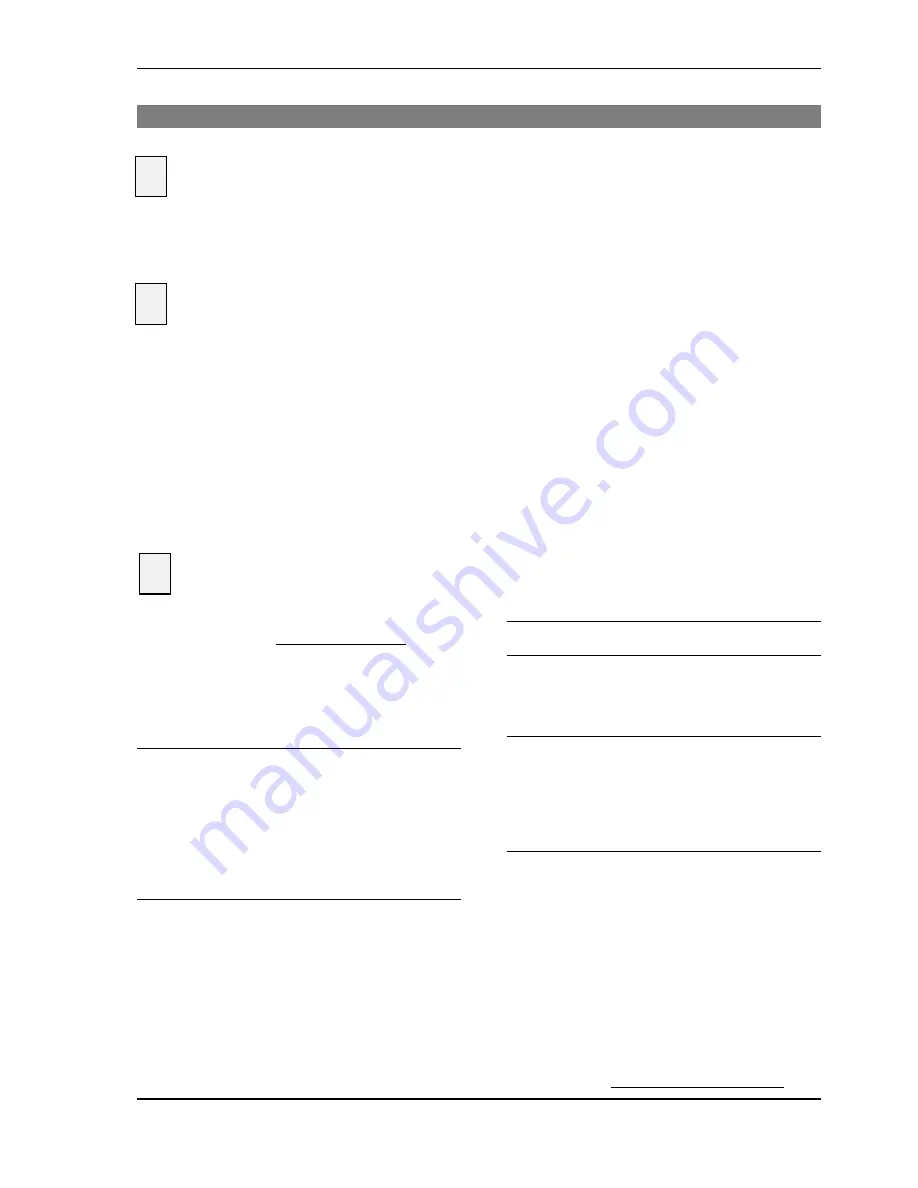
CTA
Instruction Manual
MPE
Reference: MT0027DA
This document may be modified without prior notice
6
Revision date: 11/05/06
Even partial reproduction is prohibited without authorisation in writing
3
Installation
The installation procedures described in this chapter must only be executed by qualified personnel.
The following procedure must be scrupulously respected or the safety of all staff could be at risk.
3.1
Inspection
Immediately after unpacking the drier, check that it is undamaged. If necessary, make a damage claim to
the carrier who delivered the equipment.
Never install or use an appliance damaged during shipment.
3.2
Handling
If using hoists to lift the equipment make sure they are safe. To prevent accidents, check that all chains, hooks,
rings, slings, etc., are in good condition and suitable for the load. They must be tested and approved as
stipulated in local safety regulations. Cables, chains and ropes should never be attached directly to the lift
lugs. Always use a correctly positioned ring or a hook. Lay out the lift so that hoisting cables do not form
excessively tight curves.
Use a bar to avoid side loads on hooks and lugs. Stand at a safe distance away from the load while it is being
lifted. Ensure that lift accelerations and velocities are within safety limits and never leave a load suspended
longer than necessary.
3.3
Layout
Throughout installation, stop compressed air production of to avoid risks to installation personnel.
1.
The dryer should be installed on a flat surface
suitable for the weight of the appliance in a
closed, dry, room which cannot freeze. Access
to the room must be restricted to qualified
maintenance and test personnel. The room
must be sufficiently ventilated with clean air free
from flammable gases or solvents. The drier must
not be exposed directly to heat sources. The
temperature of the room must not exceed 43C°.
Minimum and maximum ambient temperatures are
specified on the manufacturer's plate on the
drier. Unless otherwise stated, dryers are
designed to function in ambient conditions at a
temperature of 25C°. Higher temperatures may
reduce the capacity of the drier and result in an
increase in the dew point. Usually this does not
cause a problem if the compressed air network is
also in higher ambient temperature conditions.
2.
Check that the drier is not surrounded by
equipment which does not comply with
European electromagnetic compatibility
directives as interference could deteriorate
appliance operation. Leave a minimum 1 m
space between the drier and all other electrical
appliances.
3.
Leave adequate space around the drier for
maintenance. Position the drier to ensure that
cooling air cannot recirculate towards the
suction ports. Check that the drier does not suck
in hot air from the compressor cooling systems,
the final cooler or any other appliance.
Remark: The cooling air used by the dryer comes in by the rear
grid and comes out by the front grid
4.
The position of the drier in the compressed air
distribution system depends on the way the
compressed air will be used (see installation
plan).
−
The drier must be installed downstream from the tank if the
compressor pumps intermittently or if total demand for air
does not exceed the total compressor flow rate capacity (the
usual case).
−
The drier should be installed upstream from the tank if the tank
has been dimensioned to permit wide fluctuations in
compressed air demand or if peak demand exceeds
maximum compressor flow rate capacity.
5.
Fit by-pass valves between the drier inlet and
exhaust so that maintenance can be carried
out without having to shut down the
compressed air supply to the network (see
diagram below). During installation, the
upstream and downstream valves must be
closed.
6.
Additional fittings
- fit a class 4* type P solid pollutants filter (15m,
µ8mg/m3) upstream from the drier
- fit a class 1* type S total oil 1filter (0.01mg/m3)
downstream from the drier to remove dust and
oil from the compressed air. Only use filters
equipped with an automatic purge system.
!
!
!