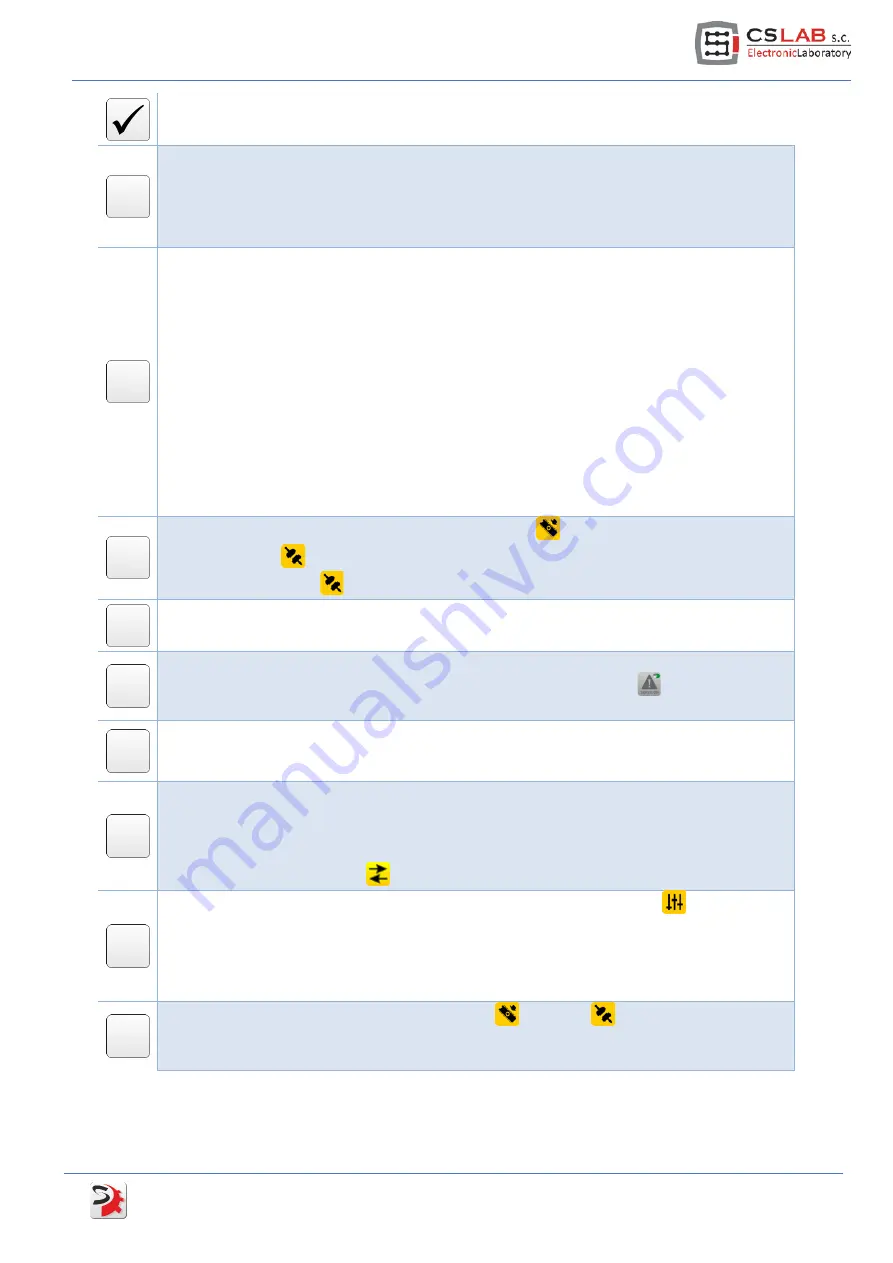
Operation name
Verify motion control STEP/DIR signals operation. For that select from the list in parameters
monitor window - "Reference Position" and make a move in CNC software (it does not
matter if the motor will not move at the moment as there is no power on a power output
stage). "Reference Position" counter should increase or decrease its value - it depends on
motion direction in CNC software.
If it is a motor bought from CS-Lab s.c. and configuration template had been loaded before -
you can skip this point.
Open motor parameters configuration window and set the parameters:
•
Motor type
•
Nominal voltage and current values and nominal revs.
•
Pole pairs number
•
Resistance and inductance of windings. If it is unknown - enter 0.
•
Torque and voltage constants (if unknown - enter 0).
•
Encoder counting direction and pulses number per encoder rev incl. all edges. it's a
value usually presented by a manufacturer as x4 (e.g. if it stays 2500 on the encoder
for us it mean 10 000)
•
Set HALL signals negation if necessary.
Save the configuration in non-volatile memory with
button, close the connection in
csServoManager
and switch off the 24V power supply for min. 5s. Next switch it on and
connect with the drive
.
Open PID regulators tuning window and ensure that the needed values in there are safe for
the first run (look at chapter 5.6.1 - „Initial settings of PID regulator")
Enable power output stage voltage (HV) and open "JOG I/O control" window. Next click
„Reset”. The drive should change its status into "Ready", next - click
- the drive should
change its status into "Running".
Test the motion on low revs (about 50-100 rev/min) – few revs left and right. If a motor
doesn't move or it jerks and/or it reports an error then verify connection and settings again
(especially motor parameters configuration).
If you want to use automatic PID regulators tuning function - skip this point.
In „JOG I/O Control” go to "Motion planner" tab. Set speed to 150RPM, 3000 RPM/s
acceleration and relative motion as pulses number per encoder rev - it's range of 1 motor
rev. Next - start cyclic motion
.
Launch automatic PID regulator tuning in "PID regulator tuning" window"
on "Automatic
tuning" tab or tune the regulators manually as following:
•
current regulator
•
speed regulator
•
position regulator
Save the configuration in non-volatile memory
and click
to disconnect the drive.
Verify if the drive works properly when CNC controller and software control the motion (e.g.
Mach3 and CSMIO/IP). If everything works fine the drive is ready to work.
simDrive™ AC Servo Drive -
U
SER
G
UIDE
7