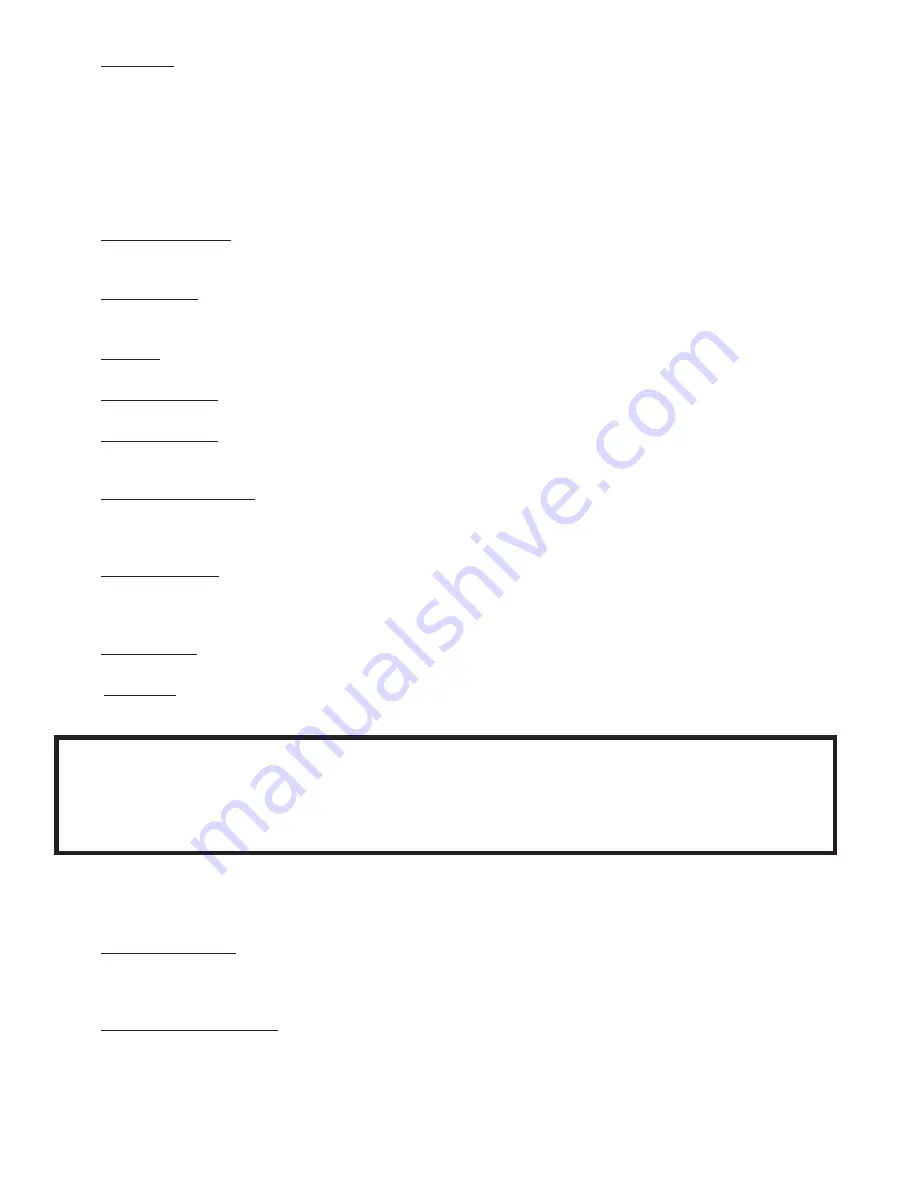
20
1)
Relief valve (Required) - Mount the relief valve on the top left side of the boiler as shown in Figure 8.1 using the 3/4”
nipple provided. The relief valve shipped with the boiler is set to open at 30 psi. This valve may be replaced with one
having a pressure up to the “Maximum Allowable Working Pressure” shown on the rating plate. If the valve is replaced,
the replacement must have a relief capacity in excess of the DOE heating capacity for the boiler.
Pipe the discharge of the relief valve to a location where water or steam will not create a hazard or cause property damage
if the valve opens. The end of the discharge pipe must terminate in an unthreaded pipe. If the relief valve discharge is not
piped to a drain, it must terminate at least 6 inches above the floor. Do not run relief valve discharge piping through an
area that is prone to freezing. The termination of the relief valve discharge piping must be in an area where it is not likely
to become plugged by debris.
2)
Circulator (Required) - Figure 8.1 shows the ideal location of the circulator which is in the supply piping immediately
downstream of the expansion tank. A less ideal, but acceptable, location for most residential circulators is in the return (if
this is done, be sure that adequate clearance exists to open the door.
3)
Expansion Tank (Required) - If this boiler is replacing an existing boiler with no other changes in the system, the
old expansion tank can generally be reused. If the expansion tank must be replaced, consult the expansion tank
manufacturer’s literature for proper sizing.
4)
Fill Valve (Required) - Either a manual or automatic fill valve may be used. The ideal location for the fill is at the
expansion tank.
5)
Automatic Air Vent (Required) - At least one automatic air vent is required. Manual vents will usually be required in
other parts of the system to remove air during initial fill.
6) Low Water Cut-Off (Required by some codes) - The 3250-Plus control supplied with this boiler is a listed low water
cut-off that will prevent burner operation in the event that there is insufficient water in the boiler. It can be set for either
automatic or manual reset operation (see Part XIII for more details)
7) Manual Reset High Limit (Required by some codes) - This control is required by ASME CSD-1 and some other codes.
Install the high limit in the boiler supply piping just beyond the boiler with no intervening valves. Set the manual reset
high limit as far above the operating limit setting as possible, but not over 240°F. Wire the control to break the 120 VAC
electrical supply to the boiler.
8) Flow Control Valve (Required under some conditions) - The flow control valve prevents flow through the system unless
the circulator is operating. A flow control valve may be necessary on converted gravity systems to prevent gravity
circulation. Flow control valves are also used to prevent “ghost flows” in circulator zone systems through zones that are
not calling for heat.
9) Isolation Valves (Optional) - Isolation valves are useful if the boiler must be drained, as they will eliminate having to drain
and refill the entire system.
10) Drain Valve - The drain valve is shipped in the boiler parts bag. Install it in the tee on the boiler return as shown in
Figure 2.0.
NOTICE
The 1-1/2” plugged tapping on the bottom rear section is present for manufacturing purposes
only. Do not attempt to use this tapping as a return connection.
Piping for Special Situations
Certain types of heating systems have additional requirements. Some of the more common variations follow:
1)
Indirect Water Heaters - Figure 8.2 shows typical indirect water heater piping. Boiler piping is the same as for any two-
zone system. Figure 8.2 shows circulator zoning, which is usually preferred for indirect water heaters. Size the circulator
and indirect water heater piping to obtain the boiler water flow through the indirect water heater called for by the indirect
water heater manufacturer.
2)
Large Water Volume Systems - The piping shown in Figure 8.3 will minimize the amount of time that the boiler operates
with return temperatures below 120°F on these systems. A bypass is installed as shown to divert some supply water
directly into the return water. The bypass pipe should be the same size as the supply. The two throttling valves shown are
adjusted so that the return temperature rises above 120°F during the first few minutes of operation. A three-way valve can
be substituted for the two throttling valves shown.
Summary of Contents for TWB Series
Page 2: ......
Page 12: ...10 FIGURE 4 1 FIELD INSTALLATION OF FLUE BAFFLES...
Page 18: ...16 FIGURE 6 4 ALLAIR FROM OUTDOORS USING HORIZONTAL DUCTS INTO BOILER ROOM...
Page 23: ...21 FIGURE 8 3 BOILER BYPASS PIPING FIGURE 8 2 INDIRECT WATER HEATER BOILER SIDE PIPING...
Page 31: ...29 FIGURE 11 0 CONNECTIONS DIAGRAM BOILERS WITH OR LESS TANKLESS HEATER...
Page 51: ...49...
Page 53: ...51...
Page 54: ...52 SERVICE RECORD DATE SERVICE PERFORMED...
Page 55: ...53 Notes...