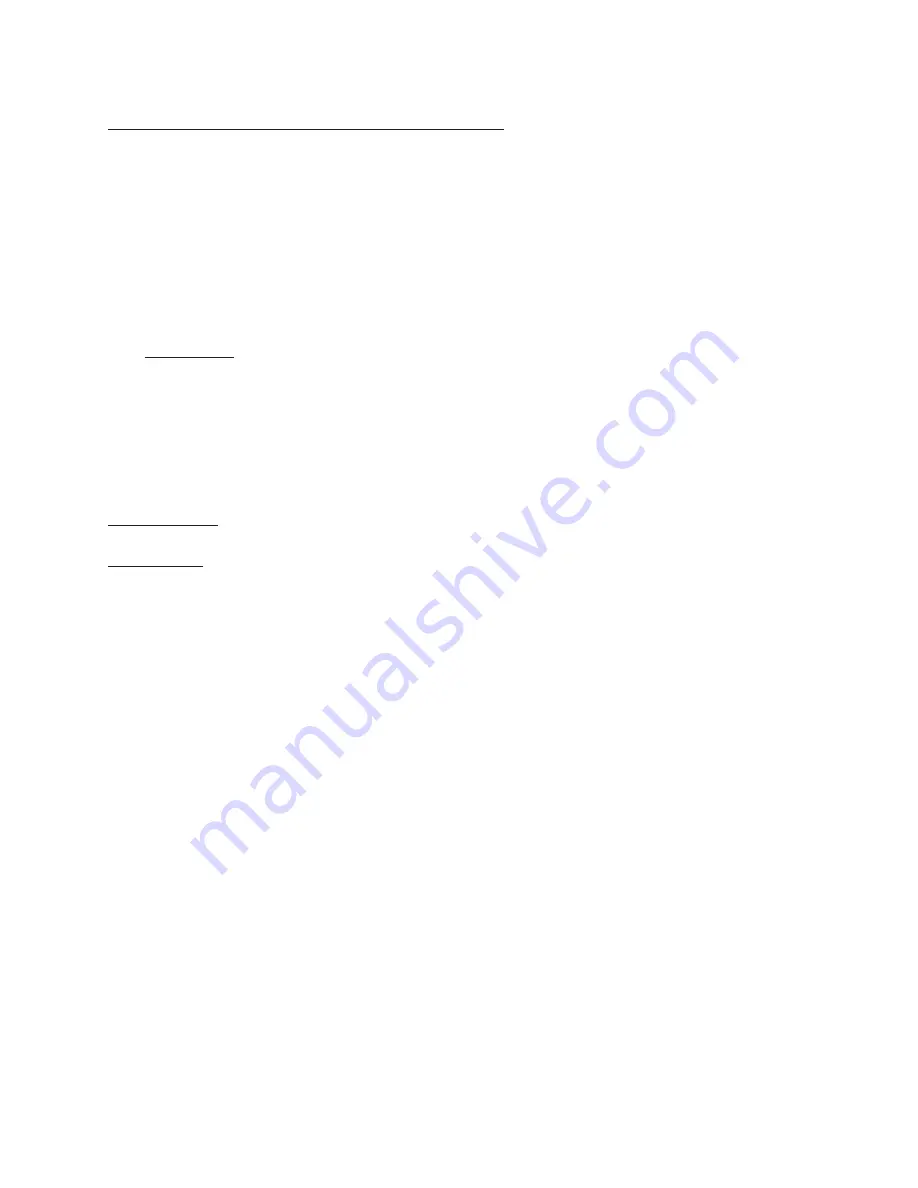
13
A. For Buildings of Other than Unusually Tight Construction
1) Determine whether the boiler is to be installed in a confined space - A confined space is defined as having a volume less
than 50 cubic feet per 1000 BTU/hr input of all appliances installed in that space. To determine whether the boiler room is a
confined space:
a) Total the input of all appliances in the boiler room in thousands of BTU/hr. Round the result to the next highest 1000
BTU/hr.
b) Find the volume of the room in cubic feet. The volume of the room in cubic feet is:
Length (ft) x width (ft) x ceiling height (ft)
In calculating the volume of the boiler room, consider the volume of adjoining spaces only if no doors are installed
between them. If doors are installed between the boiler room and an adjoining space, do not consider the volume of the
adjoining space, even if the door is normally left open.
c) Divide the volume of the boiler room by the input in thousands of BTU/hr. If the result is less than 50, the boiler room is
a
confined space
.
Example:
An FWZ080 and a water heater are to be installed in a room measuring 6 ft - 3 in x 7 ft with an 8 ft ceiling. The
water heater has an input of 30000 BTU/hr:
Input of FWZ080 = 0.80 Gal/hr x 140000 BTU/Gal = 112000BTU/hr
Total input in thousands of BTU/hr = (112000 BTU/hr + 30000 BTU/hr)/1000 = 142
Volume of room = 6.25 ft x 7 ft x 8 ft = 350 ft
3
350/142 = 2.46. Since 2.46 is less than 50, the boiler room is a confined space.
2) Unconfined Space - Natural infiltration into the boiler room will normally provide adequate air for combustion and ventila
-
tion without additional louvers or openings into boiler room.
3) Confined Space - Provide two openings into the boiler room, one near the floor and one near the ceiling. The top edge of the
upper opening must be within 12” of the ceiling and the bottom edge of the lower opening must be within 12” of the floor
(Figure 6.0).
•
Each opening must have a free area of 1 square inch per 1000 BTU/hr input of all fuel burning appliances in the boiler
room. The minimum opening dimension is 3 inches. Minimum opening free area is 100 square inches per opening.
•
If the total volume of both the boiler room and the room to which the openings connect is less than 50 cubic feet per
1000 BTU/hr of total appliance input, install a pair of identical openings into a third room. Connect additional rooms
with openings until the total volume of all rooms is at least 50 cubic feet per 1000 BTU/hr of input.
•
The “free area” of an opening takes into account the blocking effect of mesh, grills, and louvers. Where screens are
used, they must be no finer than ¼” (4 x 4) mesh.
B. For Buildings of Unusually Tight Construction
1) Openings must be installed between the boiler room and the outdoors or a ventilated space, such as an attic or crawl space,
which communicates directly with the outdoors.
2) Two openings are required. The top edge of the upper opening must be within 12 inches of the ceiling. The bottom edge of
the lower opening must be within 12 inches of the floor.
3) Size openings and ducts as follows:
•
Vertical ducts or openings directly outdoors (Figure 6.1, Figure 6.2, and Figure 6.3) - Each opening must have a free
cross sectional area of 1 square inch per 4000 BTU/hr of the total input of all fuel fired appliances in the boiler room but
not less than 100 square inches. Minimum opening size is 3 inches.
•
Openings to outdoors via horizontal ducts (Figure 6.4) - Each opening must have a free cross sectional area of 1 square
inch per 2000 BTU/hr of the total input of all fuel fired appliances in the boiler room but not less than 100 square inches.
Minimum opening size is 3 inches.
•
The “free area” of an opening takes into account the blocking effect of mesh, grills, and louvers. Where screens are
used, they must be no finer than ¼” (4 x 4) mesh.
Summary of Contents for FWZ Series
Page 2: ......
Page 12: ...10 FIGURE 4 2 BAFFLE AND BLANKET INSTALLATION...
Page 23: ...21 FIGURE 8 1 INSTALLATION OF FACTORY SUPPLIED PIPING FIGURE 8 2 STANDARD BOILER PIPING...
Page 25: ...23 FIGURE 8 4 BYPASS PIPING FIGURE 8 5 ISOLATION OF BOILER FROM SYSTEM WITH A HEAT EXCHANGER...
Page 28: ...26 FIGURE 9 2 TWO PIPE GRAVITY FEED SYSTEM NOT RECOMMENDED FIGURE 9 3 TWO PIPE LIFT SYSTEM...
Page 31: ...29 FIGURE 10 0 WIRING CONNECTIONS DIAGRAM FOR HYDROSTAT 3250 PLUS CONTROL...
Page 32: ...30 FIGURE 10 1 CONNECTIONS WIRING DIAGRAM FOR BURNER SPECIFIC PRIMARY CONTROL...
Page 52: ...50...
Page 55: ...53...