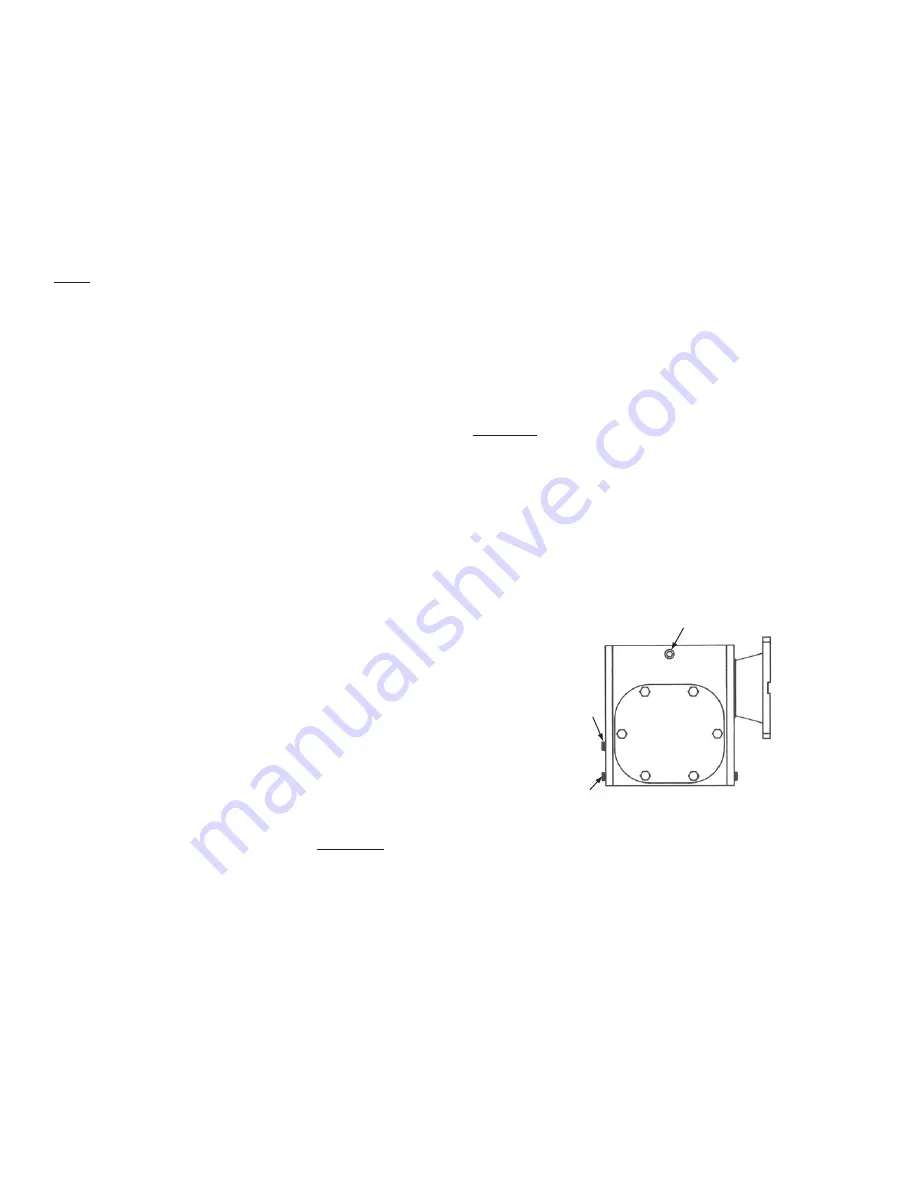
K. FINAL ROTARY LIMIT SWITCH ADJUSTMENT
After the run speed, creep speed and ACCEL & DECEL
have been adjusted, the fi nal limit switch settings can be
made.
(a) Actuate the operator controls and adjust the
rotary limit switches (LSO & LSC) to stop the
door in the full open and closed positions.
(b) Actuate the operator and adjust the rotary limit
switches (LSCO & LSCC) to initiate the creep
mode at the desired time. Keep in mind that the
operator only travels in creep mode as long as
the cam lobe is depressing the snap switch.
Note: The length of time the operator is running in creep
mode must be long enough to allow for it to dynamically
brake from run speed to creep speed plus the desired
length of time the operator is traveling under creep
mode. If the DECEL time is set for too long, the creep
mode may be adversely affected.
(c) After adjusting LSCO & LSCC check the travel of
the door. LSC & LSO may need to be re-adjusted.
(d) Activate the operator to open and close the door
several
times
and
fi ne tune the limit switch
settings.
(e) Close limit switch cover and tighten down screw
clamp.
(f) Periodically the limit switches may require
adjustment. This is especially evident during the
initial few weeks after start up due to chain
stretch and wear in.
L. FINAL ADJUSTMENTS & CHECKS
(1) Make a fi nal check of operator, Chain Tensioner,
sliding door hardware, sag roller(s) and idlers. It is
extremely important that the operator be run several
times to check chain alignment. Make corrections as
needed.
3. MAINTENANCE
A. GENERAL
To insure that the electric operator is ready for operation
at all times, it must be inspected systematically which will
preclude serious damage or failure. Proper adjustment
and lubrication must be maintained and checked as
recommended below.
B. LUBRICATION
(1) LUBRICATION FOR GEARMOTOR
(a) Figure 16 shows the proper location of vent, oil
level, and drain plugs.
(b) The drive unit is pre-lubricated and shipped with
Mobil "SHC 634" synthetic lubricant. This oil is a lifetime
lubricant rated for operation in ambient temperatures
ranging from -40°F to +125°F.
(2) Every 900 cycles, where one cycle consists of
opening and closing of the door, or every 3 months
whichever comes fi rst, clean and lubricate the chain with
a SAE lubricant as required for ambient temperature.
C. PREVENTIVE MAINTENANCE
To prevent damage or improper operation, the following
inspections should be let made at least EVERY 6
MONTHS.
(1) Check oil level by removing the oil level plug. Oil
should be up to the bottom of the plug hole.
(2) Check tension of chain.
(3) Check all electrical components and wiring for
tightness.
(4) Check clutch to see that it doesn’t slip under
normal
operation.
(5) Check all bolts and nuts for tightness.
VENT PLUG
OIL LEVEL
PLUG
DRAIN
PLUG
Figure 7.
A. TO ORDER REPLACEMENT PARTS
(1) SEND IN SERIAL NUMBER OF ELECTRIC
OPERATOR.
(2) SPECIFY the number of pieces needed.
(3) Order by part number and name of part.
(4) State whether to ship by freight, truck, parcel
post, or air express.
(5) State whether transportation charges are to be
prepaid or collect.
(6) Give name and address of the person or
company to whom the parts are to be shipped.
(7) Give name and address of person or company to
whom the invoices to be sent.
4. PARTS
Crown Industrial Operators • 213 Michelle Ct. • So. San Francisco, Ca 94080-6202
Phone: (650) 952-5150 • Fax: (650) 873-1495
www.crown-industrial.com Email: [email protected]
G-2001
6