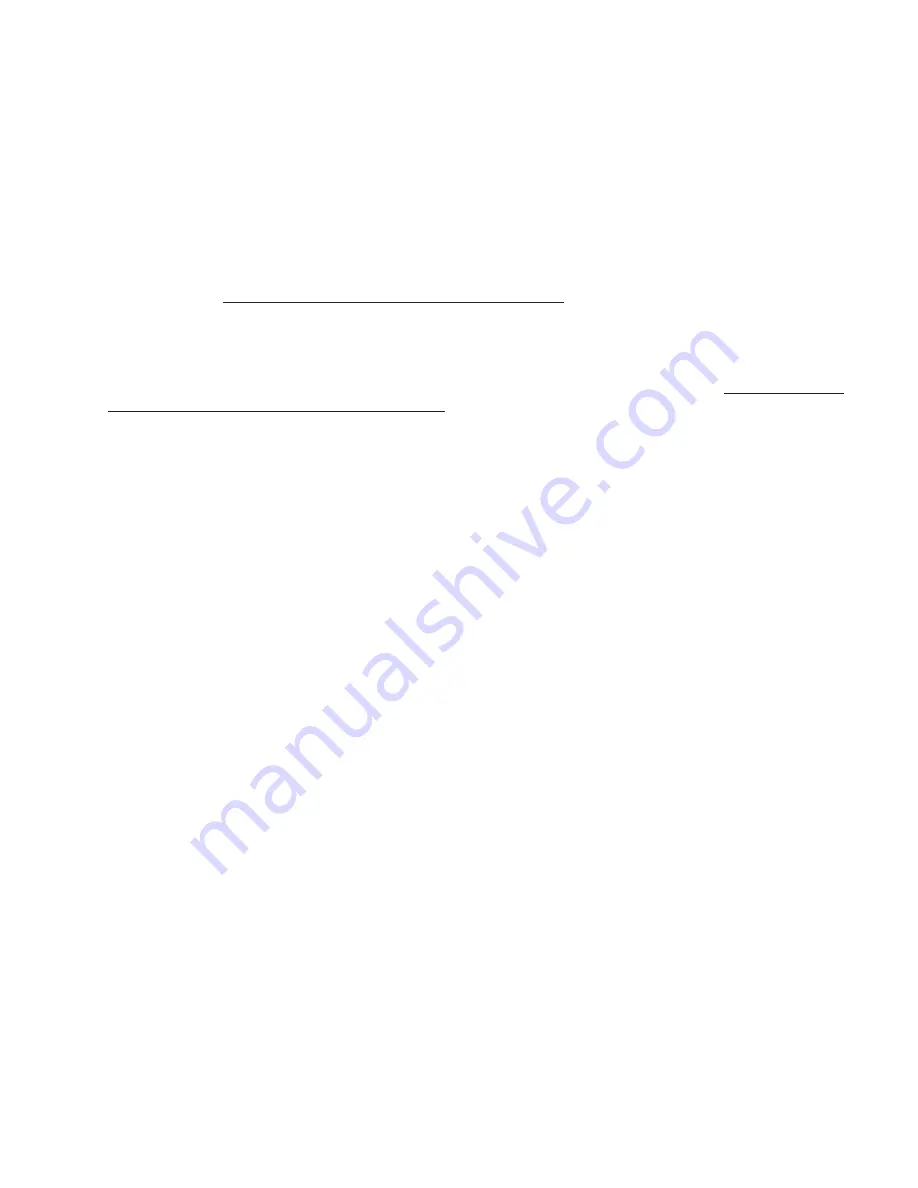
17
The vent installation must be in accordance with local building codes, or the local authority having jurisdiction. Contact your
local fire and building officials on specific requirements for restrictions and the installation of fuel oil burning equipment. In
the absence of other applicable codes, the vent system installation must meet the requirements of NFPA 31 –
Standard for the
Installation of Oil-Burning Equipment
and NFPA 211 -
Standard for Chimneys, Fireplaces, Vents, and Solid
Fuel-Burning
Appliances
. Vent systems in Canada must comply with CSA B139-04 –
Installation Code for Oil-burning Equipment
.
A typical vent system is illustrated in Figure 7.0. The components of the vent installation are the vent connector (breeching),
barometric draft regulator, and chimney.
1) Acceptable Chimneys - The following chimneys may be used to vent a FWZ series boiler:
•
Listed Type L vent - Install in accordance with the manufacturer’s instructions, the terms of its listing, and applicable
codes.
•
Masonry Chimney - The masonry chimney must be constructed in accordance with the latest edition of
Standard for
Chimneys, Fireplaces, Vents, and Solid Fuel Burning Appliances
(NFPA 211) and lined with a clay liner or other listed
lining system. Do not vent a FWZ series boiler into an unlined chimney
.
2) Acceptable Vent Connectors - The following may be used for vent connectors:
•
Listed Type L vent.
•
Single Wall Galvanized Pipe - Use 0.018” (26 gauge) or heavier.
3) Chimney and Vent Connector Sizing - See Table 7.1 for minimum vent connector and chimney sizing.
The vent connector
size must not be smaller than boiler flue collar diameter
.
4) Do not vent this appliance into any portion of a mechanical vent system operating under positive pressure.
5) Do not connect the boiler into a chimney flue serving an open fireplace or other solid fuel appliance.
6) Prior to boiler installation, an existing chimney must be inspected by a qualified person in accordance with the requirements
of Chapter 11 of NFPA 211,
Standard for Chimneys, Fireplaces, Vents, and Solid Fuel-Burning Appliances
. This inspection is
intended to identify safety problems with the chimney such as obstructions, a missing or damaged liner, or leak points. Clean
chimney as necessary and correct any other chimney defects before installing the boiler.
7) Vent connector must slope upward from boiler not less than one inch in four feet. No portion of vent pipe should run
downward or have sags. Vent connector must be securely supported.
8) The vertical section of vent connector coming off the boiler should be as tall as possible, while still maintaining the proper
clearance from the horizontal vent connector to combustibles and the proper pitch called for in (7) above.
9) Vent connector must be installed above the bottom of the chimney to minimize risk of blockage.
10) Vent connector must be inserted flush with inside face of the chimney liner and the space between vent connector and
chimney sealed tight. A thimble permanently cemented in place can be used to facilitate removal of vent connector for
cleaning.
11) Install the barometric draft regulator supplied with this boiler in accordance with the regulator manufacturer’s instructions.
No other draft regulator shall be used. Mount the barometric draft regulator in the side connection of a tee (not supplied).
12) Secure all joints in the vent connector system with sheet metal screws. This includes the joint between the vent connector and
the boiler collar (see Figure 7.0, Detail ‘A’), as well as the barometric draft regulator. Use at least three screws at each joint.
Summary of Contents for FWZ Series
Page 2: ......
Page 12: ...10 FIGURE 4 2 BAFFLE AND BLANKET INSTALLATION...
Page 23: ...21 FIGURE 8 1 INSTALLATION OF FACTORY SUPPLIED PIPING FIGURE 8 2 STANDARD BOILER PIPING...
Page 25: ...23 FIGURE 8 4 BYPASS PIPING FIGURE 8 5 ISOLATION OF BOILER FROM SYSTEM WITH A HEAT EXCHANGER...
Page 28: ...26 FIGURE 9 2 TWO PIPE GRAVITY FEED SYSTEM NOT RECOMMENDED FIGURE 9 3 TWO PIPE LIFT SYSTEM...
Page 31: ...29 FIGURE 10 0 WIRING CONNECTIONS DIAGRAM FOR HYDROSTAT 3250 PLUS CONTROL...
Page 32: ...30 FIGURE 10 1 CONNECTIONS WIRING DIAGRAM FOR BURNER SPECIFIC PRIMARY CONTROL...
Page 52: ...50...
Page 55: ...53...