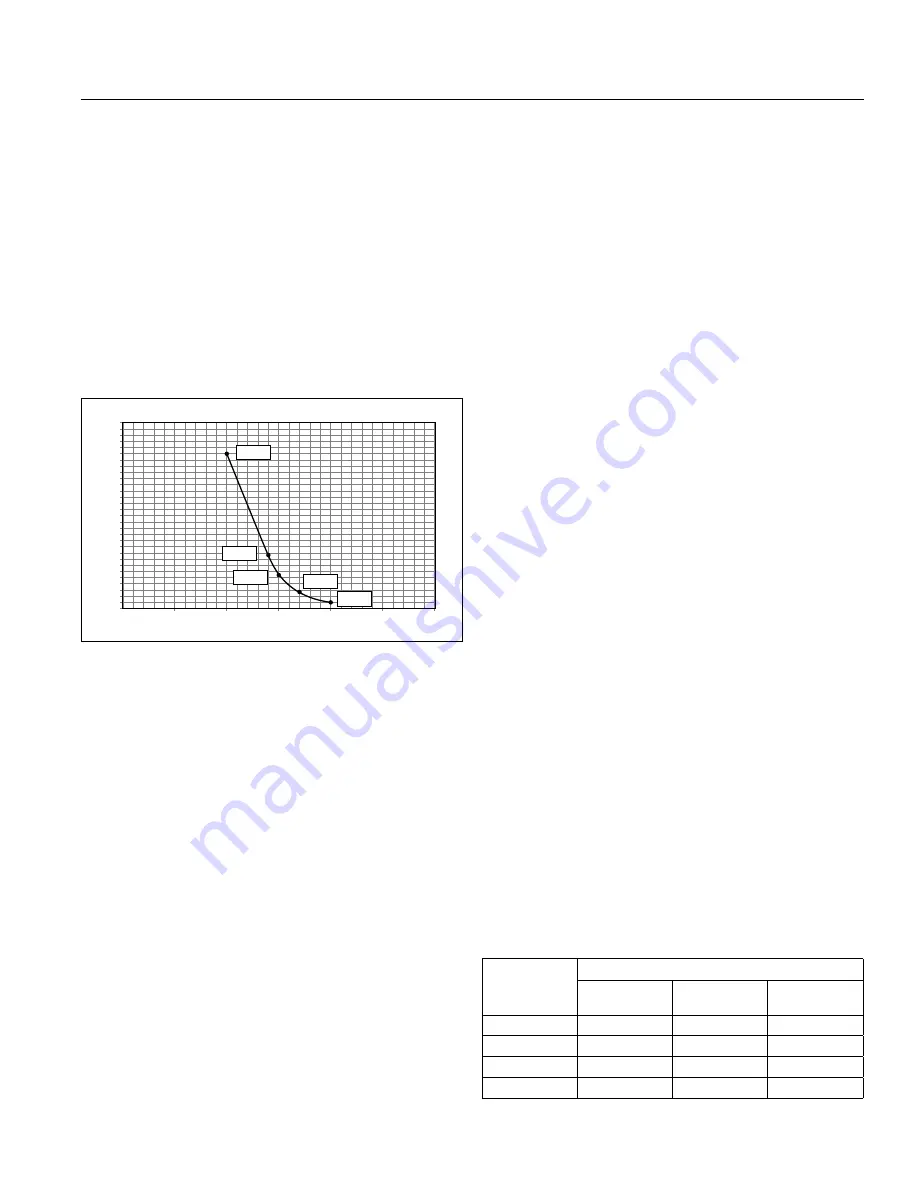
GTX Series Actuator Installation & Maintenance Instructions |
13
www.exlar.com
| 952.500.6200
11. Create an index program to cycle the actuator in both the
extend and retract directions at rated speed.
12. Set acceleration to 10 times the rated actuator speed.
13.
If the actuator cycles without any amplifier error messages
or abnormal behavior, couple the actuator to the load and
begin commissioning the overall system.
NOTES:
• GTX Series actuators can be operated at current levels
two times the current rating for short amounts of time.
• When operating the actuator in the peak current range,
follow the duty cycle limits shown in Figure 10.
120
100
80
60
40
20
0
0 0.5 1.0 1.5 2.0 2.5 3.0
Normalized Continuous Current (Motor)
% Duty Cycle
Duty Cycle
100.00
34.00
22.00
10.00
4.00
Figure 10 –
Duty cycle for peak current operation
6.0 MAINTENANCE PROCEDURES
6.1 LUBRICATION
GTX Series actuators lubricated with grease require periodic
inspection and renewal of the bearing and roller screw grease
to maximize actuator life. Maintenance indicators during a
physical inspection include:
• Contamination of grease with foreign matter
• Leaking seals
• “Burnt” smell of the grease
• Grease is gritty in appearance
• Grease is dehydrated (dried out)
Although application-specific performance makes it difficult to
provide an exact number of hours of operation before main-
tenance is required, the following factors will help determine
lubrication maintenance cycles.
Temperature
– Temperature is the most significant factor
affecting grease life. Exlar’s testing of Mobil SHC 220 syn
-
thetic grease indicates ideal performance operation in ambient
temperature ranging from 32° C to 55° C (90° F to 130° F).
Within this temperature range, the grease has a long service
life. Operation In temperatures above this range decreases the
effective grease life. For every temperature rise of 15° C (60° F),
grease life is reduced by approximately 50%.
Speed
– The rotational speed of the actuator will generate heat
(thus raising the grease temperature) and potentially resulting in
lubricant being thrown off the roller screw.
Load
– Load contributes to the stress applied to the roller
screw mechanism and the pressure applied to the grease thus
impacting the overall lubricant life and relubrication interval.
Load directly impacts the amount of power put into the actuator
adding to the heat generated by roller screw speed. This heat is
transmitted to the lubricant eventually separating the oils from
the thickener and reducing grease life.
Orientation
– Gravity can cause grease migration over time,
especially in vertical applications at elevated temperatures.
Figure 11 provides a general guideline for recommended lubri-
cation renewal cycles.
RMS
Rotational
Speed (RPM)
Recommended Grease Renewal Period (hours)
Case Temp.
65° C (149° F)
Case Temp.
80° C (176° F)
Case Temp.
95° C (203° F)
250
10,000
5,000
2,500
500
8,500
4,250
2,125
1000
6,000
3,000
1,500
1500+
3,500
1,750
875
Figure 11 –
Recommended lubrication renewal cycles