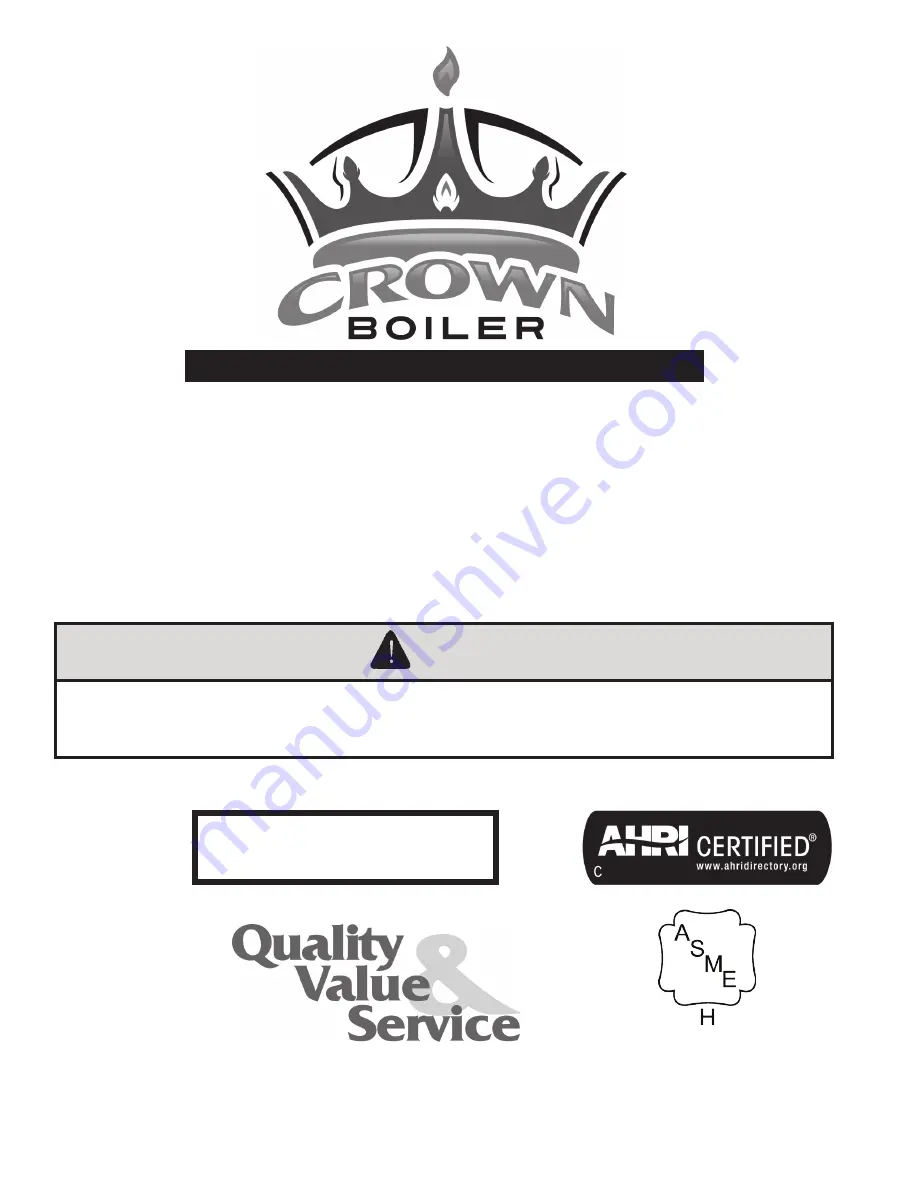
FWZ Series
Oil-Fired Hot Water Boilers
INSTALLATION INSTRUCTIONS
These instructions must be affixed on or adjacent to the boiler
D
E S I G N E D T O
L
E A D
9802605 Rev A, 06-18
Crown Boiler Company
P.O. Box 14818
3633 I Street
Philadelphia, PA 19134
www.crownboiler.com
WARNING
Improper installation, adjustment, alteration, service or maintenance can cause property damage,
injury, or loss of life. For assistance or additional information, consult a qualified installer, service
agency or the gas supplier. This boiler requires a special venting system. Read these instructions
carefully before installing.
Models:
•
FWZ060
•
FWZ080
•
FWZ081
•
FWZ100
•
FWZ130
•
FWZ160
Equipped with Hydrolevel
3250-Plus Control System
Summary of Contents for FWZ Series
Page 2: ......
Page 12: ...10 FIGURE 4 2 BAFFLE AND BLANKET INSTALLATION...
Page 23: ...21 FIGURE 8 1 INSTALLATION OF FACTORY SUPPLIED PIPING FIGURE 8 2 STANDARD BOILER PIPING...
Page 25: ...23 FIGURE 8 4 BYPASS PIPING FIGURE 8 5 ISOLATION OF BOILER FROM SYSTEM WITH A HEAT EXCHANGER...
Page 28: ...26 FIGURE 9 2 TWO PIPE GRAVITY FEED SYSTEM NOT RECOMMENDED FIGURE 9 3 TWO PIPE LIFT SYSTEM...
Page 31: ...29 FIGURE 10 0 WIRING CONNECTIONS DIAGRAM FOR HYDROSTAT 3250 PLUS CONTROL...
Page 32: ...30 FIGURE 10 1 CONNECTIONS WIRING DIAGRAM FOR BURNER SPECIFIC PRIMARY CONTROL...
Page 52: ...50...
Page 55: ...53...