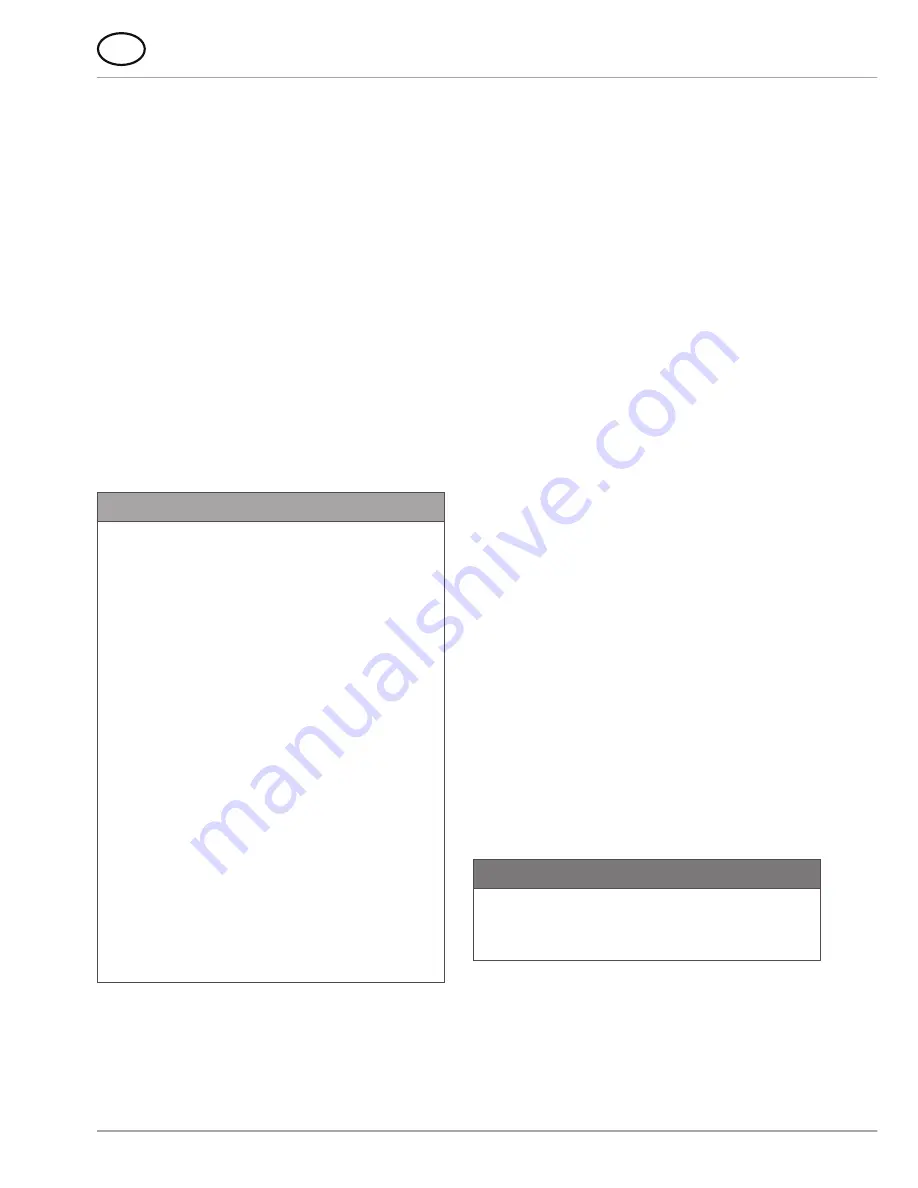
15
MAB 465
GB
Drilling with core drills
When drilling with core drills, proceed as
follows:
Insert the appropriate ejector pin into
the core drill and insert the core drill
into the tool holder (2).
Position and fix the machine at the
location of use.
Switch on the clamping magnet and
check the magnetic holding force (see
section
“Activating/deactivating the
magnetic clamp”
).
Select a suitable speed and switch on
the machine.
Direct the drill to the material with the
handle (9).
NOTE
Observe the following instructions when
drilling with core drills:
►
Drilling with core drills does not require
great force. The drilling process is not
accelerated by higher pressure. The
drill wears faster and the machine can
be overloaded.
►
Use the high-performance BDS 5000
cutting oil in the cooling lubricant sys-
tem of the machine.
►
The cooling lubricant system cannot
be used when working overhead. In
this case, use the high-performance
ZHS 400 grease spray. Spray the drill
on the inside and outside before drill-
ing. In the case of larger drill depths,
repeat this procedure.
►
Make sure that swarf is removed regu-
larly. With larger drilling depths, break
up the swarf.
Thread cutting
The machine is equipped with reversible
direction of rotation and can also be used for
cutting threads.
In order to cut threads, proceed as follows:
Drill the hole for the thread.
Switch off the machine and set the
lowest gear stage and speed.
Set the direction of rotation to clock-
wise (right = R) at switch (24).
Insert the drill tap from below into the
tool holder (2) of the machine.
Switch on the machine and place the
drill tap onto the drilled hole.
Use the hand lever (9) without exerting
pressure to guide the machine until the
desired thread length has been cut.
Switch off the machine and set the
direction of rotation to anti-clockwise
(left = L) at switch (24).
Switch on the machine again and allow
the drill tap to completely emerge out
of the workpiece. Then use the hand
lever (9) to guide the machine slide
upwards in order to avoid damaging
the top of the thread.
Reaming/counter-sinking
Thanks to its wide range of operating
speeds, the machine can also be used for
reaming or counter-sinking.
ATTENTION
►
When reaming and counter-sinking,
observe the limits stated in the techni-
cal data for the tools to be used.
Using
WWW.CSUNITEC.COM