM ECM WIRING DIAGRAM 2 OF 6 IPCM 6KD ISFI 6TD...
Page 522: ...ENGINE CONTROLS 1F 17 DAEWOO V 121 BL4 PCM ECM WIRING DIAGRAM 3 OF 6 IPCM 6KD ISFI 6TD...
Page 523: ...1F 18IENGINE CONTROLS DAEWOO V 121 BL4 PCM ECM WIRING DIAGRAM 4 OF 6 IPCM 6KD ISFI 6TD...
Page 524: ...ENGINE CONTROLS 1F 19 DAEWOO V 121 BL4 PCM ECM WIRING DIAGRAM 5 OF 6 IPCM 6KD ISFI 6TD...
Page 525: ...1F 20IENGINE CONTROLS DAEWOO V 121 BL4 PCM ECM WIRING DIAGRAM 6 OF 6 IPCM 6KD ISFI 6TD...
Page 526: ...ENGINE CONTROLS 1F 21 DAEWOO V 121 BL4 CONNECTOR END VIEW...
Page 527: ...1F 22IENGINE CONTROLS DAEWOO V 121 BL4...
Page 528: ...ENGINE CONTROLS 1F 23 DAEWOO V 121 BL4...
Page 529: ...1F 24IENGINE CONTROLS DAEWOO V 121 BL4...
Page 530: ...ENGINE CONTROLS 1F 25 DAEWOO V 121 BL4...
Page 531: ...1F 26IENGINE CONTROLS DAEWOO V 121 BL4 COMPONENT LOCATOR...
Page 541: ...1F 36IENGINE CONTROLS DAEWOO V 121 BL4...
Page 632: ......
Page 633: ......
Page 670: ...5A 16I4T40 E AUTOMATIC TRANSAXLE DAEWOO V 121 BL4 POWERTRAIN CONTROL MODULE 2 OF 3...
Page 671: ...4T40 E AUTOMATIC TRANSAXLE 5A 17 DAEWOO V 121 BL4 POWERTRAIN CONTROL MODULE 3 OF 3...
Page 681: ...FIVE SPEED MANUAL TRANSAXLE 5B 9 DAEWOO V 121 BL4 COMPONENT LOCATORS GEARS AND CASE...
Page 684: ...5B 12IFIVE SPEED MANUAL TRANSAXLE DAEWOO V 121 BL4 SHIFT LINKAGE...