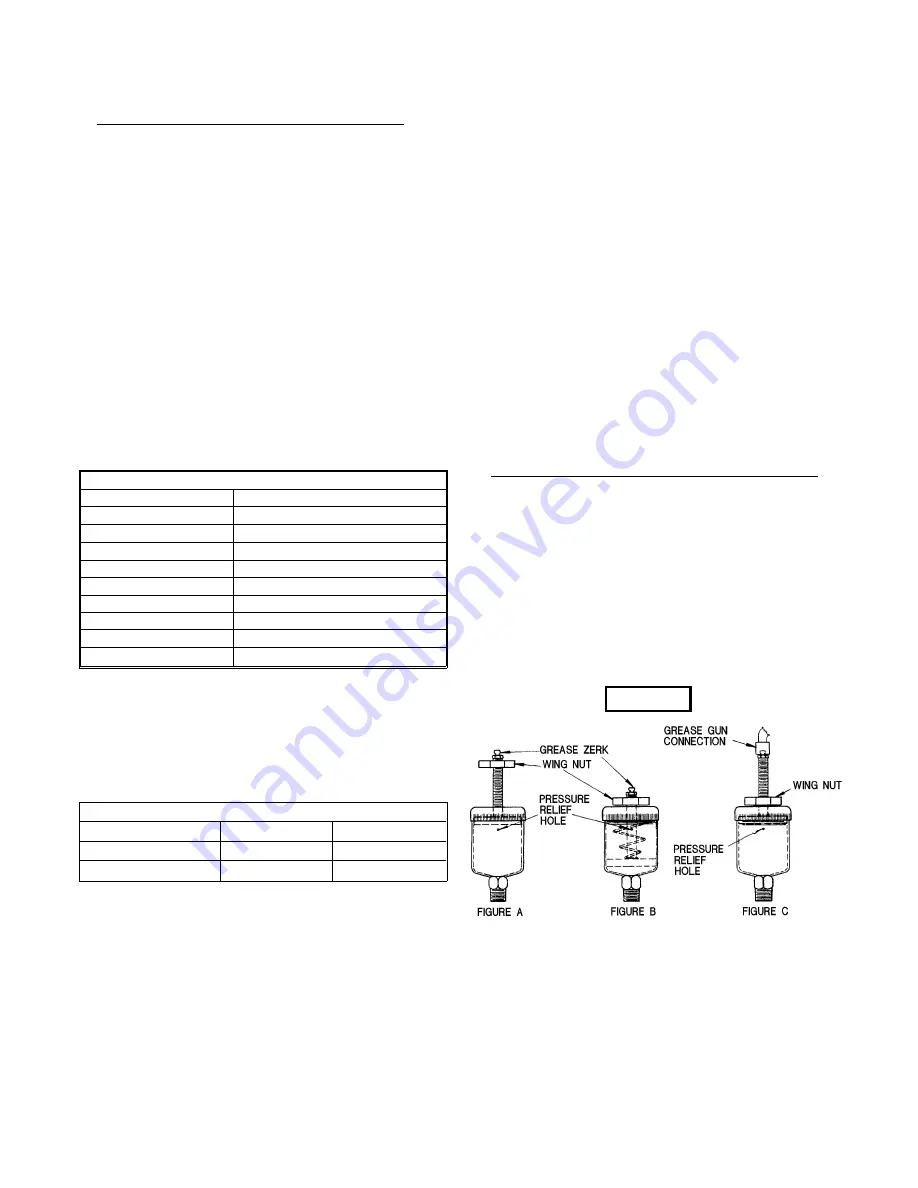
SECTION D: OPERATION RECOMMENDATIONS
The automatic AUTO-PRIME dry priming system fills the pump
case with liquid while starting the pump. A self priming pump
does require the liquid level in the case to at least cover the eye
of the impeller. Operate engine at sufficient speed to prime the
pump. Generally the pump will prime faster if the engine is
operated at a fast speed, rather than at idling speed. The
AUTO-PRIME systems removes air and/or water vapor from
pump case and suction line. Automatic priming and repriming
at 30 ft. vertical suction lifts and on long suction lines.
2. Place the self-feeding grease lubricator in operation by
turning the wing nut on the threaded plunger shaft counter
clockwise as far as it will go.
Do not force the plunger into
the grease cup as this can cause a seal failure.
See
Maintenance Recommendations, Paragraphs 1 and 2 for
instructions on filling the grease cup.
3. Before starting check compressor oil. The oil should be
changed once a month under normal operation. See Table 1.
TABLE 1 - COMPRESSOR OIL
SUPPLIER
GRADE
Amoco Oil Co.
Amocon 32 & 68
Shell Oil Co.
Shell Turbo T Oils 32, 68 & 100
Exxon Co.
Exxon Teresstic Oils 32 & 100
Mobil Oil Co.
Mobil SHC 500
Huls
Anderol 497
Cheveron Oil Co.
Cheveron GST 46 & 68
Pennzoil Oil Co.
Pennzbell TO Oils 32, 46 & 68
Texaco Lubricants Co.
Regal Oil R&O 32 & 68
Pacer Lubricants Division
Thermal "T" Oils
These oils have been approved for use in Emglo Compressors.
Use of these oils will extend the life of the compressor and
insure proper performance and lubrication. NOTE: Oils
numbered 32 & 46 are for winter use. Oils numbered 68 & 100
are for summer use.
Oils or fluids that should
NOT
be used in Emglo Compressors.
DO NOT USE
Transmission Fluid
Hydraulic Fluid
Vegetable Oil
Power Steering Fluid
Used Oil
Brake Fluid
Automotive Motor oil
Gear Oil
Scented Oil
4. Before starting the engine, check engine crankcase to see
that it has the proper amount of lubricating oil. Also, check the
fuel tank for sufficient fuel.
Refer to the engine instruction
manual for proper engine maintenance.
5. In cold weather operation, the pump will not freeze as long
as it is running. However, it may freeze if it is not drained while
standing idle. To drain the pump, remove the drain plugs at the
bottom of the pump case and rotate the impeller at least once
to assure removal of all the water.
6. To obtain more capacity or pressure, increase the speed of
the engine.
7. The discharge of a self priming centrifugal pump may be
closed briefly without damaging the pump. However, the water
will soon heat up and this can damage the pump seal.
8. It is not desirable to run the pump without liquid in the pump
case. If the pump must be run in order to check the operation
of the engine or motor, fill the case with sufficient water to keep
the rotating seal wet. This will eliminate damage to the seal and
other pump parts.
9. If the pump has been idle for some time, the impeller may
appear to be stuck or locked in place. This is usually caused
by a film of rust or dirt between the impeller and the volute. A
little extra force on the crank may break it loose. If not, the pump
must be dismantled.
SECTION E: MAINTENANCE RECOMMENDATIONS
E-1) MECHANICAL SEAL - Grease lube - (Std)
1. A self-feeding lubricator is provided to supply grease to the
shaft seal of the pump on pumps with single seals (See Fig. 1).
The grease cup is empty when the wing nut, positioned at the
outer end of the threaded plunger shaft, recedes to the cap of
the grease cup. To refill the grease cup, rotate the wing nut
clockwise as far as it will go, attach a zerk gun to the zerk fitting,
then fill until grease oozes from the relief hole on the side of the
cup. For operation, return the wing nut to the end of the plunger.
Never force the plunger into the grease cup as this can
cause seal failures.
2. A #1 grease is normally recommended. However, where
high ambient temperatures are encountered, such as direct
sunlight, a #2 grease can be used. Use a water resistant,
nonfiberous grease. Lithium base greases are excellent and
molydisulfide is acceptable. Normally, the sodium soap base
greases are the only non-water resistant types that are not
acceptable for mechanical seal lubrication.
Figure 1
FULL
EMPTY
REFILL POSITION
7
Summary of Contents for CT4QP Series
Page 14: ...Pump Model CT4QP 14...
Page 17: ...Pump Models CT6QP PO6LB 10N 17...
Page 20: ...NOTES 20...