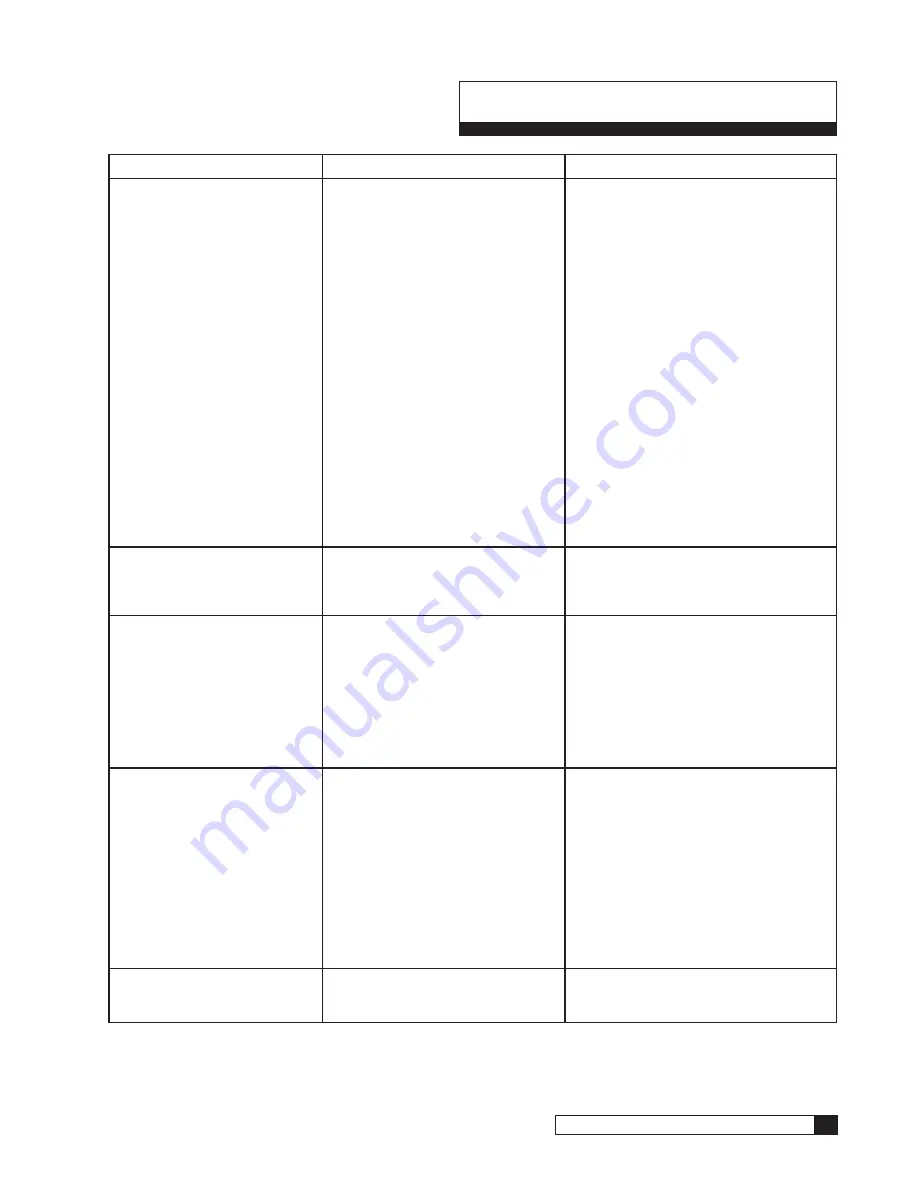
Troubleshooting
47
Cat. No. 01024000
Troubleshooting
Problem
Cause
Solution
Low Water Quality
1. Monitor or Cell Malfunction.
2. Lower grade chemicals cause resin
fouling.
3. Commercial grade caustic will foul an-
ion resin within 2 to 3 regenerations.
4. Inhibited muriatic acid will foul cation
resin.
5. Regeneration temperature too low—
below 50° F.
6. Insufficient amount of acid and /or
caustic used.
7. Percentage of acid and/or caustic too
low.
8. Inadequate regeneration time.
9. Incorrect service flow rates.
10. Organic fouling of anion strong base
resin.
11. Hardness fouling of anion strong base
resin.
1. Check performance and replace.
2. Verify that the acid and caustic used meets
required specifications.
3. Change caustic soda to proper type and
percentage.
4. Change acid to commercial grade 20°Be.
5. Use a blending valve to increase water
temperature.
6. Determine actual amount of chemical used,
and increase time as required.
7. Check inlet water pressure. Low pressure
will cause low flow rates, and high pressure
will cause high flow rates.
8. Short time cycles will not allow enough
chemical. Adjust times accordingly.
9. High flow rates do not allow enough contact
time with resin. Slow down service flow
rate. Low flow rates cause channeling. Use
recirculation pump.
10. Clean up anion resin.
11. Clean up anion resin.
Low Capacity
1. Change in supply. Increase in TDS
reduces gallonage throughput.
2. Increase in water usage.
1. Get updated water analysis and recalculate
gallons between regenerations.
2. Re-evaluate actual water usage using a
water meter
Will Not Draw Chemical—
Acid or Caustic
1. Rate set valves in chemical line
closed.
2. Caustic soda too cold will not flow
through tubing.
3. Solenoid Coil burned out.
4. Air locked in upper piping sytem
1. Adjust valves to obtain proper amount of
chemical draw.
2. Add heat belt to drum—caustic must be
above 65° F, preferably 90° F.
3. Check coil with ohm meter—if the meter
reads no resistance then coil should be
replaced.
4. Turn off the pumps and relieve the air from
the upper piping system.
Air Pumps Are Not Pumping
1. The chemical container is empty.
1. Refill chemical container.
2. Inlet water pressure fluct/–
10 psi.
2a. Install inlet pressure regulator.
2b. Regen system at off-peak time.
3. Air supply limited on scfm.
3a. Supply must be 8–10 scfn,
3b. Regen system at off-peak time.
3c. Dedicated air compressor.
4. Chemical feed lines size.
4. For long-distance feed lines 25–50 ft., feed
line size should be 1.5 times that of the pump
inlet fitting size.
5. Air in chemical feed lines.
5. Disconnect the feed line to inlet to the pump
and remove air from feed line.
Water Flow to Drain
During Service
1. Drain diaphragm or solenoid valves
1a. Identify where water is flowing from and re-
place diaphragm valve.
1b. Replace air solenoid valve on air manifold.