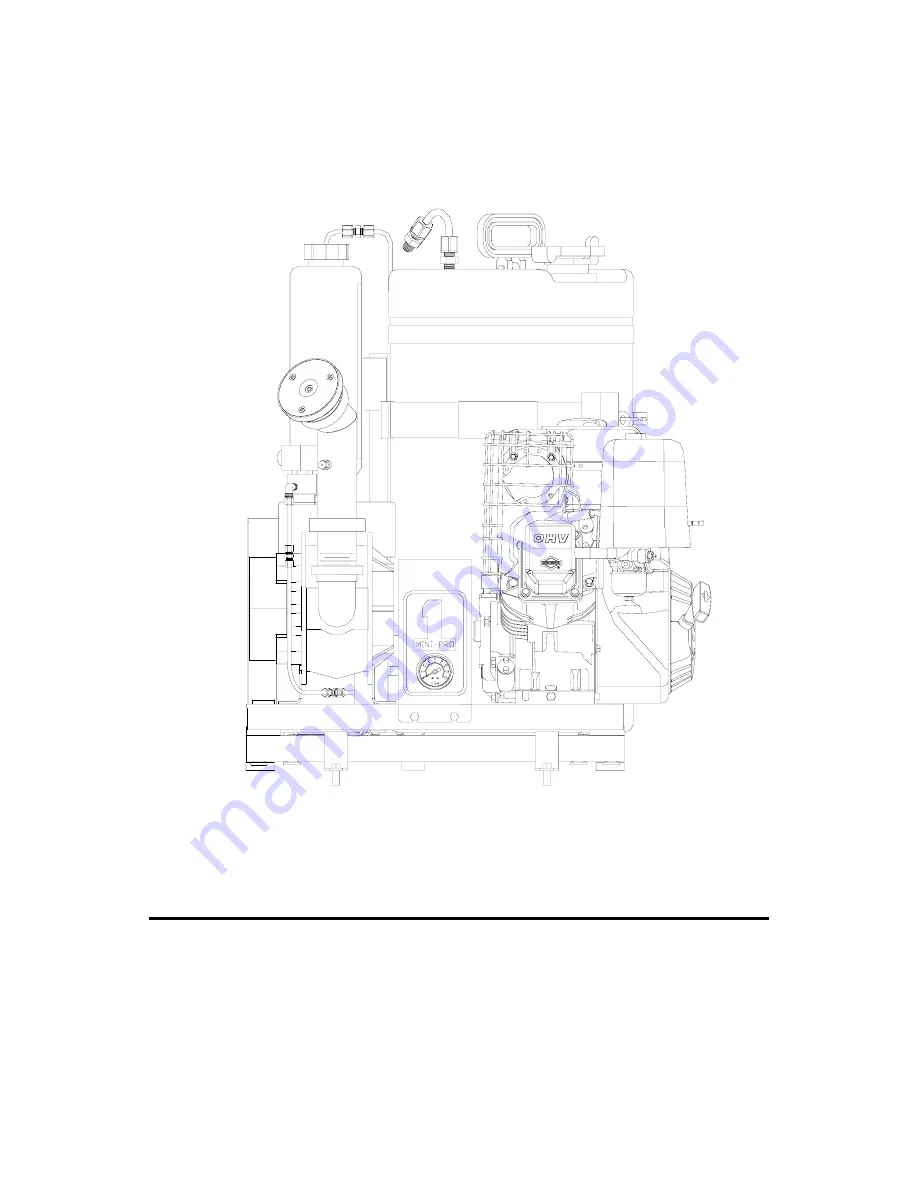
DYNA-FOG
MINI-PRO 8HP
MODEL 2992 SERIES 3 (DIAPHRAGM PUMP)
ULV AEROSOL APPLICATOR
MANUFACTURED BY :
CURTIS DYNA-FOG, Ltd.
17335 U.S. Highway 31 North
WESTFIELD, INDIANA, U.S.A.
INNOVATORS OF SPRAYING AND FOGGING DEVICES
OPERATION, MAINTENANCE AND SPARE PARTS MANUAL
MACHINE SPECIFICATIONS
FOR MINI-PRO 8HP
TM
, MODEL 2992, SERIES 3
TM
®