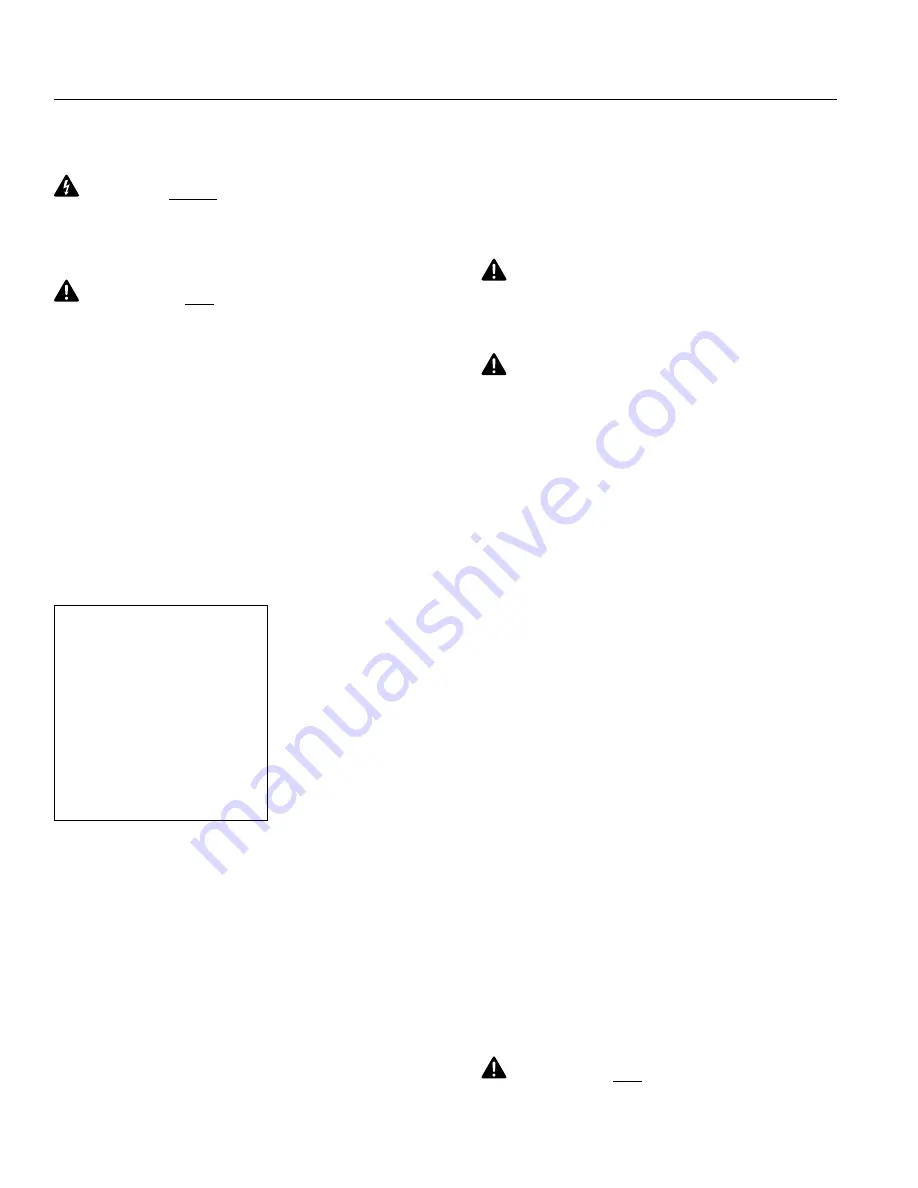
12
| GTX Series Actuator Installation & Maintenance Instructions
Curtiss-Wright | Rev D | PN75557 | 10/01/2019
5.0 STARTUP
5.1 CONSIDERATIONS FOR STARTUP
5.1.1 Safety Considerations
WARNING!
NEVER attempt to connect or disconnect
the actuator with power applied. Many amplifiers have voltage
present after incoming power is removed. Ensure that the am-
plifier has discharged all power.
CAUTION!
Do NOT exceed the maximum input voltage
for GTX Series actuators (460 Vac).
5.1.2 Amplifier Software
Many amplifiers offer software that allows the user to enter the
above parameters or download “motor data files” that dictate how
the feedback must be set up on the motor. There parameters are
available in the GTX Series Actuator catalog or on the Exlar web-
site.
NOTE
: Entering motor parameter data to some amplifiers
may require assistance from the amplifier manufacturer.
5.1.3 Rotary-to-Linear Motion Relationship
The relationship between the rotary motion of the motor
and the linear motion of the actuator is based on the
following parameters:
L
D
= Rev x R
L
S
= [RPM/60] x R
L
F
= [T x (2p x E/R)]
where:
E = Efficiency
L
D
= Linear distance traveled
L
S
= Linear speed
L
F
= Linear force
R = Roller screw lead
REV = Motor revolutions
RPM = Motor revolutions per minute
T = Motor torque
NOTE:
Each of the above relationships requires proper anti-
rotation of the actuator rod.
5.1.4 Amplifier Wiring
Each brand of brushless motor amplifiers may have unique
wiring requirements, parameter settings, and operational princi-
ples that affect how the actuator operates. For more information
on sizing and selecting GTX Series actuators and the brushless
servo motor amplifiers used to power them, consult the sizing
and selection section of the GTX Series actuator catalog.
5.2 GENERAL STARTUP PROCEDURE
IMPORTANT!
Exlar recommends testing new systems prior to
live operation (see example startup procedure below).
1.
Connect wiring or cables from the amplifier to the actuator
using cables supplied by the drive manufacturer.
CAUTION!
Verify that pin patterns match before
attempting to connect cables to the actuator.
2.
Apply input power to the amplifier.
CAUTION!
Motor RMS current must be maintained
at a level below the continuous current rating of the GTX
Series actuator or damage to the motor stator will result.
The peak current setting must be maintained at a level
below the peak current rating of the GTX Series actuator or
damage to the motor stator will result.
3.
Input key motor parameters into the amplifier settings.
NOTES:
•
Some drives require motor files to be input. For
additional guidance regarding amplifier-specific settings
or operation, consult the amplifier manufacturer.
•
Motor parameters and motor files can be found on the
Exlar website.
• Set peak current less than two times the current rating
on the actuator label.
4.
Enable the amplifier.
5.
Download parameters to the amplifier.
6. Run “auto-tune” or “auto-commutate” to double-check
alignment.
7.
If necessary, re-download parameters to the amplifier.
8. In Jog mode, index the actuator rod at 10% of the rated
actuator speed.
9. Check to ensure the linear distance traveled matches the
theoretical distance based upon motor revolutions and
roller screw lead.
10. Review end-of-travel limits internal to the actuator and set
maximum revolutions per extend/retract direction to ensure
end-of-travel limits are not reached.
CAUTION!
Do NOT exceed the actuator’s physical
travel limits. End-of-stroke impacts can cause permanent
damage to the actuator.