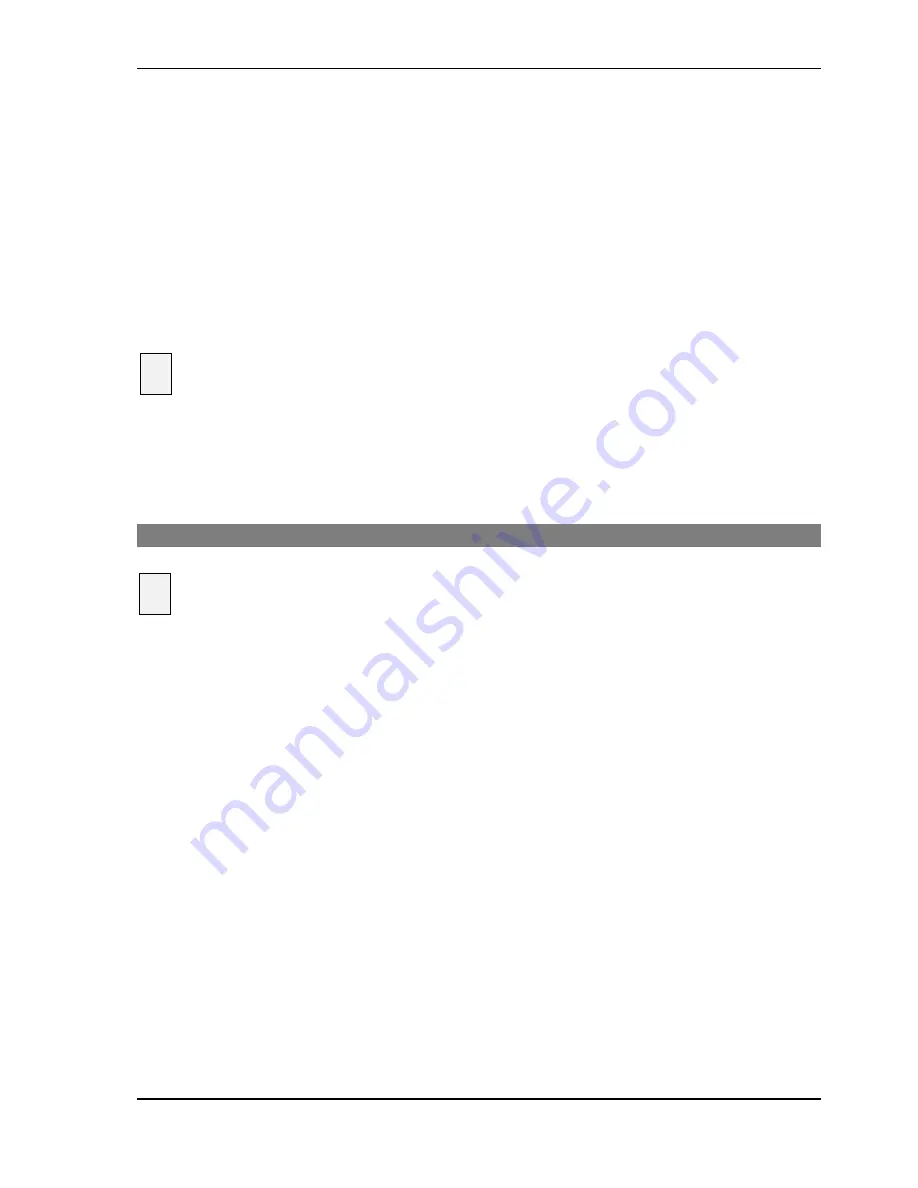
CTA
Instruction Manual
MPE
Reference: MT0027DA
This document may be modified without prior notice
12
Revision date: 11/05/06
Even partial reproduction is prohibited without authorisation in writing
MPE 010 to 125
1.
Replace the upper panel by sliding it forwards to engage the lock tabs. Screw up the rear screws of the
upper panel.
Otherwise, replace the front panel by sliding it downwards to engage the lock tabs. Screw up the lower
screws of the front panel.
Then
2.
Unlock the power supply cut-out switches.
3.
Unlock the upstream and downstream valves and the by-pass valve.
You can now start up the drier and return it to the network.
6.4
Start-up and return to the network
After stopping the drier and disconnecting all circuits (see §4.1), follow the procedure below to return it to
service.
Various risks (projection, explosion, noise...) When starting the drier, the valves upstream and
downstream from the drier must be CLOSED and the by-pass valve must be OPEN.
1.
Set the master switch of the drier to I.
2.
Slowly open the downstream valve.
Take care: any rapid variation in pressure could damage the drier.
3.
Slowly open the upstream valve.
4.
Slowly close the by-pass valve.
7
Maintenance operation
Various risks (electrocution, explosion...): The following operations must only be carried out by
personnel qualified in electrical and pneumatic systems.
The operations described in § 4.1 and 4.2 must be carried out BEFORE maintenance.
The operations described in § 4.3 and 4.4 must be carried out AFTER maintenance.
7.1
Cleaning the purge filter*
General comments
The solenoid purge valve is protected by a filter to prevent damage to the solenoid valve seals from metal
particles or dust. This filter must be cleaned 1 week after the first start-up and then once per month. If this is
not done, the filter will clog and it will not be possible to purge the system correctly. Liquid phase water will
appear in the compressed air network.
Procedure
1.
Close the manual valve on the purging line (see the refrigeration/pneumatic circuit diagram)
2.
Unscrew the filter lock nut.
3.
Withdraw the metal mesh, clean and refit.
4.
Check the good condition of the seal and replace if necessary
5.
Screw up the filter lock nut.
6.
Open the manual valve on the purging line.
*You must comply with the recommendations at the beginning of this chapter.
!
!