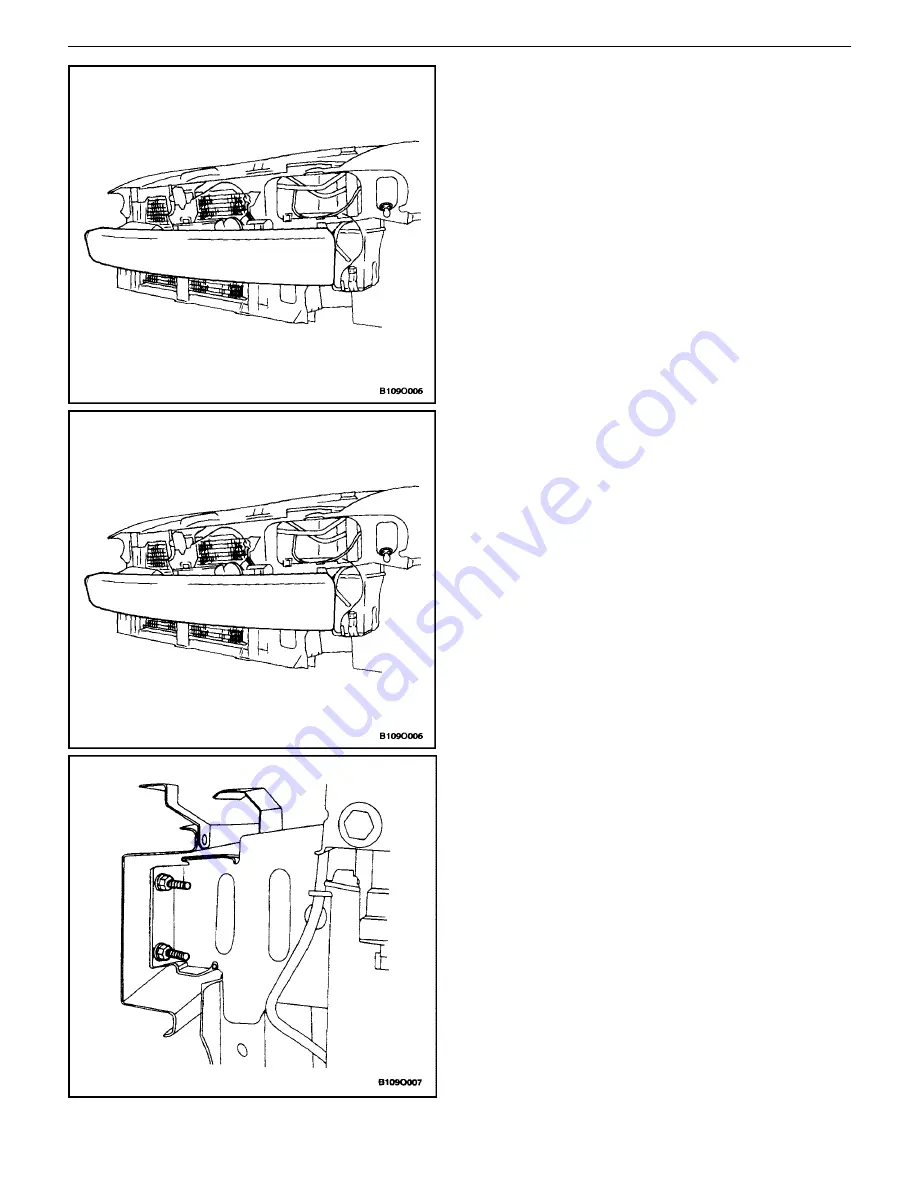
9O – 6
I
BUMPERS AND FASCIAS
DAEWOO V–121 BL4
FRONT BUMPER ENERGY
ABSORBER
Removal Procedure
1. Remove the front bumper fascia. Refer to”Front
Bumper Fascia” in this section.
2. Remove the energy absorber.
Installation Procedure
1. Install the energy absorber.
2. Install the front bumper fascia. Refer to”Front
Bumper Fascia” in this section.
FRONT BUMPER IMPACT BAR
Removal Procedure
1. Remove the front bumper fascia. Refer to”Front
Bumper Fascia” in this section.
2. Remove the front bumper energy absorber. Refer
to”Front Bumper Energy Absorber” in this section.
3. Remove the front bumper impact bar nuts.
Summary of Contents for NUBIRA
Page 1: ......
Page 29: ...WIPERS WASHER SYSTEMS 9D 3 DAEWOO V 121 BL4 WIPERS AND WASHER SYSTEM HATCHBACK...
Page 58: ...DOORS 9P 3 DAEWOO V 121 BL4 SCHEMATIC AND ROUTING DIAGRAMS POWER DOOR LOCKS...
Page 59: ...9P 4IDOORS DAEWOO V 121 BL4 POWER WINDOWS FRONT AND REAR...
Page 92: ...9Q 2IROOF DAEWOO V 121 BL4 SCHEMATIC AND ROUTING DIAGRAMS POWER SUNROOF SYSTEM...
Page 229: ...ANTILOCK BRAKE SYSTEM 4F 5 DAEWOO V 121 BL4 SCHEMATIC AND ROUTING DIAGRAMS ABS CIRCUIT 1 OF 4...
Page 230: ...4F 6IANTILOCK BRAKE SYSTEM DAEWOO V 121 BL4 ABS CIRCUIT 2 OF 4...
Page 231: ...ANTILOCK BRAKE SYSTEM 4F 7 DAEWOO V 121 BL4 ABS CIRCUIT 3 OF 4...
Page 232: ...4F 8IANTILOCK BRAKE SYSTEM DAEWOO V 121 BL4 ABS CIRCUIT 4 OF 4...
Page 252: ...5C0 6ICLUTCH DAEWOO V 121 BL4 1 Flywheel 2 Clutch Disc 3 Pressure Plate 4 Release Bearing...
Page 272: ...SECTION 2 POSITION OF CONNECTORS AND GROUNDS...
Page 276: ...POSITION OF CONNECTORS AND GROUNDSW2 5 2 ENGINE CONTROL BATTERY S 2 0 DOHC ENGINE...
Page 277: ...2 6WPOSITION OF CONNECTORS AND GROUNDS 3 INSTRUMENT PANEL INSIDE...
Page 278: ...POSITION OF CONNECTORS AND GROUNDSW2 7 4 AIR BAG INSTRUMENT PANEL 5 BODY...
Page 279: ...2 8WPOSITION OF CONNECTORS AND GROUNDS 6 W H DOOR 1 Front Door 2 Rear Door...
Page 281: ...2 10WPOSITION OF CONNECTORS AND GROUNDS 8 ABS MODULE WHEEL SPEED SENSOR...
Page 282: ...POSITION OF CONNECTORS AND GROUNDSW2 11 9 REAR 10 FUEL TANK TRUNK LID...
Page 285: ...2 14WPOSITION OF CONNECTORS AND GROUNDS S303 BLACK N B H B S303 BLACK S W...
Page 286: ...SECTION 3 WIRING DIAGRAM FOR POWER SUPPLIES...
Page 287: ...3 2WWIRING DIAGRAM FOR POWER SUPPLIES 1 IGNITION SWITCH CIRCUIT...
Page 290: ...WIRING DIAGRAM FOR POWER SUPPLIESW3 5 4 ENGINE ROOM FUSE RELAY CIRCUIT...
Page 291: ...3 6WWIRING DIAGRAM FOR POWER SUPPLIES...
Page 292: ...WIRING DIAGRAM FOR POWER SUPPLIESW3 7...
Page 293: ...SECTION 4 USAGE AND CAPACITY OF FUSES...
Page 297: ...SECTION 5 ELECTRICAL WIRING DIAGRAMS...
Page 301: ...9A 2IBODY WIRING SYSTEM DAEWOO V 121 BL4 POWER DISTRIBUTION SCHEMATIC...
Page 302: ...BODY WIRING SYSTEM 9A 3 DAEWOO V 121 BL4...
Page 306: ...BODY WIRING SYSTEM 9A 7 DAEWOO V 121 BL4 REAR HARNESS ROUTING...
Page 307: ...9A 8IBODY WIRING SYSTEM DAEWOO V 121 BL4 FRONT HARNESS ROUTING...
Page 308: ...BODY WIRING SYSTEM 9A 9 DAEWOO V 121 BL4 FLOOR HARNESS ROUTING...
Page 309: ...9A 10IBODY WIRING SYSTEM DAEWOO V 121 BL4 INSTRUMENT HARNESS ROUTING...
Page 310: ...BODY WIRING SYSTEM 9A 11 DAEWOO V 121 BL4 DOOR HARNESS ROUTING...
Page 314: ...9B 4ILIGHTING SYSTEMS DAEWOO V 121 BL4 PARKING TAIL POSITION AND LICENSE LAMPS CIRCUIT...
Page 315: ...LIGHTING SYSTEMS 9B 5 DAEWOO V 121 BL4 TURN AND HAZARD LAMPS CIRCUIT...
Page 316: ...9B 6ILIGHTING SYSTEMS DAEWOO V 121 BL4 BRAKE AND BACKUP LAMPS CIRCUIT...
Page 318: ...9B 8ILIGHTING SYSTEMS DAEWOO V 121 BL4 HEADLAMPS CIRCUIT...
Page 319: ...LIGHTING SYSTEMS 9B 9 DAEWOO V 121 BL4 DAYTIME RUNNING LAMPS CIRCUIT...
Page 320: ...9B 10ILIGHTING SYSTEMS DAEWOO V 121 BL4 FOG LAMPS CIRCUIT...
Page 342: ...9C 2IHORNS DAEWOO V 121 BL4 SCHEMATIC AND ROUTING DIAGRAMS HORN WIRING SYSTEM...
Page 347: ...9F 2IAUDIO SYSTEMS DAEWOO V 121 BL4 SCHEMATIC AND ROUTING DIAGRAMS AUDIO SYSTEM CIRCUIT...
Page 365: ...CRUISE CONRTOL SYSTEM 9U 3 DAEWOO V 121 BL4 CRUISE CONTROL SYSTEM AUTOMATIC TRANSAXLE 2 OF 2...
Page 366: ...9U 4ICRUISE CONRTOL SYSTEM DAEWOO V 121 BL4 CRUISE CONTROL SYSTEM MANUAL TRANSAXLE 1 OF 2...
Page 367: ...CRUISE CONRTOL SYSTEM 9U 5 DAEWOO V 121 BL4 CRUISE CONTROL SYSTEM MANUAL TRANSAXLE 2 OF 2...
Page 407: ...GENERAL INFORMATION 0B 25 DAEWOO V 121 BL4...
Page 408: ...0B 26IGENERAL INFORMATION DAEWOO V 121 BL4 Vehicle Lifting Points...
Page 427: ...1C 8IDOHC ENGINE MECHANICAL DAEWOO V 121 BL4 COMPONENT LOCATOR UPPER END...
Page 429: ...1C 10IDOHC ENGINE MECHANICAL DAEWOO V 121 BL4 LOWER END...
Page 521: ...1F 16IENGINE CONTROLS DAEWOO V 121 BL4 PCM ECM WIRING DIAGRAM 2 OF 6 IPCM 6KD ISFI 6TD...
Page 522: ...ENGINE CONTROLS 1F 17 DAEWOO V 121 BL4 PCM ECM WIRING DIAGRAM 3 OF 6 IPCM 6KD ISFI 6TD...
Page 523: ...1F 18IENGINE CONTROLS DAEWOO V 121 BL4 PCM ECM WIRING DIAGRAM 4 OF 6 IPCM 6KD ISFI 6TD...
Page 524: ...ENGINE CONTROLS 1F 19 DAEWOO V 121 BL4 PCM ECM WIRING DIAGRAM 5 OF 6 IPCM 6KD ISFI 6TD...
Page 525: ...1F 20IENGINE CONTROLS DAEWOO V 121 BL4 PCM ECM WIRING DIAGRAM 6 OF 6 IPCM 6KD ISFI 6TD...
Page 526: ...ENGINE CONTROLS 1F 21 DAEWOO V 121 BL4 CONNECTOR END VIEW...
Page 527: ...1F 22IENGINE CONTROLS DAEWOO V 121 BL4...
Page 528: ...ENGINE CONTROLS 1F 23 DAEWOO V 121 BL4...
Page 529: ...1F 24IENGINE CONTROLS DAEWOO V 121 BL4...
Page 530: ...ENGINE CONTROLS 1F 25 DAEWOO V 121 BL4...
Page 531: ...1F 26IENGINE CONTROLS DAEWOO V 121 BL4 COMPONENT LOCATOR...
Page 541: ...1F 36IENGINE CONTROLS DAEWOO V 121 BL4...
Page 632: ......
Page 633: ......
Page 670: ...5A 16I4T40 E AUTOMATIC TRANSAXLE DAEWOO V 121 BL4 POWERTRAIN CONTROL MODULE 2 OF 3...
Page 671: ...4T40 E AUTOMATIC TRANSAXLE 5A 17 DAEWOO V 121 BL4 POWERTRAIN CONTROL MODULE 3 OF 3...
Page 681: ...FIVE SPEED MANUAL TRANSAXLE 5B 9 DAEWOO V 121 BL4 COMPONENT LOCATORS GEARS AND CASE...
Page 684: ...5B 12IFIVE SPEED MANUAL TRANSAXLE DAEWOO V 121 BL4 SHIFT LINKAGE...